Die besten Fertigungsunternehmen mit hohem Produktmix erreichen eine Auslastung Ihrer Maschinen von über 90 % – ohne die dass es nötig ist, etwas auf Lager zu produzieren oder Teile nachzuarbeiten, die außerhalb der Toleranzen liegen. Schneidwerkzeuge sind eine der größten Engpässe, die diese Metallzerspaner überwunden haben. Unabhängig davon, ob Ihre Werkzeugmaschinen automatisiert sind oder nicht, die Werkzeug-Managementprozesse sind hier der Schlüssel. Je höher der Produktionsmix und / oder je kürzer die Standzeiten der Werkzeuge sind, desto wichtiger werden diese Prozesse. Basierend auf 40 Jahren Erfahrung in der Automatisierung von Fräs- und Drehmaschinen – und parallel zur Optimierung von Schneidwerkzeugprozessen – möchten wir unsere vier wesentliche Schritte vorstellen, um eine hohe Spindelauslastung und hervorragende Qualität zu erreichen.
Unnötige Kosten durch fehlendes Werkzeug-Management
Wie viele verschiedene Bearbeitungsoperationen führen Sie täglich durch? Und wie viele Werkzeuge benötigt jedes NC-Programm? Sicherzustellen, dass jede Werkzeugmaschine immer den richtigen Satz an Werkzeugen geladen hat – und diese über eine ausreichende Standzeit verfügen – ist das Ziel eines jeden Herstellers und doch oft schwer zu realisieren. Ineffiziente Schneidwerkzeugprozesse verursachen auf vielen Ebenen unnötige Kosten:
- Niedrige Spindelauslastung: Maschinenstopps durch wegen fehlender oder verschlissener Werkzeuge
- Ausschuss, Nacharbeiten und Spindelbrüche: Die Qualität ist ungenügend – im schlimmsten Fall kommt es zu Spindelbrüchen – durch Fehler beim Werkzeugwechsel oder in den Werkzeugdaten.
- Hoher Zeit- und Kostenaufwand: Hohe Investitionen in Ersatzwerkzeuge und Personal, um die beiden zuvor genannten Probleme zu beheben.
Welches sind die ‚best Practices‘ für Schneidwerkzeuge und wie am besten starten?
Wir haben einen 4-stufigen Ansatz entwickelt, um die Werkzeugengpässe bei unseren Kunden in der Fertigungsindustrie zu beseitigen. Die Anzahl der erforderlichen Schritte hängt von der Komplexität der Werkzeugumgebung des Herstellers ab – aber wir empfehlen, dass die ersten beiden Schritte von jedem Hersteller in Betracht gezogen werden sollten. Je weiter Sie gehen, desto besser werden sowohl Ihre Spindelauslastung als auch die Qualität!
Die Schritte im Werkzeugmanagement im Einzelnen:
- Ermöglichen Sie Werkzeug-Setups im Voraus.
- Beseitigen Sie Werkzeuladefehler.
- Automatisieren Sie Ihre Werkzeuge und nutzen diese auf verschiedenen Maschinen.
- Automatisieren Sie die Werkzeug-Setups.
