Höhere Fertigungsflexibilität –
auch bei Marktschwankungen – Dank agiler Automation und mannlosen Umrüsten
„Das wird nicht funktionieren.“ So oder so ähnlich lauteten die Antworten, als Herbert Mayr nach einer Automationslösung suchte, die nicht nur das Paletten- und Werkstückhandling in einem System kombiniert, sondern auch das mannlose Umrüsten einer Maschine.
Herbert Mayr ist Betriebsleiter und Prokurist der ALLMATIC-Jakob Spannsysteme GmbH (siehe Kasten). „Wir entwickeln und fertigen Maschinenschraubstöcke, vom Hochdruckspanner für konventionelle Fräsmaschinen bis hin zu komplexen Lösungen für flexible Fertigungszentren. Hinzu kommen Sonderlösungen für spezielle Anforderungen.“
Der Fokus richtet sich auf Serienfertigung mit einem Anteil von rund 85 Prozent an der Gesamtproduktion und Losgrößen zwischen 5 und 300 Stück pro Auftrag. Zirka 15 Prozent entfallen demnach auf Sonderanfertigungen für verschiedene Kunden.
„Wir gehören zu den führenden Anbietern von Maschinenschraubstöcken. Dennoch haben wir nicht den Anspruch, die meisten Schraubstöcke zu verkaufen, um hierdurch Marktführer zu werden. Wir streben vielmehr bis 2030 die Technologieführerschaft in unserem Segment an“, so der Betriebsleiter.
Intensiver mit Automation befassen
Ehrgeizige Ziele verpflichten, weiß auch Luis Paiba, Leiter Entwicklung und Konstruktion: „Im Sinne unserer Kunden müssen wir weiterhin Innovationen entwickeln, noch mehr Intelligenz in unsere Lösungen bringen und uns vor allem intensiver mit Automatisierung befassen.“
Aus Sicht von Herbert Mayr ein Thema mit Relevanz nicht allein für die eigenen Produkte, sondern außerdem für die gesamte Fertigungsorganisation und damit die Beschäftigen des Unternehmens: „Wir haben viele junge, qualifizierte Mitarbeiter, die kaum bereit sind, im Mehrschicht-Betrieb