Hochautomatisierte Einzelteilfertigung – Industrie 4.0 in der Praxis
Reiden Technik und Fastems realisieren Industrie 4.0-Projekt für Daimler AG: Industrie 4.0 ist schon längst nicht mehr nur reine Theorie. Ein ambitioniertes Projekt bei der Daimler AG in Sindelfingen zeigt, welche Potenziale die Strategie tatsächlich birgt, wenn bereits verfügbare Technologien konsequent genutzt werden.
Das Werk Sindelfingen der Daimler AG produziert vor allem Fahrzeuge der E- und S-Klasse inklusive aller Derivate sowie den Sportwagen AMG GT. Der Standort verfügt über einen eigenen Werkzeugbau, der gemeinsam mit dem Anlagenbau den Betriebsmittelbau mit rund 1.200 Mitarbeitern bildet und die Presswerkzeuge zur Produktion der Pkw-Karosserien von Mercedes Benz herstellt. Der Betriebsmittelbau gehört mit seinem Werkzeug- und Anlagenbau zur sogenannten „Technologiefabrik“.
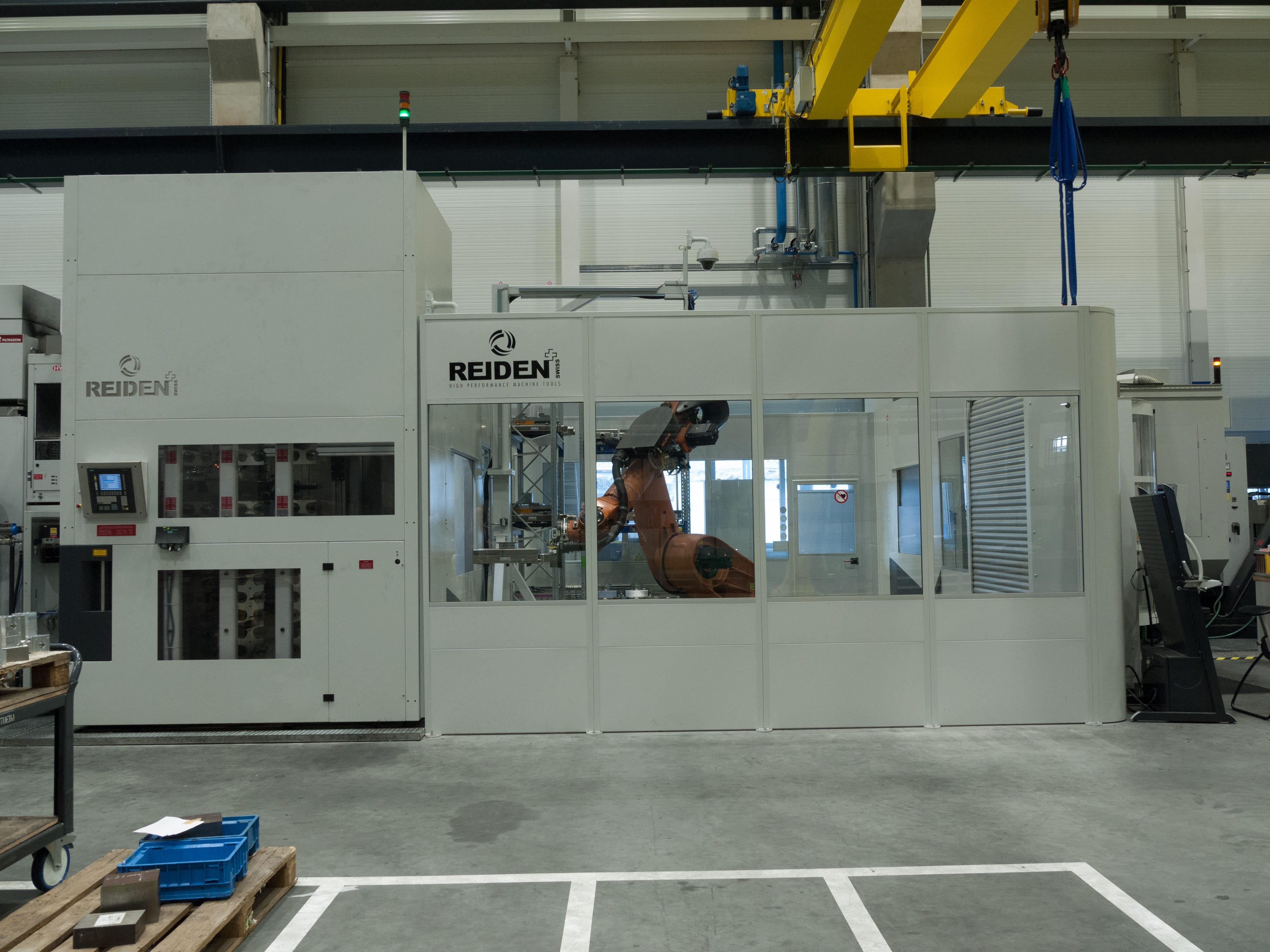
Das multifunktionale Fertigungssystem für Kleinteile ging Mitte 2015 in Betrieb.
