Automatisierung
von Bestandsmaschinen und -anlagen
Automatisierte Fertigung
auch mit Bestandsmaschinen
Neu ist nicht immer besser.
Auch bestehende Werkzeugmaschinen lassen sich in eine automatisierte Umgebung integrieren und dadurch flexibler, effizienter und vernetzter betreiben. Der Schlüssel dazu: das perfekte Zusammenspiel von Mensch, Maschine und flexibler Automation.
So können Sie auch mit Ihren vorhandenen Maschinen gestiegene Kundenerwartungen, komplexere Werkstücke und schwankende Nachfrage mühelos meistern. Diese Seite bietet Ihnen einen ersten Überblick zum Thema „Automatisierung vorhandener Werkzeugmaschinen“. Für tiefergehende Informationen steht Ihnen ein kostenloser Leitfaden zum Download bereit.
Leitfaden Automatisierung vorhandener Werkzeugmaschinen
Navigation:
1. WELCHE Möglichkeiten der Automatisierung stehen zur Verfügung?
2. WAS spricht dafür, Ihre vorhandene/n Werkzeugmaschine/n zu automatisieren?
3. WIE automatisieren Sie vorhandene Werkzeugmaschinen erfolgreich?
4. Sie möchten tiefer in dieses Thema eintauchen? Holen Sie sich den Leitfaden!
WELCHE
Möglichkeiten der Automatisierung stehen zur Verfügung?
Produktion: Das Zusammenspiel von Mensch, Maschine und IT
Für optimale Ergebnisse müssen alle Komponenten perfekt harmonieren. Automatisierung bedeutet per Definition, menschliche Eingriffe in einen Prozess zu minimieren.
Doch welche Optionen gibt es, um Bestandsmaschinen zu automatisieren?
Die folgende Grafik zeigt die Möglichkeiten je nach Prozess- und Maschinentyp sowie den entsprechenden Automatisierungsgrad.
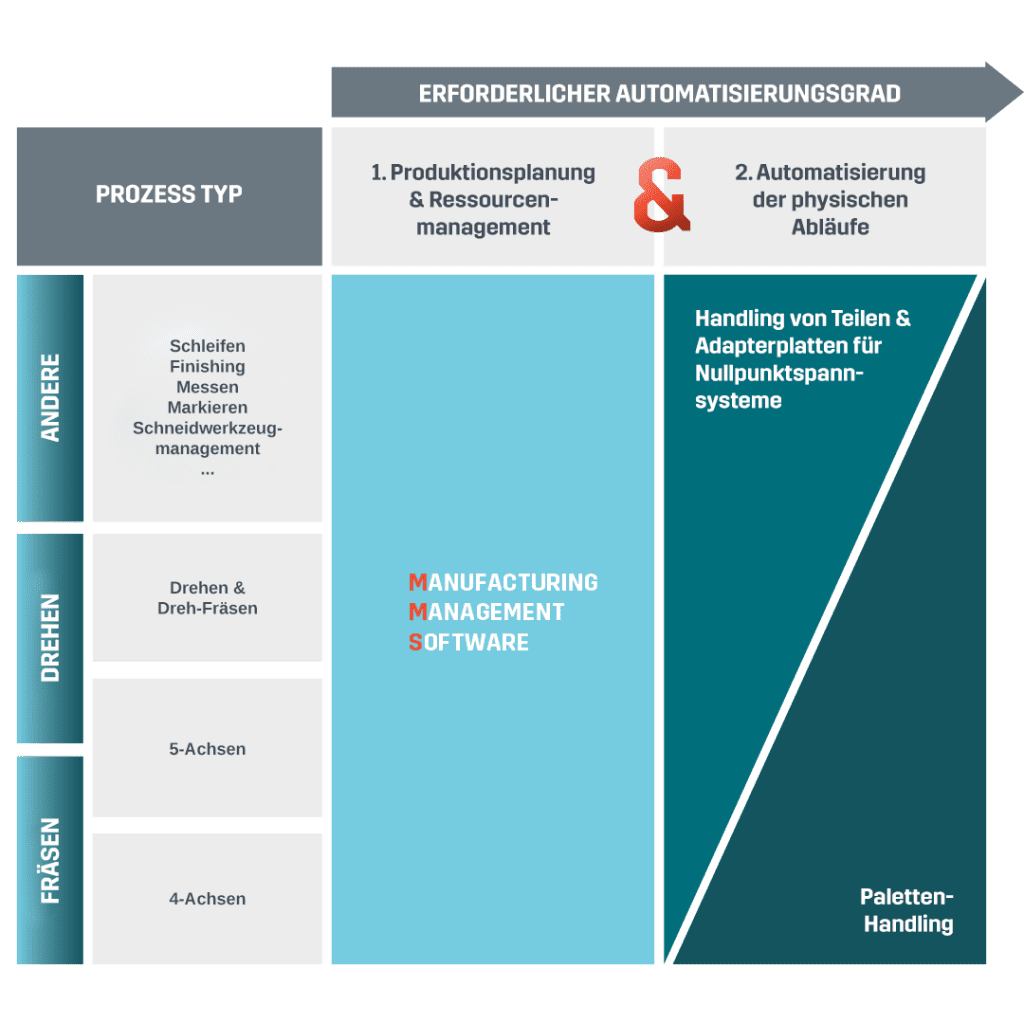
Die Situation im Fertigungsbereich
Die möglichen Optionen für eine nachträgliche Automation hängen von der Ausstattung der zu automatisierenden Bestandmaschine(n) ab. Diese lassen sich für die Automatisierung in folgende Hauptkategorien einteilen:
Standalone-
Werkzeugmaschinen
Bei Standalone-Maschinen ist sowohl das automatisierte Paletten- als auch Werkstückhandling möglich. Darüber hinaus lassen sich die folgenden Funktionen der Manufacturing Management Software MMS, wie die automatische Produktionsplanung und die Ressourcenverwaltung in dieser Automation nutzen.