zu arbeiten. Um solche Fachkräfte auf Dauer halten zu können, müssen wir attraktive Arbeitsplätze schaffen, was letztendlich ein Einschicht-Betrieb mit Mitarbeitern und eine mannlose Produktion in der übrigen Zeit durch konsequenten Einsatz von Automationslösungen bedeutet.“
Projekt beinahe an besonderer Anforderung gescheitert
Das in diesem Zusammenhang bis dato wohl ambitionierteste Projekt von ALLMATIC: Die Planung und Realisierung einer Roboterzelle, die quasi rund um die Uhr bis zu 32 verschiedene Bauteile in Einzellose von über 100 Stück pro Auftrag für Schraubstöcke mannlos und damit hochautomatisiert fertigt.
Anfänglich sah es jedoch danach aus, als ob dieses Automationsprojekt scheitern würde. Herbert Mayr erinnert sich: „Die Lösung sollte zusätzlich zur flexiblen Werkstückhandhabung bei einem Produktwechsel in mannlosen Schichten auch ein automatisches Umrüsten der Maschine ermöglichen.“ Eine Anforderung, für die der Betriebsleiter von vielen Maschinenherstellern nur Kopfschütteln erntete. „Bis ich während einer Hausausstellung bei der Gebr. Heller Maschinenfabrik Thomas Weinhold, Senior Sales Manager von Fastems, kennenlernte und schon allein anhand seiner spezifischen Fragen sofort erkannte, dass hier jemand ist, der tatsächlich versteht, was ich vorhatte. Um es kurz zu machen: Mit Fastems und Heller als Maschinenlieferant sowie Generalunternehmen für das Projekt haben wir unsere Roboterzelle schließlich in die Tat umsetzen können.“
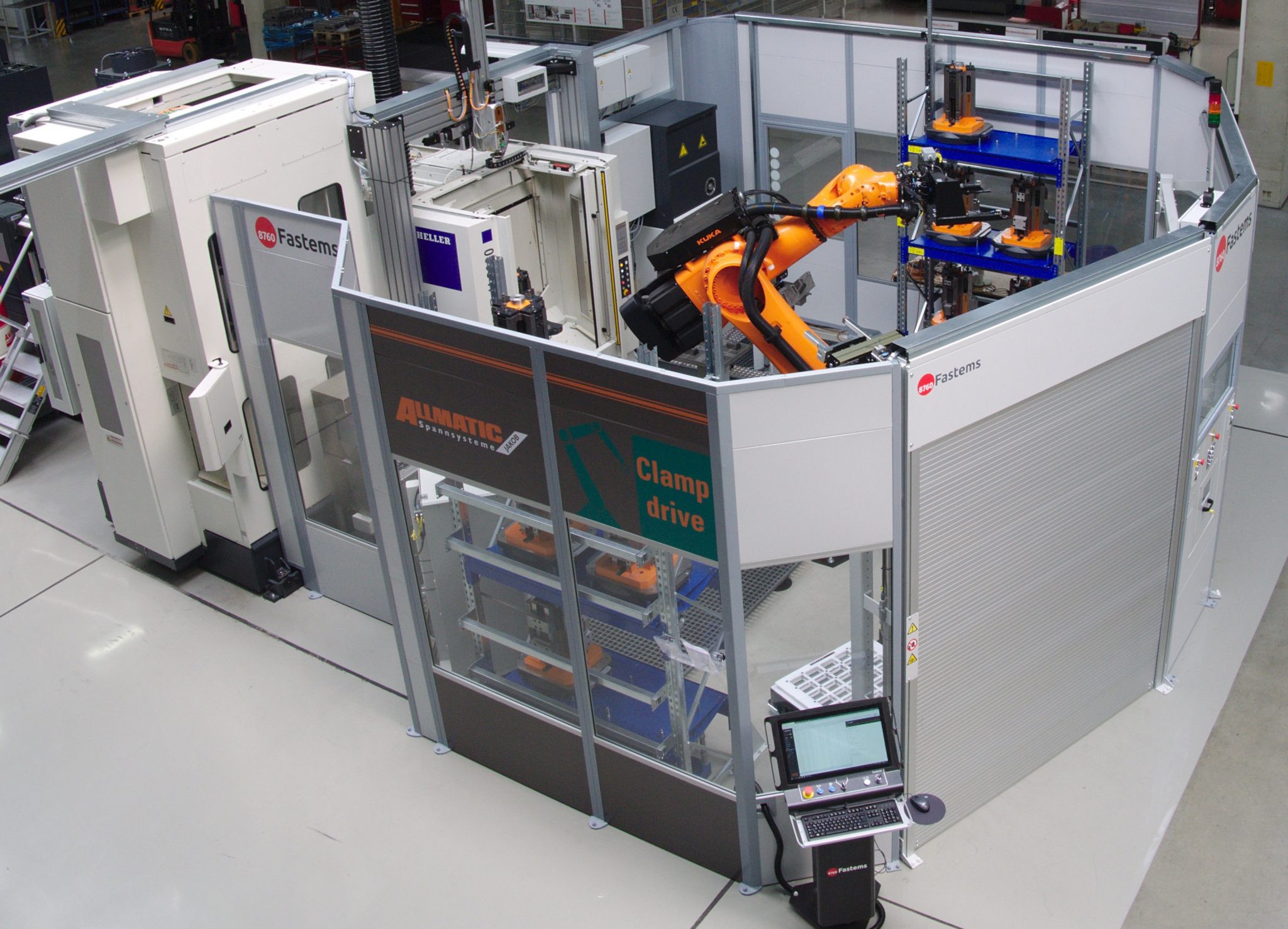
Die seit 2018 in Betrieb befindliche Roboterzelle bei ALLMATIC ist bis dato einzigartig und verfügt über einige Besonderheiten.
Produktionsstart via Barcode
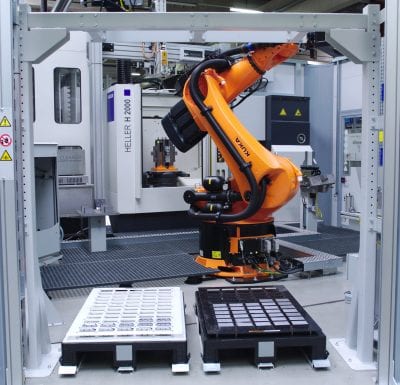
Eine von zwei Materialstationen für jeweils zwei Eurokunststoffpaletten für Roh- und Fertigteile.