Hochautomatisierte Einzelteilfertigung
Im Jahr 2015 wurden die Kapazitäten des Werkzeugbaus erweitert und in diesem Zusammenhang eine neue Halle errichtet, in der eine eigenständige Abteilung des Bereichs entstand. „Bei dieser Gelegenheit haben wir uns gefragt, wie ein zukunftsfähiger Werkzeugbau für die Karosserieproduktion ausschauen könnte. Ein Ergebnis unserer Überlegungen war letztendlich die Entwicklung eines multifunktionalen Fertigungssystems für Kleinteile mit dem wir vollautomatisiert eine Einzelteilfertigung realisieren können“, erklärt Paul Schmidt, Projektkoordinator bei Daimler in Sindelfingen und zuständig für die Maschinen- und Anlagenplanung im Werkzeugbau.
Multifunktionales Produktionssystem
Vor diesem Hintergrund benötigte der Werkzeugbau zwei 5-Achs-Bearbeitungszentren zur Produktion der Formeinsätze für die Großwerkzeuge der Pressen. Das Werkstückhandling, darunter der Transport der Werkstücke zu und von den Maschinen, sollte über ein roboterbasiertes Palettensystem erfolgen. Mehr noch: Im Zusammenhang mit dem Attribut „multifunktional“ musste zusätzlich der Prozess des Induktionshärtens in die Automationslösung integriert werden.
Die zentrale Steuerung der Automationslösung erforderte schließlich ein MES (Manufacturing Execution System), das sich möglichst problemlos in die bestehende Systemumgebung einbinden ließ und u. a. über eine Schnittstelle zum Fertigungsplanungs- und Steuerungssystem des Werkzeugbaus verfügen sollte. „Gemäß unserer Vorgaben haben wir dann ein Lastenheft erstellt und das Projekt im Markt ausgeschrieben, wobei uns nach seinem Abschluss bewusst wurde, dass wir hier ein Industrie 4.0-Projekt auf den Weg gebracht hatten“, so Paul Schmidt.
Als Generalunternehmer für die Realisierung des anspruchsvollen Vorhabens wurde schließlich die Reiden Technik AG beauftragt, die sich für Fastems als kompetenten Partner entschied, um im Zuge des Vorhabens gemeinsam zentrale Elemente der Strategie Industrie 4.0 in die Praxis umzusetzen.
