Kleine Serien und hohe Teilevarianz –
Flexibles Fertigungssystem (FFS) sorgt für stabilen und verlässlichen Prozess
„Es ist Teil unserer DNA, unseren Namen zu leben“, sagt Scott Shortess, CEO von Advanced Machining & Fabricating und Advanced Plastics in Owasso, Oklahoma. Bekannt ist das Unternehmen jedoch schlicht als „Advanced“.
Die Geschichte von Advanced beginnt 1979, als Shortess’ Vater, Steve Shortess, das Unternehmen als Komponentenhersteller für die Öl- und Gasindustrie in seiner Garage gründete – mit einem einzigen LKW und einem Inventar im Wert von gerade einmal 5.000 Dollar. Der Name „Advanced“ wurde aus einem cleveren Grund gewählt: Er sollte in den „Gelben Seiten“ des Telefonbuchs vor der Konkurrenz erscheinen.
Was als einfacher Marketingtrick begann, entwickelte sich im Laufe von 40 Jahren zu einem Synonym für Fortschritt. „Advanced“ steht heute für Innovation, Exzellenz und eine klare Philosophie, die tief in der DNA des Unternehmens verankert ist – ein Name, der nicht nur Programm, sondern Antrieb für den Erfolg geworden ist.
Advanced hat sich vom kleinen Rohstofflieferanten zu einem Tier-1-Supply-Chain-Partner für führende Erstausrüster in den Bereichen Luft- und Raumfahrt, Verteidigung, Energie sowie Öl und Gas entwickelt. „Mein Vater hatte eine Leidenschaft für neue Technologien“, erinnert sich Shortess. „Er war immer der Erste, der ein Autotelefon, einen Radardetektor oder einen tragbaren Computer hatte. Es schien, als wäre er ständig auf der Suche nach dem Neuesten und Besten.“
Ursprünglich veröffentlicht auf SME.org und geschrieben von Advanced Machining & Fabricating
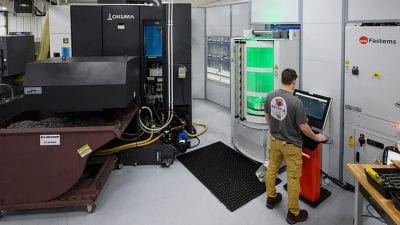
Advanced setzt ROBOFMSone von Fastems ein. Die größten Vorteile des neuen Systems ergeben sich am vorderen Ende des Prozesse durch die Funktionen der MMS Steuerung für die Terminierung, Progonose, Datenerfassung und Dokumentensteuerung.
Das Streben nach Fortschritt, gepaart mit dem Aufschwung in der Luft- und Raumfahrt sowie der Öl- und Gasindustrie, verwandelte Advanced in ein Kraftzentrum des Südwestens. Die Kunden verlangten zunehmend komplexere Bauteile, was den einst kleinen Garagenbetrieb dazu brachte, in hochmoderne Maschinen zu investieren. Um die wachsende Nachfrage zu bewältigen, stellte Shortess zusätzliches Personal ein. Heute beschäftigt Advanced 35 Mitarbeiter – selbst nach einer Umstrukturierung während der Coronavirus-Pandemie, die eine leichte Reduzierung der Belegschaft erforderlich machte.
Der ganze Stolz von Advanced ist derzeit der Bereich der 5-Achsen-Bearbeitung. Das Herzstück bildet ein flexibles Fertigungssystem (FFS) von Fastems mit 36 Paletten, das an zwei Okuma MU 5000 Maschinen angebunden ist. Ergänzt wird dieser Bereich durch drei eigenständige Okuma M460-5AX-Maschinen. Die gesamte Abteilung ist auf die fünfachsige Bearbeitung von Hartmetall spezialisiert, vor allem für die Luft- und Raumfahrtindustrie. Hier wird an den meisten Tagen Titan in Luft- und Raumfahrtqualität wie 6AL4V bearbeitet, um hochpräzise Teile wie Gondel- und Schubumkehrkomponenten herzustellen.