Die einzelnen Bestandteile der Roboterzelle (siehe unten: Agile Roboterzelle) und vor allem die Beschreibung eines typischen Produktionsablaufs, vermitteln einen Eindruck von den Besonderheiten dieser Automationslösung.
Hierzu Luis Paiba: „An den beiden Materialstationen stehen jeweils zwei Paletten mit Rohmaterialien sowie für die Fertigteile bereit, sodass bis zu zwei unterschiedliche Aufträge inklusive automatischer Maschinenumrüstung unbemannt abgearbeitet werden können.“
Zu Beginn eines Auftrags scannt der Roboter zunächst den Barcode an der Rohmaterialmatrize und erhält somit sämtliche Informationen für die anstehende Produktion.
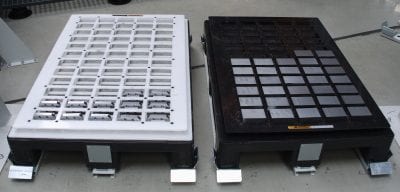
Die von ALLMATIC selbst angefertigten Matrizen für die Rohmaterial- und Fertigteil-Paletten sind für eine optimale Roboter-Handhabung konzipiert.
Die Manufacturing Management Software (MMS) von Fastems ruft hierzu automatisch die entsprechenden Programme für die Automatisierung sowie Werkstückbearbeitung ab. Der Roboter entnimmt mit dem Permanentmagnetgreifer einen Rohling aus der Matrize, legt ihn zur genauen Positionierung in eine Schablone, transportiert ihn anschließend zur Umgreifstation und belädt dann mit dem Parallelgreifer die Maschinenpalette.
Komplettbearbeitung in zwei Aufspannungen
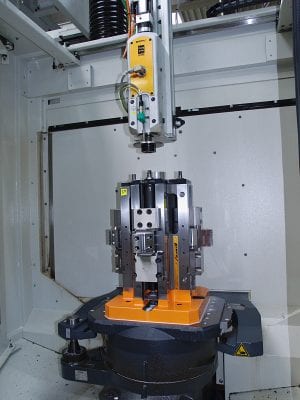
Der ALLMATIC Clamp Drive (oben) ermöglicht eine mannlose Werkstückaufspannung.
Für eine aktuelle Fertigung stehen immer zwei Vorrichtungen auf der Maschine bereit, um eine durchgängige Fertigung und 6-Seiten-Bearbeitung mit nur zwei Aufspannungen in zwei Prozessschritten (OP10 und OP20) realisieren zu können. Die gleichsam automatische wie flexible Spannung der Werkstücke übernimmt der ALLMATIC Clamp Drive, der über der Rüstseite des Palettenwechslers der Maschine positioniert ist.
Ein Produktionsauftrag beginnt stets mit einer leeren Palette, wobei zunächst Werkstücke auf die erste Vorrichtung (OP10) aufgespannt werden, während OP20 für eine Bearbeitungsphase leer bleibt. Nach der Bearbeitung werden die Halbzeuge vor der Maschine zwischengelagert und anschließend auf die zweite Vorrichtung (OP20) aufgespannt. Nach dem Palettentransfer kann der Roboter die erste Vorrichtung (OP10) erneut mit Rohlingen bestücken. Danach wird der Gesamtauftrag mit einem ständigen Wechsel der Prozessschritte OP10 und OP20 abgearbeitet. Steht ein Produktwechsel an, transportiert der Roboter den für die anstehende Produktion benötigen Spannturm zur Maschine, noch während sich die letzten Teile des vorherigen Auftrags in der Maschine befinden.
Nachdem ein kompletter Fertigungsauftrag abgearbeitet ist, wechselt der Roboter bei Bedarf außerdem automatisch die für den neuen Auftrag (neue Werkstücke) erforderlichen Paletten mit Vorrichtungen in die Maschine.
Potenziale für Prozessoptimierungen
„Mit einer komplexen Automationslösung wie dieser, müssen in der Praxis immer auch Erfahrungen gesammelt werden, um mitunter Optimierungspotenziale für einzelne Prozesse zu gewinnen“, betont Herbert Mayr.