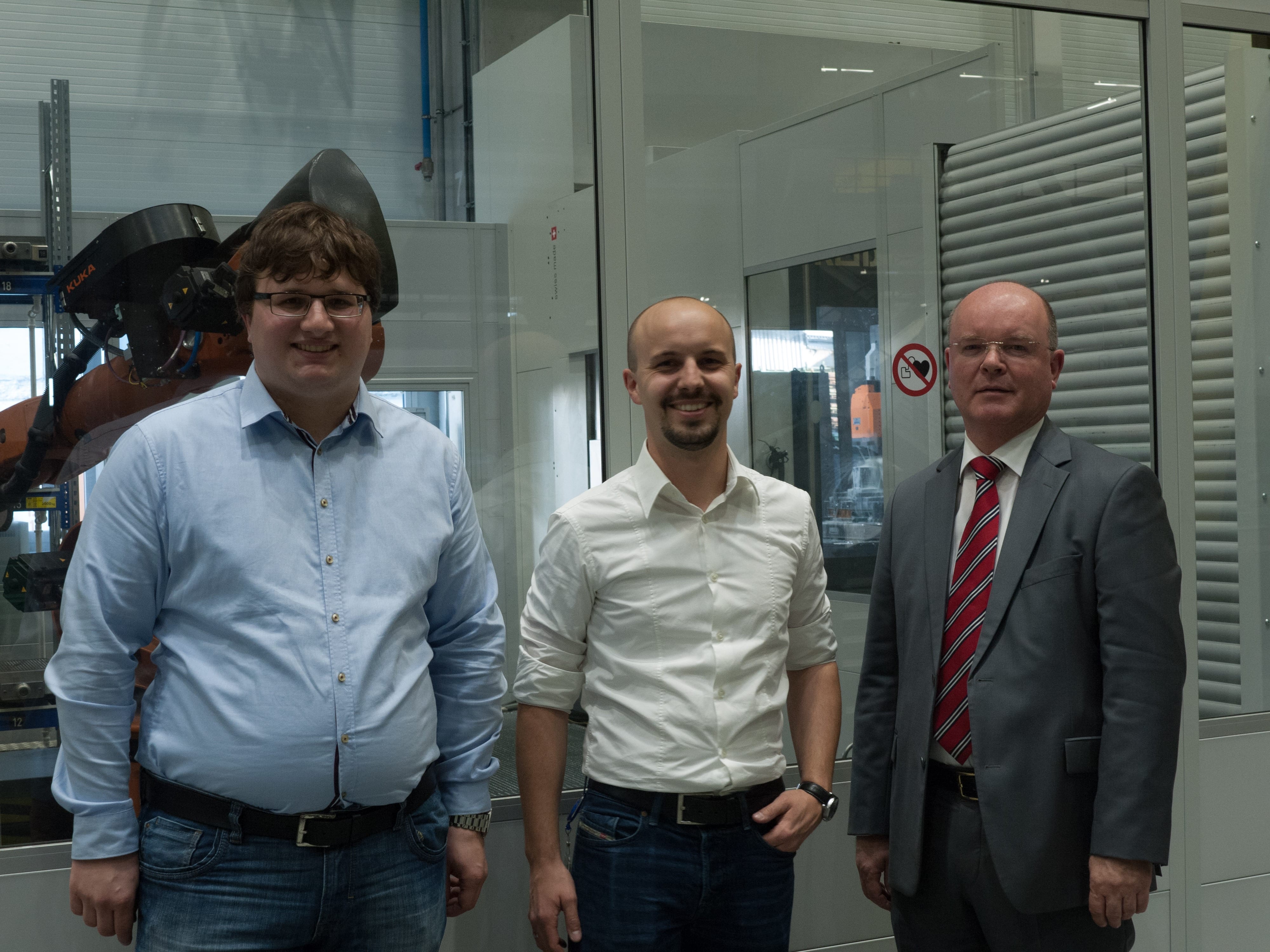
Projektleiter Michael Müller von Reiden Technik, Projektkoordinator Paul Schmidt von Daimler und Rolf Hammerstein, Marketing Direktor von Fastems (v. l.)
Hochkomplexe Vernetzung mit Hilfe von Fastems MMS5
„Keine einfache Aufgabe“, wie Michael Müller, Entwicklungsingenieur von Reiden Technik und Leiter des Projektes, betont. Zu den besonderen Herausforderungen im Projekt gehörten nach seiner Auffassung die kundenspezifischen Modifikationen der 5-Achs-Bearbeitungszentrum vom Typ RX10 für ein roboterbasiertes Be- und Entladen und vor allem die Anpassung der sehr unterschiedlichen Schnittstellen im Fertigungssystem.
Der Projektleiter vermittelt einen Eindruck:
„Die Lösung enthält eine ganze Reihe an Komponenten, die aufgrund einer gewissen internen Intelligenz miteinander kommunizieren können. Das fängt mit dem Fertigungsplanungs- und Steuerungssystem des Werkzeugbaus an, das im Prinzip die gesamte Produktion im Blick hat. Dieses System kommuniziert mit der MMS5, der Manufacturing Management Software von Fastems. Als MES übernimmt sie die Zellensteuerung und plant u. a. gemäß der Auftragsinformationen und Terminierungen autonom den Produktionsablauf im Fertigungssystem.
Die MMS5 erhält vom Fertigungsplanungs- und Steuerungssystem hierfür alle notwendigen Parameter und Programme, gleichzeitig empfängt sie bspw. Informationen zum Maschinenzustand, zu den Werkzeugen sowie zu den Programmlaufzeiten und übermittelt diese an die relevante Stellen, etwa bei der Fertigung eines NIO-Teils an einen Mitarbeiter von Daimler.
Das Werkzeugvoreinstellgerät im Fertigungssystem wiederum vermisst die Werkzeuge und übermittelt dieses Informationen an die RFID-Chips auf den Werkzeugen, damit diese Parameter vor der Bearbeitung eines Teils an die Maschinen übertragen werden können.