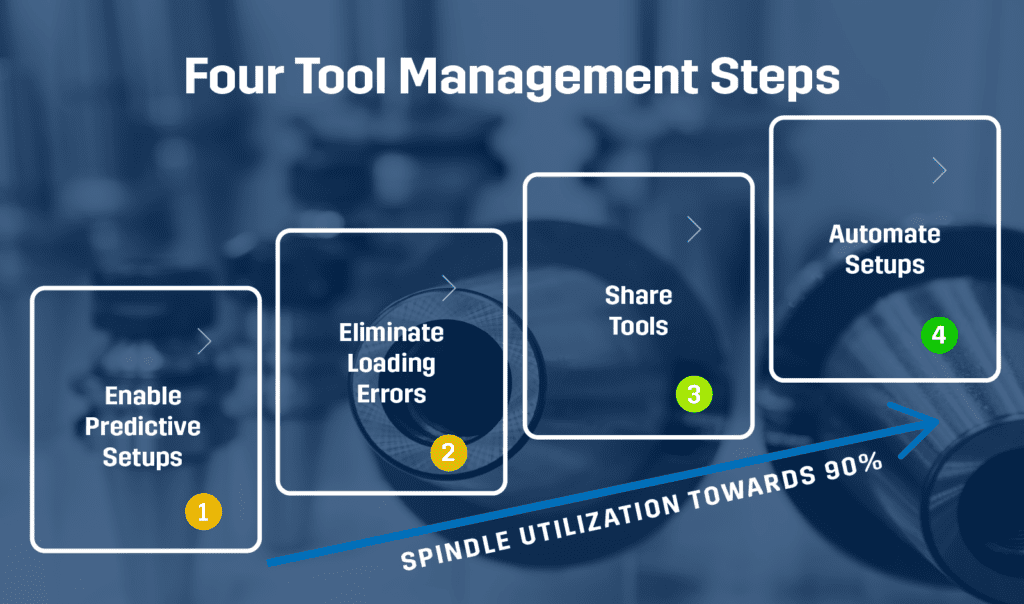
Schritt 1: Werkzeug-Setups im Voraus
Wissen Sie, wann und wo Sie welche Werkzeuge benötigen? Wenn nicht, wird die Statuslampe Ihrer Maschine häufig auflechten, weil eine Werkzeug fehlt oder verschlissen ist. Das Problem in Zahlen ausgedrückt: Wenn Sie vier Bearbeitungszentren mit vier Werkzeugwechseln pro Stunde über zwei Schichten betreiben, wechseln Sie 96.000 Mal im Jahr die Werkzeuge. Wenn 10 % dieser Wechsel eine Wartezeit von 10 Minuten verursachen (=Sie konnten nicht sofort reagieren), standen Ihre Maschinen 1.600 Stunden still. Das sind 18 % Ihres gesamten jährlichen Fertigungspotenzials.
Being able to predict your tool needs based on your machining schedule gives your team an opportunity to (1) prepare the right tools BEDie Fähigkeit, Ihren Werkzeugbedarf basierend auf Ihrem Fertigungsplan vorherzusagen, bietet Ihrem Team die Möglichkeit, (1) die richtigen Werkzeuge VOR Beginn der Bearbeitung vorzubereiten und (2) sicherzustellen, dass dasselbe Werkzeug nicht an zwei Stellen gleichzeitig benötigt wird. Zur Umsetzung benötigen Sie nicht einmal eine Automatisierung, sondern:
- Eine Werkzeug-Bibliothek, in der alle Ihre Werkzeuge erfasst sind.
- Ein Planungstool für Ihre Fertigungsaufträge (ERP, MES oder Automatisierungssoftware).
- Eine Software, die mit den oben genannten Systemen kommuniziert und eine Planung der Werkzeuge mindestens 2 Tage im Voraus erstellt.
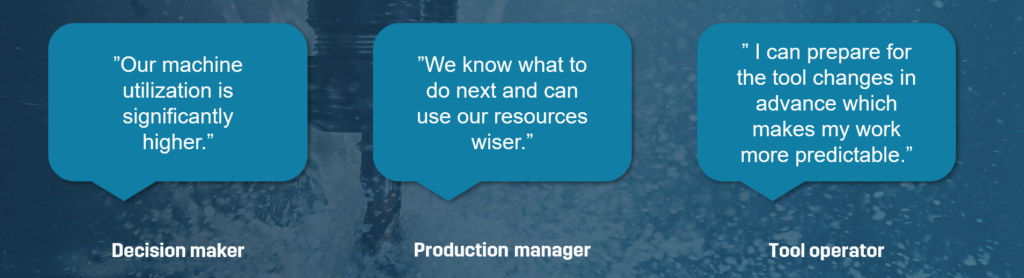
Schritt 2: Voreinstellgeräte nutzen und Werkzeugdaten automatisieren
Die Konsequenz von falschen Werkzeugkorrekturen sind entweder eine schwankende Qualität oder im schlimmsten Fall ein Maschinenausfall. Beides ist eine totale Verschwendung von Zeit und Geld und bringt den gesamten Fertigungsplan durcheinander, da die Teile nachbearbeitet werden müssen und die Zeit für die anderen geplanten Arbeiten fehlt. Im vorherigen Schritt haben wir 96.000 Werkzeugrüstungen pro Jahr berechnet – selbst das sorgfältigste Team kann diese Menge an Daten nicht fehlerfrei messen und eingeben. Wenn Ihre Fehlermarge 1% beträgt und 1% dieser Fehler zu einem Spindelabsturz führen würden, müssten Sie 960 Teile nacharbeiten und einen Spindelabsturz pro Jahr reparieren.