Werkzeugmaschinen in bestehenden Automationssystemen
Bei Werkzeugmaschinen, die schon Teil eines bestehenden Automationssystems sind, können Hardware-Automation, Prozesseinrichtungen von Drittanbietern oder Funktionen unserer Software MMS, wie automatisierte Produktionsplanung und Ressourcenverwaltung nachgerüstet werden.
Mix aus Standalone-Maschinen und Werkzeugmaschinen in einem bestehenden Automationssystem
Gerade in Unternehmen mit einer umfangreicheren Fertigung ist es nicht ungewöhnlich, eine Automation, die eine Kombination aus Einzelmaschinen und Werkzeugmaschinen in einem bestehenden System ist, zu realisieren.
WAS
spricht dafür, Ihre Bestandsmaschine/n zu automatisieren?
Ganz egal, ob es sich um eine neue oder eine vorhandene Werkzeugmaschine handelt, Hersteller profitieren im gleichen Maße von den Vorteilen einer Automation. Folgende drei Beweggründe für die Automatisierung vorhandener Werkzeugmaschinen konnten wir ermitteln:
- Die vorhandene Produktionskapazität reicht nicht mehr aus und es ist nicht genügend Platz für neue Maschinen. Oder die Anschaffung neuer Werkzeugmaschinen kommt nicht in Frage.
- Sie stellen fest, dass Sie das Potential Ihrer Fertigung hinsichtlich Rentabilität der Produktion, Durchlaufzeiten, Qualität oder das Engagement der Mitarbeiter, noch lange nicht voll ausgeschöpft haben.
- Oder das vorhandene Automationssystem ist nicht auf dem neuesten Stand, verursacht Betriebsstörungen und wird zunehmend zu einem betriebswirtschaftlichen Risiko.
Für einen besseren Überblick haben wir die Vorteile für die Automatisierung von Bestandsmaschinen in diese drei Kategorien eingeteilt:
Maximale Prozesseffizienz
Weniger Leerlaufzeiten, höhere und gleichbleibende Qualität, effektivere und integrierte Prozesse, automatisierte Produktionsplanung und Ressourcenverwaltung und unbemannte Produktionszeiten sind Faktoren, die zu maximaler Prozesseffizienz beitragen.