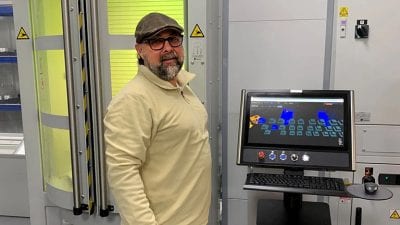
Scott Shortess, CEO von Advanced Machining & Fabricating and Advanced Plastics.
Shortess legt großen Wert auf Effizienz und teilt die technologische Neugier seines Vaters. Daher entschied er sich, zunehmend auf Automatisierung zu setzen. Vor etwa zehn Jahren begann er mit seinem Team, die Spindelauslastung systematisch zu messen. „Anfangs nutzten wir eine sehr rudimentäre Methode“, erinnert er sich. „Jemand machte mit dem Smartphone ein Foto der Messwerte auf den Maschinen und ging dann an den Schreibtisch, um aus den Daten Zeit- und Produktivitätsdiagramme zu erstellen.“
Das Werkstatt-Team analysierte akribisch, wie lange jede Maschine lief und wie oft sie stillstand. „Erst durch diese Zahlen wurde uns klar, wie niedrig unsere Spindelauslastung tatsächlich war“, erklärt Shortess. Dieser Erkenntnis folgend nahm er Kontakt zu Risto Niemi, Business Area Director bei Fastems, auf – einem führenden Entwickler und Anbieter von Automatisierungslösungen.
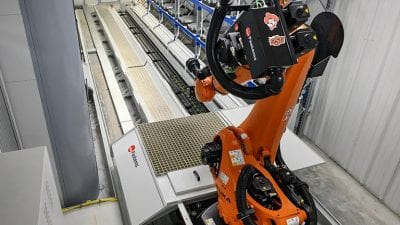
Advanced’s 36 pallet system is connected to two Okuma MU 5000s and run by Fastems ROBO-One Flexible Manufacturing System (FMS).
Niemi besuchte also Advanced, um Lösungen für die Manufacturing Management Software (MMS), Automationssysteme, Lifecycle Services und digitale Fertigung vorzustellen. “Er hat uns wirklich alle Möglichkeiten der Automatisierung aufgezeigt“, erzählt Shortess. “Wir haben Zehntausende von Dollar für Reisen, Messen und neue Technologien ausgegeben, aber bis zu diesem Treffen und der kontinuierlichen Unterstützung und dem Wissen, das er und das Fastems Team bieten, haben wir nie einen so entscheidenden Schritt nach vorne getan.”
Advanced ließ das RoboFMS ONE (FMS – Flexible Manufacturing System) von Fastems im Juni 2019 installieren. Das RoboFMS ONE, welches mit der MMS für die Produktionsplanung und -ausführung ausgestattet ist, automatisiert die fünfachsigen Okuma-Maschinen und hat dadurch die Rüstzeit verkürzt. Shortess erzählt, dass das RoboFMS ONE und die MMS “enorme Auswirkungen auf die Effizienz, wie die Ausbringung beim ersten Durchlauf, die Spindelauslastung und die erhöhte Kapazität und gleichzeitig den Ruf des Unternehmens für die Herstellung von Qualitätsprodukten und Service verbessert haben.”
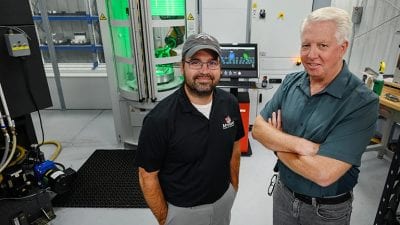
Jason Adkins, Director Operations & Kim Parrish, President bei Advanced.
„Wir fertigen nach Bedarf und nicht für den Lagerbestand. Wir können die Daten aus dem ERP-System hochladen und alles, unter Berücksichtigung der benötigten Ressourcen, einplanen lassen.”