Unsere Empfehlung für jede Fertigung lautet: Nutzen Sie zuerst das Werkzeug-Voreinstellgerät. Ein Werkzeugvoreinstellgerät ermöglicht es Ihnen, Voreinstellungen bereits während der Bearbeitung des vorherigen Auftrags vorzunehmen, und Ihre Daten sind jedes Mal zu 100 % korrekt – was viel Zeit und Mühe beim Messen, bei Testläufen und bei der Nacharbeit spart.
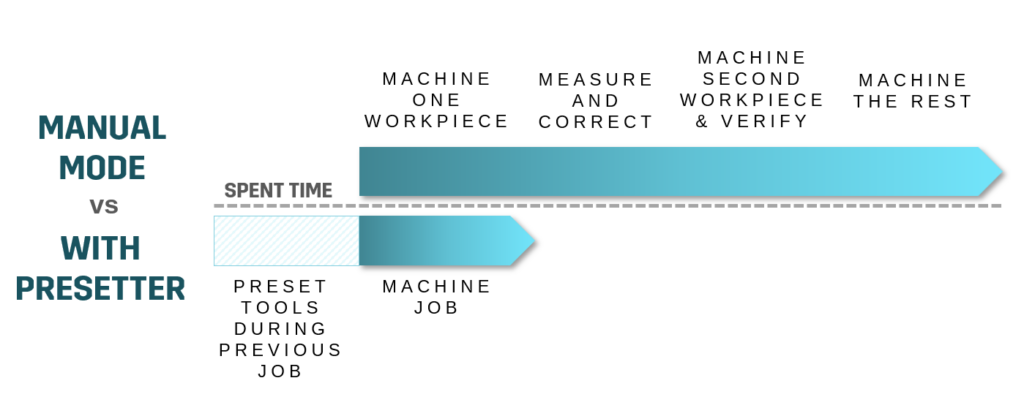
Neben einem Werkzeug-Voreinstellgerät, welches Ihnen perfekte Daten zu den Abmessungen Ihrer Werkzeugen liefert, empfehlen wir, automatisierte Werkzeugdatentransfers zwischen den Maschinen. So haben Sie immer absolut korrekte Werkzeugdaten in Ihrer Werkzeugbibliothek und müssen den Werkzeugverschleiß nicht manuell überwachen, um Werkzeugwechsel zu planen. Für diesen Schritt benötigen Sie:
- Schritt 1 abgeschlossen.
- Ein Werkzeug-Voreinstellgerät.
- Eine Software, die mit Ihrem Werkzeug-Voreinstellgerät, Ihrer Werkzeugbibliothek und Ihren Maschinenwerkzeugen kommuniziert, um die korrekten Werkzeugdaten hin und her zu übertragen.