Zufriedene Kunden & Mitarbeiter
Durch den Einsatz von intelligenter Automation wird die Arbeit für den Bediener zugleich sicherer und anspruchsvoller. Eine hohe und beständige Qualität zusammen mit kurzen und verlässlichen Lieferzeiten garantieren dem Kunden die richtigen Teile zur rechten Zeit in der richtigen Ausführung.
Finanzielle Leistungsfähigkeit
Eine höhere Produktionskapazität,
geringere Lohnkosten und Investitionskosten pro Stück in Verbindung mit geringerem Kapitaleinsatz sind alles Vorteile, die durch Automatisierung vorhandener Werkzeugmaschinen realisiert werden können.
WIE
automatisieren Sie Bestandsmaschinen erfolgreich?
Unser „Leitfaden für die Automatisierung vorhandener Werkzeugmaschinen“ beleuchtet die vier wesentlichen Erfolgsfaktoren für eine erfolgreiche Automation vorhandener Werkzeugmaschinen. Diese sind Projektmanagement, Schnittstellenoptionen und -anforderungen, Schnittstellenentwicklung und Anpassungen in Hardware und Sicherheit.
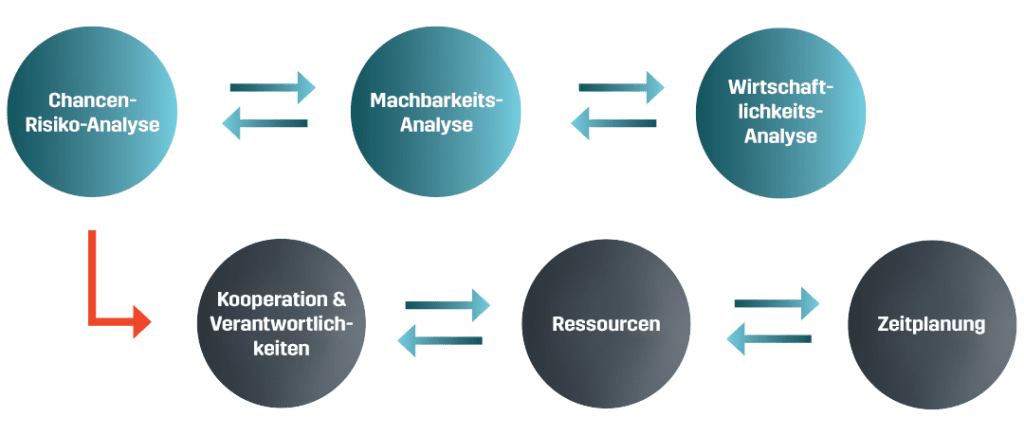
Projektmanagement
Die Automatisierung von vorhandenen Werkzeugmaschinen, wie gehen wir vor? Aus unserer Sicht besteht das Projekt aus einer Vorstudie und der eigentlichen Projektphase, wie links in der Grafik dargestellt. Dabei ist die Vorstudie ein wichtiger technischer Bestandteil des Projekts: Auf Grundlage der in der Vorstudie gesammelten Informationen können die Möglichkeiten, die IST-Situation sowie die Frage, ob für dieses Projekt ein Investmentbudget eingeplant werden soll, detailliert bestimmt werden.
Fällt dann die Entscheidung, das Projekt umzusetzen, werden die einzelnen Zuständigkeiten der am Projekt beteiligten Parteien (Fertiger = Kunde, Automationsanbieter und ggfls. Werkzeugmaschinenhersteller oder -händler (MTB/D)) sorgfältig definiert, das eigentliche Projektteam ausgewählt sowie der Zeitplan vereinbart. Dieser weist auch auf mögliche notwendige Unterbrechungen der Produktion hin.