Shortess betont, dass die vorausschauende MMS und das Palettenautomationssystem die effizienteste Lösung für Unternehmen wie Advanced darstellen, wenn es um die Fertigung einer hohen Teilevarianz in kleinen Losgrößen geht. Die typischen Kunden von Advanced bestellen meist ein bis fünf Teile pro Auftrag, nicht Tausende. „Die Flexibilität des Systems ist für uns ein entscheidender Vorteil, da wir als Auftragsfertiger nach Bedarf produzieren und nicht für den Lagerbestand. Wir können die Daten direkt aus dem ERP-System hochladen und die gesamte Produktion unter Berücksichtigung der benötigten Ressourcen automatisch planen lassen“, erklärt Shortess.
In einem Betrieb mit häufigen Umrüstungen ist die Reduzierung der Rüstzeit der einfachste Weg, um Zeit und Geld zu sparen. Shortess erinnert sich an ein komplexes Scharnierbauteil aus Titan für die Luft- und Raumfahrt, das früher auf konventionellen Einzelmaschinen bearbeitet wurde. Allein die Rüstzeit für dieses Bauteil betrug zwei Stunden und war damit zeitintensiver als die eigentliche Bearbeitungszeit von einer Stunde und vierzig Minuten.
„Mit unserem neuen System haben wir das Bauteil quasi in die Produktentwicklung zurückgeführt. Die Rüstzeit hat sich von zwei Stunden auf praktisch null reduziert, da sich das Teil immer im Fastems-System befindet“, erklärt Shortess. „Diese eingesparte Rüstzeit hilft uns, die Spindelauslastung deutlich zu steigern.“
Derzeit arbeitet Advanced in einem teilweise bemannten Betrieb, verfolgt jedoch das ultimative Ziel einer komplett mannlosen Fertigung.
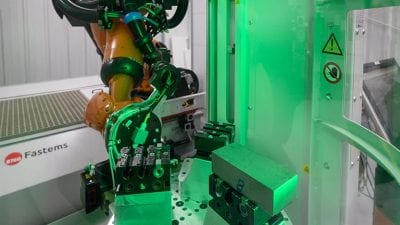
Advanced reduzierte die Umrüstzeit, die erforderlich war, um mit der Bearbeitung einer Titan-Halterung für die Luft- und Raumfahrtindustrie zu beginnen, durch standardisierte Spannmittel und konnte sofort eine Steigerung der Spindelauslastung feststellen, nachdem es sich der Fastems-Automatisierung anvertraut hatte.
„Wir können die Datenmenge, die die MMS verarbeitet, einfach nicht manuell bewältigen. Das System analysiert Werkzeugdaten, Zykluszeiten – einfach alles – und sagt genau voraus, was benötigt wird. Heute sprechen wir über stabile, vorhersagbare Prozesse. Wer in der Fertigung nicht in solche Technologien investiert, läuft meiner Meinung nach Gefahr, den Anschluss zu verlieren.“
„Das neue System unterstützt uns bereits am Anfang des Prozesses, noch bevor ein Auftrag gestartet wird. Advanced nutzt diese Möglichkeiten, um den Werkzeugverschleiß zu überwachen und alle verfügbaren Daten effizient zu nutzen“, erklärt Shortess. „Wir lassen das System im Automatikmodus laufen – genau so, wie es vorgesehen ist. Es macht, wofür wir es gekauft haben.“
Er fährt fort: „Die Datenmenge, die die MMS verarbeiten kann, könnten wir niemals manuell bewältigen. Das System analysiert Werkzeugdaten, Zykluszeiten – einfach alles – und trifft genaue Vorhersagen darüber, was benötigt wird. Heute sprechen wir über stabile, vorhersagbare Prozesse. Wer in der Fertigung nicht in solche Technologien investiert, wird meiner Meinung nach zunehmend ins Hintertreffen geraten.“
Advanced plant in den kommenden Jahren eine weitere hochmoderne Anlage, die neue Maßstäbe setzen soll. Geplant ist ein zusätzliches flexibles Fertigungssystem von Fastems, ergänzt durch Technologien wie das Fastems Gantry Tool Storage (GTS), robotergestütztes Entgraten und fortschrittliche Messtechnik. Das GTS kann bis zu 4.000 Werkzeuge zentral lagern und nutzt einen Roboter auf einer Portalachse, der die Werkzeuge effizient zu den Maschinen transportiert – eine erhebliche Entlastung für die Bediener und ein großer Schritt in Richtung Effizienz.