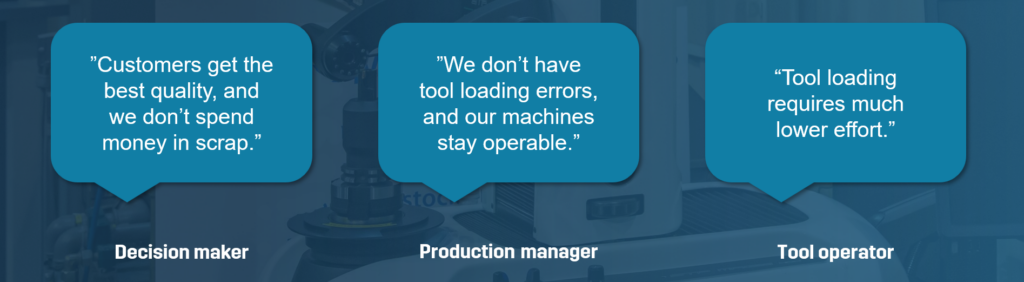
Schritt 3: Werkzeuge mit Maschinen teilen und automatisierte Werkzeug-Transfers
Wenn Ihr Werkzeugbedarf hoch ist oder die Werkzeugstandzeiten aufgrund herausfordernder Materialien kurz sind, müssen Ihre Bediener ständig hin- und herlaufen, um abgenutzte Werkzeuge zur Überarbeitung zu bringen und Werkzeuge für die nächsten Aufträge vorzubereiten. Selbst eine kleine Unterbrechung dieses Services bedeutet, dass die Maschinen stoppen und auf Werkzeuge warten müssen, wodurch die gesamte Fertigungskapazität nicht genutzt werden kann. Außerdem, wenn jede Ihrer Maschinen ihr eigenes Werkzeugsatz hat, investieren Sie wahrscheinlich stark in Ersatzwerkzeuge.
In einem solchen Operationen sollten Sie nicht nur die Automatisierung Ihrer Werkzeugmaschinen, sondern auch Ihrer Schneidwerkzeuge in Betracht ziehen. Die Werkzeug-Automatisierung kann tausende von Schneidwerkzeugen zentral speichern und diese Werkzeuge zwischen Ihren Bearbeitungszentren teilen. Jedes Werkzeug wird automatisch in ein Bearbeitungszentrum transferiert, kurz bevor es entsprechend des Produktionsplanes benötigt wird, und in den Werkzeugraum gebracht, wenn es überarbeitet werden muss. Auf diese Weise wird jedes Werkzeug maximal genutzt, unabhängig davon, in welchem Bearbeitungszentrum es benötigt wird, und die Investition in Werkzeugmagazine und Ersatzwerkzeuge ist geringer. Die Maschinen laufen ohne werkzeugbedingte Unterbrechungen – auch während der lights-out Stunden. Um die Werkzeugautomatisierung zu ermöglichen, benötigen Sie:
- Schritt 1 und 2 sind abgeschlossen.
- Ein Werkzeugautomatisierungssystem, das sich in Ihren Fertigungsplan integriert und über ausreichend Werkzeugplätze und Transferkapazität für Ihre Bedürfnisse verfügt.
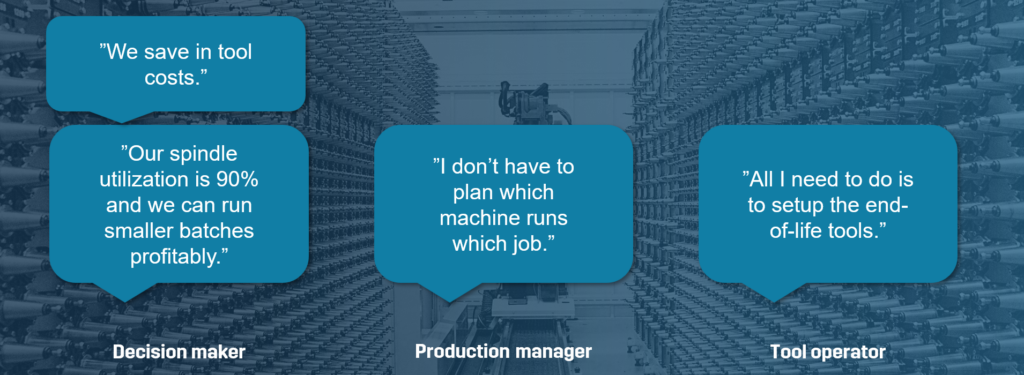
Hier ist ein YouTube-Video, das zeigt, wie Werkzeugautomatisierung in der Praxis funktioniert.