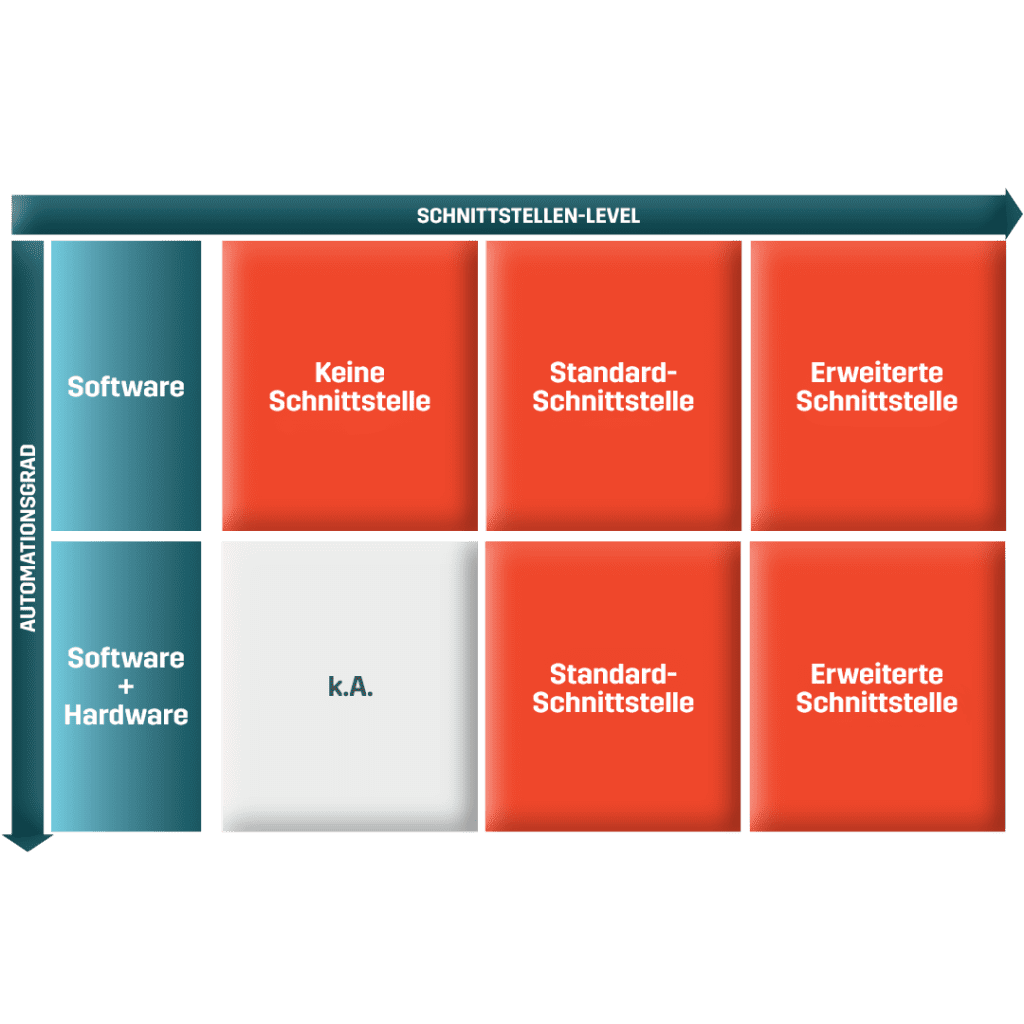
Schnittstellen
Der wohl komplexeste und herausforderndste Teil bei der Umsetzung eines Automationsvorhabens ist die Einbindung der vorhandenen Werkzeugmaschinen. Dabei sind z. B. Anzahl und Typ der Maschinen, das Baujahr und die jeweiligen Versionen der Steuerungs- und Maschinensoftware zu berücksichtigen. Für den Erfolg dieses Vorhabens ist eine enge Zusammenarbeit zwischen dem Werkzeugmaschinenhersteller oder -händler (MTB/D) und dem Automationsanbieter essentiell.