Momentan entnimmt der Roboter alle Halbfertigteile und legt sie auf der Umgreifstation ab, um die zweite Vorrichtung mit diesen Teilen zu bestücken. Zur Entnahme aller Teile muss die Palette gedreht werden. Eine anschließende prozesssichere Aufspannung erfordert jedoch eine erneute Referenzierung des Clamp Drive, was wertvolle Zeit kostet. „Das wollen wir nun ändern, in dem der Roboter zunächst ein Halbzeug entnimmt und anschließend sofort die Palette ohne Drehung mit einem Rohling an der gleichen Spannposition bestückt“, so Mayr.
Parametrische Programmierung minimiert Nebenzeiten
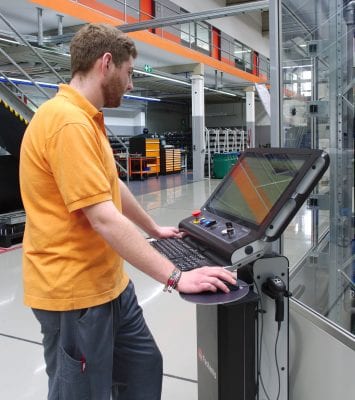
Der für das System verantwortliche Mitarbeiter von ALLMATIC am Terminal für die MMS von Fastems, die u.a. die gesamte Planung, Steuerung und Überwachung der automatisierten Fertigung übernimmt und hierzu nicht nur die NC-Programme, sondern auch die insgesamt 160 Werkzeuge verwaltet sowie deren Standzeiten überwacht.
Da die agile Fertigungszelle bei ALLMATIC für eine unbemannte Produktion über lange Perioden ausgelegt ist, sollte auch die Einführung von Neuteilen und die damit verbundene Anpassung der Roboterkinematik mit möglichst wenig Zeitaufwand verbunden sein.
Eine entscheidende Unterstützung bietet hier die parametrische Roboter-Programmierung über die MMS.
Spezielle Roboterkenntnisse sind hierfür nicht notwendig, wie Luis Paiba erläutert: „Fastems hat uns im Vorfeld bereits einige Programme zur Fertigung von Bauteilen zur Verfügung gestellt.
Ist ein Neuteil zu produzieren, lassen sich die hierzu notwendigen Bewegungsabläufe durch Eingabe spezifischer Parameter (Handhabungsschritte) einfach anpassen, ohne zeitaufwendiges Einteachen des Roboters.
Auf diese Weise hat unser Mitarbeiter am System bereits 17 neue Bewegungsmuster für den Roboter angelegt.“
Luis Paiba, Leiter Entwicklung und Konstruktion von ALLMATIC:
„Wenn wir Technologieführer werden wollen, müssen wir uns auch intensiver mit Automatisierung beschäftigen, nicht nur im Hinblick auf unsere Produkte.“
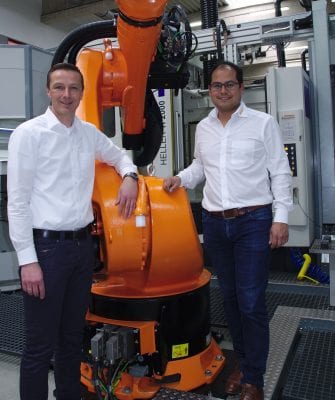
Herbert Mayr (links), Betriebsleiter und Prokurist, und Luis Paiba, Leiter Entwicklung und Konstruktion, haben während des Projektes wertvolle Erkenntnisse gewonnen.
Umdenken und wertvolle Erkenntnisse erlangen
Mit diesem Automationssystem hat ALLMATIC nicht nur ein Plus an Produktivität mithin Flexibilität in der Fertigung gewonnen, sondern nach Überzeugung von Luis Paiba und Herbert Mayr auch wertvolle Erkenntnisse.
„Sämtliche Teile, die wir nun mit der Roboterzelle fertigen, wurden ja schon vorher von uns produziert. Durch die Automatisierung mussten wir umdenken und konnten hierbei neue Potenziale zur Optimierung von Prozessen und Abläufen identifizieren. Einige wenige Beispiele hierfür sind u.a. die Komplettbearbeitung von Bauteilen in zwei anstatt drei Aufspannungen, wobei wir hierzu eigens auch die Werkstücke anpasst haben, oder aber die Einbindung von zuvor manuellen Arbeitsprozessen in die Automation durch die Integration einer Abblas- sowie Konservierungsstation in die Zelle“, erklärt Luis Paiba.