Schritt 4: Automatisierung der Werkzeug-Setups
Wenn die Standzeit Ihrer Werkzeuge extrem kurz ist und Sie ständig erneuerte Werkzeuge benötigen, benötigen Sie im Grunde ständig Personal, das nur für den Werkzeugwechsel zuständig ist. Selbst mit einem Werkzeugautomatisierungssystem, wie in Schritt 3 beschrieben, könnten Sie Ihre Produktion in diesem Szenario nicht ohne Aufsicht betreiben. Außerdem kann die Überarbeitung von Werkzeugen, insbesondere bei großen und scharfen Werkzeugen, eine anstrengende und riskante Arbeit sein.
Diese Situation tritt typischerweise beim Bearbeiten anspruchsvoller Materialien und Teile auf, zum Beispiel bei einigen Komponenten aus der Luft- und Raumfahrt. Wir empfehlen, auch die Werkzeug-Setups soweit wie möglich zu automatisieren. Eine Werkzeugvorbereitungszelle kann Werkzeuge waschen, vakuumtrocknen, voreinstellen und Werkzeuge zur Wechselstation liefern, die mehrere Werkzeuge in rotierenden Haltern ergonomisch bereitstellt. Da die Überarbeitung der Werkzeuge teilweise automatisch erfolgt und der manuelle Teil in Chargen abgewickelt werden kann, ist der Werkzeugfluss für längere unbemannte Betriebszeiten gewährleistet. Für automatisierte Werkzeugvorbereitungen benötigen Sie:
- Die Schritte 1 – 3 sind abgeschlossen und
- Ein Werkzeugvoreinstellgerät, das in Ihr Werkzeugautomatisierungssystem integriert ist.
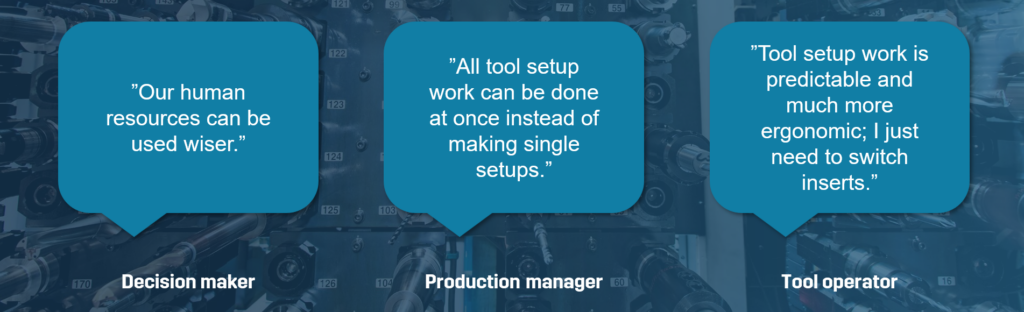
Besuchen Sie uns auf der AMB und erfahren Sie mehr über die Best Practices des Werkzeug-Managements und -Automatisierung!
Sie planen die AMB im September in Stuttgart zu besuchen?
Dann verpassen Sie auf keinen Fall unseren „How-To-Automate Tuesday“ am 10. September!
Natürlich können Sie sich auch eine persönliche Demo mit einem unserer Experten buchen, um mehr über flexible Automatisierung zu erfahren und LIVE zu erleben, wie diese der Praxis funktioniert!