Je nach Aufgabe, die die Automation beim Endkunden erfüllen soll, und der aktuellen IST-Situation im Betrieb, wird die Art und Weise der Anbindung sorgfältig ausgewählt und implementiert. Die Anbindung erfolgt in drei Stufen, die jeweils zu mehr Effizienz und Intelligenz in der automatisierten Produktion führen. Ausführlichere Informationen dazu gibt es in unserem Leitfaden:
Stufe 1 – keine Schnittstelle:
Es gibt weder eine physische Schnittstelle noch eine Verbindung zur Werkzeugmaschine. Dank der Planungs- und Steuerungssoftware wird die Fertigung um eine automatisierte Produktionsplanung und Ressourcenverwaltung erweitert und das Personal entsprechend unterstützt.
Stufe 2 – Standardschnittstelle:
Diese beinhaltet Funktionen wie das Auslesen des Maschinenstatus und die Paletten- oder Teileanlieferung an die Maschine. Herbei wird dem Fertigungsprozess die Überwachung der Produktionskennzahlen und die Standardautomatisierung der Werkzeugmaschine hinzugefügt, so dass z. B. unbemannte Schichten ermöglicht werden.
Stufe 3 – erweitere Schnittstelle:
Durch die Übertragung der NC Programme vom Automationssystem zur Werkzeugmaschine sowie den Austausch der Werkzeugdaten zu und von den Werkzeugmaschinen wird eine vollständige Produktionsplanung und Ressourcenverwaltung ermöglicht, die den Automationsgrad auf das Maximum hebt.
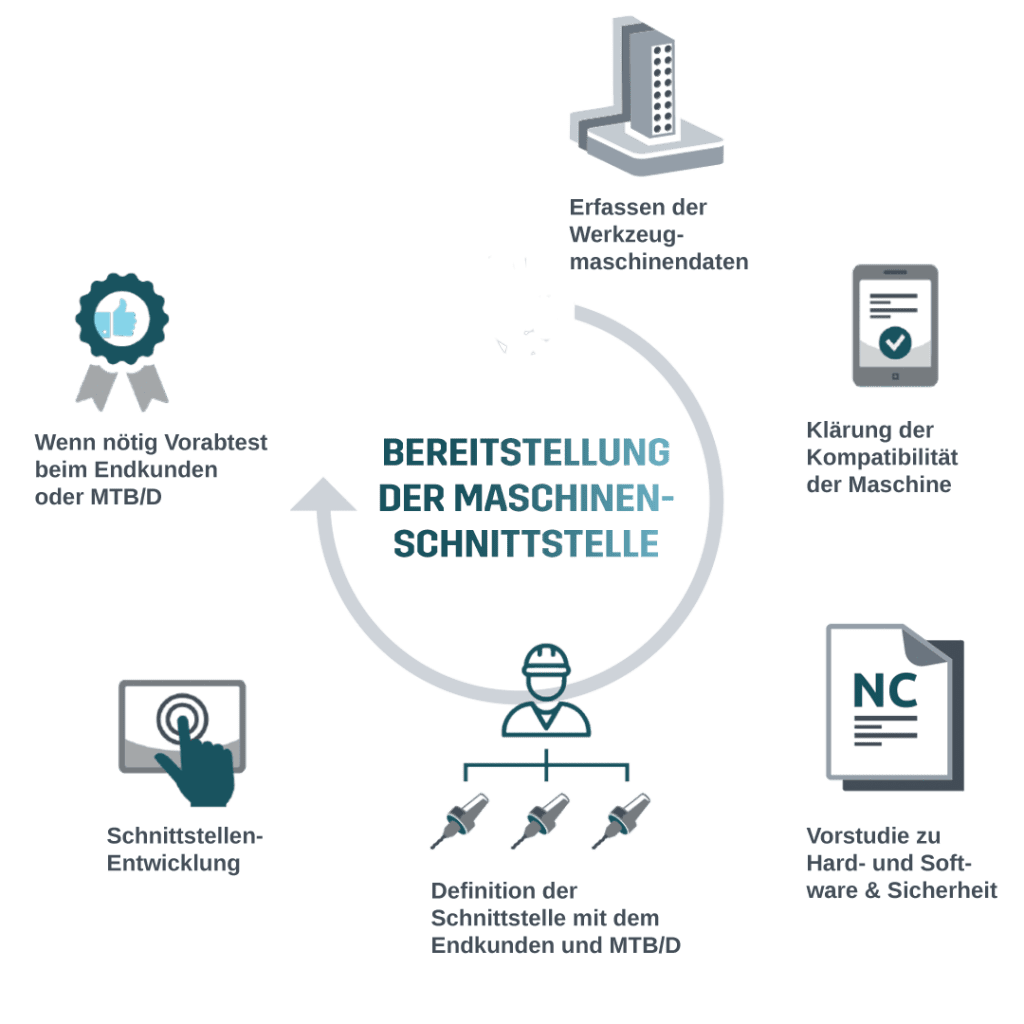
Schnittstellenentwicklung