Die beiden BAZ als ein Bestandteil der dezentralen Intelligenz im Gesamtsystem übergeben in diesem Zusammenhang u. a. fertigungs- und prozessrelevante Informationen an die MMS5. Und dies ist nur ein kleiner, vereinfachter Ausschnitt des sehr komplexen Netzwerkes.“
Trotz der hochkomplexen Technik steht der Mensch nach Auffassung von Paul Schmidt weiterhin im Mittelpunkt: „Die Rolle des Maschinenbedieners ändert sich allerdings von einem reinen „Bediener“ in einen „Manager“ für das multifunktionale Fertigungssystem, der nicht mehr nur die Funktionen einer Einzelmaschine verstehen muss, sondern die Abläufe innerhalb dieses komplexen Netzwerkes.“
Direkter, ortsunabhängiger Systemzugriff
Um Probleme innerhalb dieses Netzwerkes und somit potenzielle Stillstandszeiten des Fertigungssystems zu vermeiden, müssen sich alle Technologiepartner des Projekts schnell, direct und zu jeder Zeit mit ihren Komponenten verbinden können. Der Fernzugriff bietet hierzu im Sinne einer Unabhängigkeit von Know-how und Produktion die beste Möglichkeit, denn die Projektpartner sitzen z. B. in Finnland, in der Schweiz sowie an verschiedensten Standorten in Deutschland. Per Fernzugriff können sie außerdem das Gesamtsystem weiterentwickeln, sollten sich neue Anforderung ergeben. In einem solchen Fall werden die entsprechenden Experten der Projektpartner kontaktiert, die sich dann auf ihre Komponente im Fertigungssystem aufschalten und Modifikationen, etwa Updates mit Funktionserweiterungen, vornehmen.
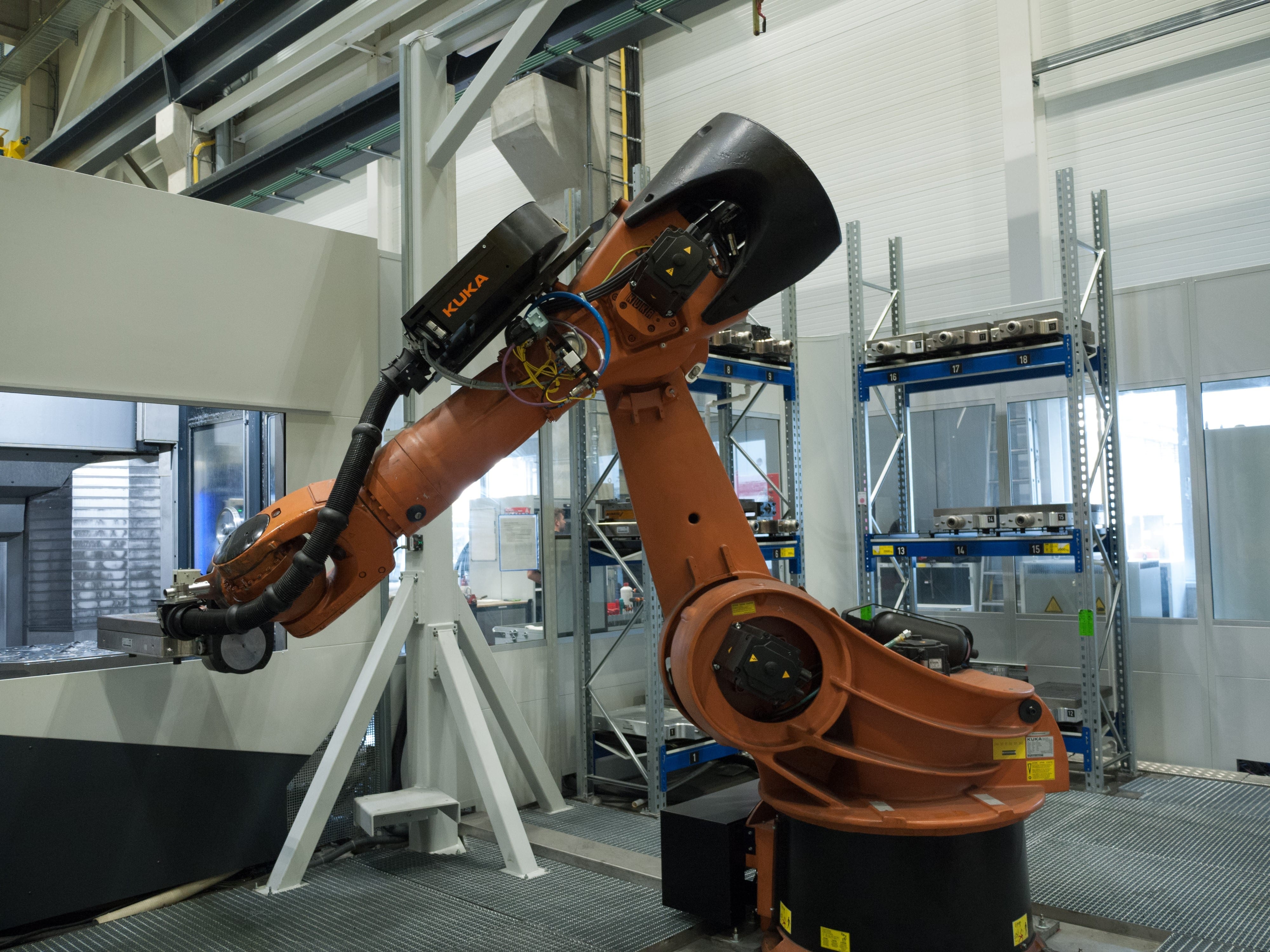
Der Roboter mit einer Traglast von 500 Kilogramm be- und endlädt die beiden Fünf-Achs-Bearbeitungszentren.
Produktion vereint zwei Welten
Wie bereits eingangs erwähnt, integriert das multifunktionale Fertigungssystem eine automatisierte Induktionshärteanlage. Das Induktionshärten, früher mit einem hohen logistischen Aufwand verbunden, wird nun von dem Roboter im System in seinen Nebenzeiten übernommen. Wann er das macht, entscheidet die Zellensteuerung MMS5 anhand der aktuellen Fertigungsplanung. Der Roboter ist somit nicht mehr nur reines Transportsystem, sondern auch eine Bearbeitungsmaschine, wobei der gesamte Prozess des Induktionshärtens „offline“ programmiert und vorab zu 100 Prozent auf Kollision simuliert wird, wodurch die virtuelle mit der realen Produktion verschmilzt.