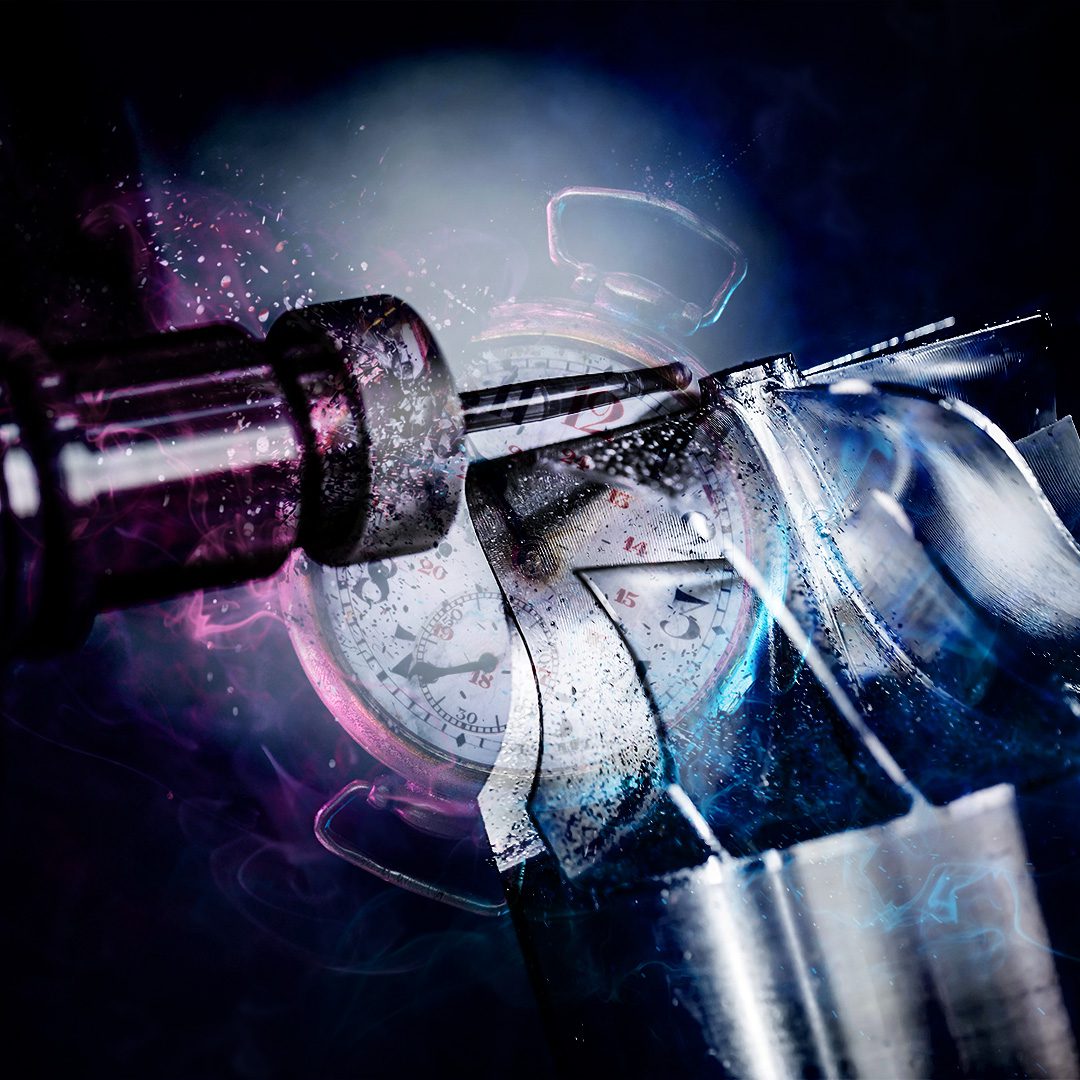
12 SEPTEMBER 2024
AMB: Tool Management Thursday
Auf der AMB beraten und zeigen wir Ihnen gerne, wie Schneidwerkzeuge optimal verwaltet werden können und Werkzeugautomatisierung mit Werkzeugmagazinen und Drehmaschinentürmen funktioniert.
Nehmen Sie an dieser Info Session teil oder buchen Sie Ihre eigene Demo!