Für die Automatisierung von vorhandenen Werkzeugmaschinen ist die Schnittstellenentwicklung entscheidend. Dieser Prozess erfolgt in sechs Schritten: (1) Erfassung der Werkzeugmaschinendaten; (2) Klärung der Kompatibilität der Maschine für die angedachte Anbindung, (3) Vorstudie zu Hard- und Software und Sicherheit, (4) Schnittstellendefinition mit dem Endkunden (5) Schnittstellenentwicklung mit dem Maschinenhersteller- o. -händler (MTB/D) und Automationsanbieter, (6) Vorabtest oder Simulation beim Endkunden oder Maschinenhersteller.
Zu Beginn werden Werkzeugmaschinendaten erfasst und dokumentiert, wie z. B. Marke und Modell, vorhandene elektrische und Software-Verbindungen etc. Sind diese Informationen nicht ausreichend, wird zusätzlich eine Vorstudie zu Hard- und Software und Sicherheit durchgeführt. Beide Schritte bringen Klarheit über die Schnittstellenkompatibilität, eine wichtige Grundlage für das gesamte Projekt.
Im Zuge der Schnittstellendefinition stimmen Endkunde, Maschinenhersteller oder -händler (MTB/D) und Automatisierer zusätzliche Soft- und Hardware-Schnittstellenfunktionen ab, die möglicherweise im bestehenden Setup fehlen. Anschließend wird mit den Parteien eine Gesamtspezifikation der Schnittstelle erstellt. Die eigentliche Entwicklung der Schnittstelle erfolgt durch den Automatisierer und Maschinenhersteller oder -händler, basierend auf den zuvor definierten Verantwortungsbereichen.
Nach Abschluss der Entwicklungphase wird je nach Bedarf ein Vorabtest beim Fertiger oder eine Simulation beim Endkunden und Maschinenhersteller oder -händler (MTB/D) durchgeführt.