Herbert Mayr, Betriebsleiter und Prokurist von ALLMATIC:
„Viele Maschinenhersteller haben angesichts meiner Idee von einer Lösung mit automatisiertem Umrüsten nur den Kopf geschüttelt. Mit Fastems haben wir diese und auch weitere Herausforderungen gemeistert.“
Nicht nur Gewinn an Kapazität
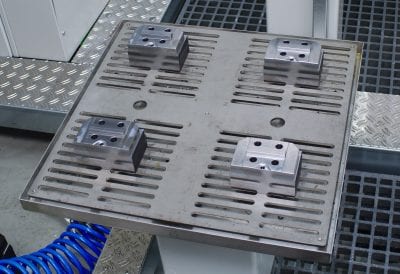
Die Umgreifstation mit bereits bearbeiteten Teilen. 32 verschiedene Bauteile für Maschinenschraubstöcke, z. B. Spannbacken, Grundkörper oder Druck- und Klemmplatten, in Losgrößen über 100 pro Auftrag werden derzeit mit der Roboterzelle produziert.
Und Herbert Mayr hat eine weitere, entscheidende Erkenntnis:
„Automation sichert Arbeitsplätze, weil wir jetzt wesentlich besser auf Auftragsschwankungen reagieren können.
Unsere Roboterzelle ist momentan mit der Fertigung von 32 verschiedenen Bauteilen zu rund 90 Prozent ausgelastet und produziert mannlos in zwei Geisterschichten.
Geht der Auftragseingang einmal dramatisch zurück, muss hierauf nicht zwangsläufig mit einem Arbeitsplatzabbau reagiert werden, da die Roboterzelle dann bspw. auch nur in einer unbemannten Schicht fertigen könnte.“
Agile Roboterzelle: die wesentlichen Merkmale
-
Mit der Heller H 2000 und einem Magazin mit derzeit 160 Werkzeugen (Fassungsvermögen: insgesamt 409 Werkzeuge) wird eine Komplettbearbeitung in zwei Aufspannungen realisiert. Das Bild zeigt eine Maschinenpalette im Arbeitsraum des 4-Achs-BAZ. Eine weitere Palette befindet sich neben der Anlage, sodass ein ständiger Palettenwechsel möglich ist.
2 Materialstationen für jeweils zwei Eurokunststoffpaletten (Roh- und Fertigteile)
- Speicherregale für bis zu 12 Maschinenpaletten mit ALLMATIC-Spannmittel
- ALLMATIC Clamp Drive zum Auf- und Abspannen der Werkstücke
- Heller H 2000 4-Achs-Bearbeitungszentrum für die 6-Seiten-Werkstückbearbeitung
- Kuka-Roboter KR600 (max. 400 kg Handhabungsgewicht)
- Palettengreifer sowie Doppelgreifer von Schunk für Werkstückhandhabung (Permanentmagnetgreifer/Parallelgreifer)
- Konservierungsstation
- Abblasstation
- Umgreifstation/Zwischenablage
- Prüfteill-Schublade
- Barcode-Reader
- Manufacturing Management Software (MMS)
für das automatisierte Produktionsmanagement
Spezialist für Spannsysteme
ALLMATIC wurde 1973 gegründet und hat sich seit 2001 als Mitglied der Jakob-Gruppe zu einem führenden Anbieter von Spannsystemen entwickelt, angefangen von der rein mechanischen Gewindespindel, über NC-Spanner (Schraubstöcke mit Kraftverstärker) und Gripp-Spanner, z. B. für die 5-Achs-Bearbeitung, bis hin zu Mehrfach- sowie Sonderspannlösungen.
Mit derzeit 73 Mitarbeitern, darunter 16 Auszubildende, entwickelt und fertigt das Unternehmen mit Sitz in Unterthingau (Allgäu) innovative Lösungen für den weltweiten Markt. Hauptabsatzmarkt ist Europa, allen voran Deutschland, gefolgt von Österreich, Italien, Frankreich und Rumänien. ALLMATIC-Jakob Spannsysteme erwirtschaftete 2018 einen Umsatz von rund 10,8 Mio. Euro.
Erschienen in der NC Fertigung, Ausgabe 07-08/2019
Related products:
Was können wir für Sie tun?
Rufen Sie uns an oder senden Sie uns einfach eine kurze Nachricht.
„*“ zeigt erforderliche Felder an