Automatische Überwachung und selbstlernende Systeme
Eine wesentliche Forderung im Projekt galt dem Ziel einer intelligenten Maschinensensorik, die nicht nur den jeweiligen Zerspanungsprozess selbstständig überwacht, sondern hierbei sogar unbekannte Prozesse ohne Zugriff von außen einlernt. Wird demnach bspw. ein Werkzeug zum ersten Mal zur Bearbeitung auf einer der RX10 eingesetzt, muss das System die Prozessgrenzen im Hinblick auf Drehmoment und Schwingungen automatisch justieren, einlernen und abspeichern. Auf diese Weise werden statische Obergrenzen ermittelt, die Werkzeugüberlastungen erkennen, während im Bearbeitungsprozess mitlaufende dynamische Grenzen plötzliche Signaländerungen, B. einen Werkzeugbruch, identifizieren. Somit erhält die Maschinensensorik für jede Kombination aus Werkzeug, Material, Vorschub und Drehzahl ein über einen gewissen Zeitraum eingelerntes Szenario, das sich bei Bedarf jederzeit abrufen lässt. Wiederholt sich demnach ein bereits eingelernter Prozess mit einem spezifischen Werkzeug bei einem anderen Werkstück, hat das System alle hierfür erforderlichen, korrekten Parameter parat.
Permanente Optimierung im Sinne von Industrie 4.0
Seit 2015 ist das multifunktionale Fertigungssystem für Kleinteile nun im Werkzeugbau der Daimler AG in Betrieb. In der Zwischenzeit haben die Projektverantwortlichen noch an etlichen Stellschrauben drehen müssen, damit die Automationslösung alle Anforderungen erfüllte. Was allerdings nicht verwundern sollte, denn Industrie 4.0 ist kein statischer, sondern fortlaufender Prozess, der es erfordert, die Funktionalitäten und Fähigkeiten eines im Sinne der Strategie entwickelten Systems permanent zu optimieren und auszubauen.
(Dieser Artikel wurde in „werkstatt + betrieb“, Ausgabe 03/2017 veröffentlicht)
Related products:
Was können wir für Sie tun?
Rufen Sie uns an oder senden Sie uns einfach eine kurze Nachricht.
„*“ zeigt erforderliche Felder an