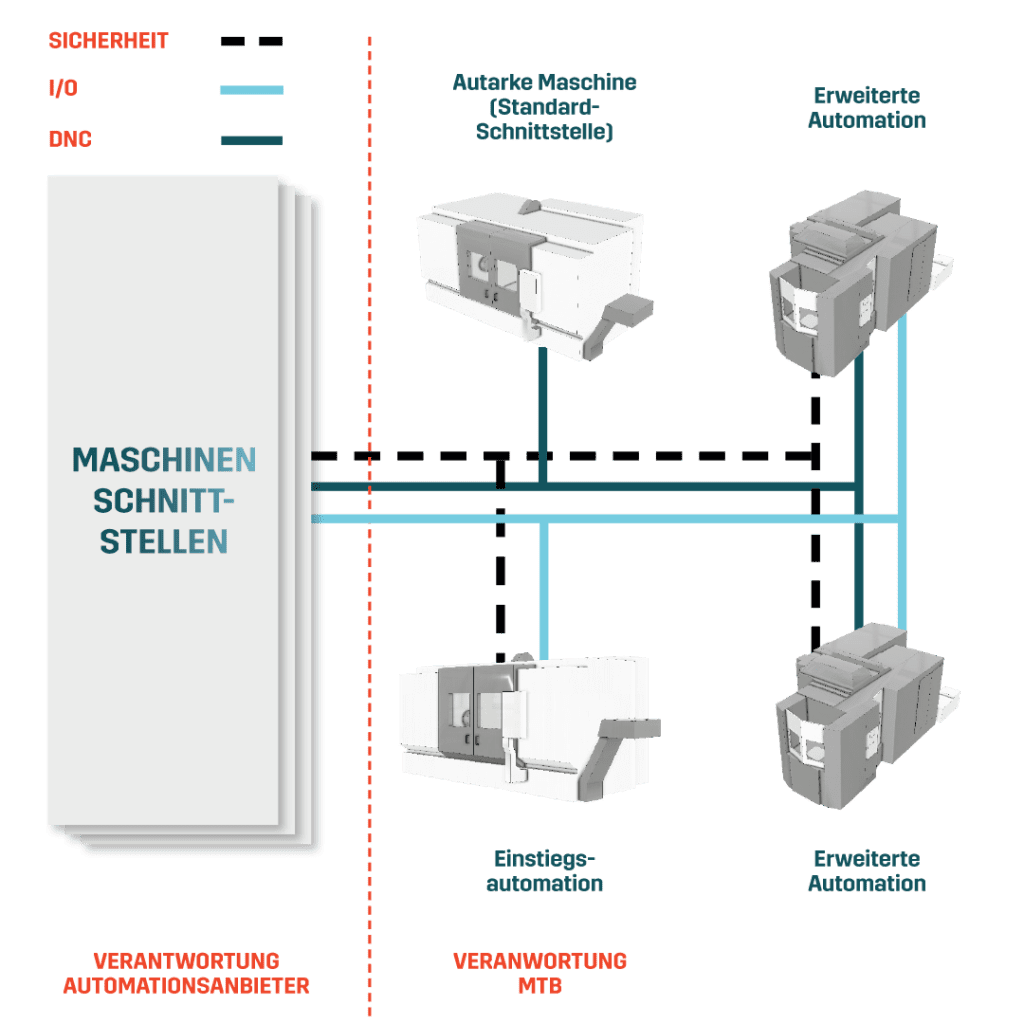
Anpassung von Hardware und Sicherheit
Je nach Automation sind die vorzunehmenden mechanischen Anpassungen der Maschine von Fall zu Fall unterschiedlich. Ausschlaggebende Faktoren dabei sind z. B. ob die Maschine bereits in ein Automationssystems eingebunden ist oder ob sie über einen automatischen Palettenwechsler (APC) verfügt. Notwendige mechanische Anpassungen der Werkzeugmaschinen liegen dabei immer in der Verantwortung des Maschinenherstellers oder -händlers (MTB/D).
Das erforderliche Sicherheitsniveau kann entweder mit vorhandenen Sicherheitsmerkmalen oder durch zusätzliche mechanische Anpassungen oder Anbindung an die Werkzeugmaschine(n) erreicht werden. Bei einer Standardanbindung ohne Automationshardware ist die Maschine selbst für Sicherheitsmerkmale verantwortlich. Bei der Einbindung einer Paletten- oder Teilehandhabungsautomation wird das System so konzipiert, dass es den geltenden Normen und Vorschriften, wie z. B. den von der EU festgelegten Standards, entspricht.
Und wie geht es weiter?
Mit dem Download:
„Leitfaden CNC Automation von bestehenden Werkzeugmaschinen“
Sie denken gerade darüber nach, wie Sie die Herausforderungen Produktionskosten pro Stück, hoher WIP oder Lagerbestand, lange Durchlaufzeiten, Qualitätssicherung und Rückverfolgbarkeit in den Griff bekommen? Dann ist dieser Leitfaden eine wertvolle Unterstützung.
„*“ zeigt erforderliche Felder an
Sie suchen eine passende Lösung?
„*“ zeigt erforderliche Felder an