„Ohne ein GTS ist es meiner Meinung nach kaum möglich, eine Spindelauslastung auf Weltklasseniveau zu erreichen. Und genau das ist der Kern der Sache. Die Kombination aus einem flexiblen Fertigungssystem (FFS) und einem GTS eröffnet völlig neue Möglichkeiten in der Teileproduktion“, erklärt Shortess. „Mit unserer neuen Automatisierungstechnologie und der klaren Vision für Advanced machen wir unserem Namen alle Ehre.“
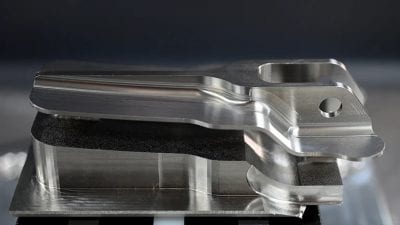
Bevor das flexible Fertigungssystem bei Advanced installiert wurde, benötigte das Einrichten der Spannvorrichtung allein für die Maschine und der Spannmittel zwei Stunden. Heute hat sich diese Zeit auf fast Null reduziert.
Ursprünglich veröffentlicht auf SME.org und geschrieben von Advanced Machining & Fabricating
Fortschrittliche Fertigung neu definiert – Advanced Machining & Fabricating
- Von der Rohmateriallieferung zum Tier-1-Partner
Advanced Machining & Fabricating hat sich von einem kleinen Rohmateriallieferanten zu einem Tier-1-Supply-Chain-Partner für führende OEMs in den Bereichen Luft- und Raumfahrt, Verteidigung, Energie sowie Öl und Gas entwickelt. - Die Herausforderung
Mit der steigenden Nachfrage nach komplexeren Komponenten statt einfacher Bauteile stand Advanced vor der Aufgabe, seine Kapazitäten auszubauen und in hochspezialisierte Maschinen zu investieren. Um den Anforderungen seiner Kunden gerecht zu werden, stellte das Unternehmen zusätzlich qualifizierte Mitarbeiter ein. - Die Lösung
Das Herzstück von Advanced ist heute die Fünf-Achsen-Bearbeitungsabteilung. Ihr Highlight: Ein flexibles Fertigungssystem RoboFMS ONE von Fastems, das 36 Paletten mit zwei Okuma MU 5000 Maschinen verbindet. Das System, ausgestattet mit der leistungsstarken MMS für Produktionsplanung und -steuerung, hat die Rüstzeiten signifikant reduziert und ermöglicht eine nahtlose Automatisierung der fünfachsigen Bearbeitung. - Das Ergebnis
Die Automatisierung führte zu beeindruckenden Effizienzsteigerungen: Höhere Ausbringung beim ersten Durchgang, maximale Spindelauslastung und eine deutliche Erhöhung der Produktionskapazität. Gleichzeitig konnte Advanced seinen Ruf für Qualitätsprodukte und exzellenten Service weiter ausbauen. - Zukunftsvision
Advanced plant in den kommenden Jahren den Aufbau einer weiteren hochmodernen Produktionsanlage. Diese wird mit einem weiteren flexiblen Fertigungssystem von Fastems ausgestattet sein, das zusätzliche Prozesse wie Gantry Tool Storage (GTS), robotergestütztes Entgraten und fortschrittliche Messtechnik integriert. Ein klarer Schritt in Richtung einer noch effizienteren und zukunftssicheren Fertigung.