Automatisierungsoffensive bei Doesburg Components
Doesburg Components, ein Unternehmen der Gietburg-Gruppe, plant in den kommenden Jahren eine umfangreiche Investition zur Erweiterung seiner Produktion. Derzeit wird bereits eine spezielle Roboterzelle zur Bearbeitung von Gusskomponenten für Lkw-Bremssysteme eingesetzt, und in den nächsten Jahren sollen weitere Roboterzellen hinzukommen. Doesburg Components strebt an, mehr Produkte mit der gleichen Anzahl an Mitarbeitern zu produzieren, was nur durch einen hohen Automatisierungsgrad realisierbar ist.
„Es gibt drei wesentliche Gründe für die Automatisierung“, erklärt Jos Smeets, Direktor von Doesburg Components. „Der erste ist der relativ hohe Stundenlohn in Europa, der zweite die physische Belastung der Mitarbeiter, und der dritte der deutliche Mangel an hochqualifizierten Fachkräften. 2009 erzielten wir 60 % weniger Umsatz, aber heute arbeiten wir mit voller Produktionskapazität, und CNC-Bediener sind nahezu unmöglich zu finden. Von 10 eingegangenen Bewerbungen kann man hoffen, dass vielleicht eine von jemandem mit ausreichender Erfahrung kommt – so schwierig ist es.“ In den letzten Jahren hat Doesburg Components seine Mitarbeiterzahl von 60 auf 103 erhöht. „Aber weiteres Wachstum muss vor allem durch Automatisierung erfolgen“, erklärt Smeets. „Wir haben die wirtschaftliche Flaute genutzt, um mit neuen Kunden in Kontakt zu treten, die nun und in den kommenden Jahren eine große Menge an Produkten nachfragen. Die Menge der Bremsenprodukte, die in der neuen Roboterzelle verarbeitet werden, war ursprünglich auf 150.000 Teile pro Jahr festgelegt, aber der Kunde hat diese Nachfrage bereits auf 240.000 Teile erhöht.“
Investitionen
Doesburg Components hat weitere große Pläne in der Pipeline. Das Unternehmen plant, erheblich in den Ausbau seiner Maschinenkapazitäten zu investieren. Smeets erklärt: „2011 wird voraussichtlich ein besseres Jahr als 2008. Eine neue Generation von Lkw und Dieselmotoren wird auf den Markt kommen, und diese Lkw werden immer komplexere Teile enthalten. Unsere Ingenieure besuchen regelmäßig unsere Kunden, um neue Designs für diese Komponenten zu entwickeln. Nur auf diese Weise lässt sich eine vollautomatisierte Bearbeitung zu den niedrigstmöglichen Gesamtkosten erreichen.“ Um für die zukünftige Produktnachfrage gerüstet zu sein, plant Smeets, in den Jahren 2011 bis 2015 rund 10 Millionen Euro in neue, robotergestützte und automatisierte Bearbeitungszentren zu investieren. „Dabei stellen wir hohe Anforderungen an die Maschinen- und Roboterlieferanten“, betont Smeets. „Die Betriebszeiten in der Automobilindustrie sind entscheidend, deshalb kaufen wir nur Maschinen von Lieferanten, die einen schnellen Service gewährleisten können. Wir können es uns nicht leisten, einen ganzen Tag auf einen Techniker zu warten.“
Zwei Roboterzellen
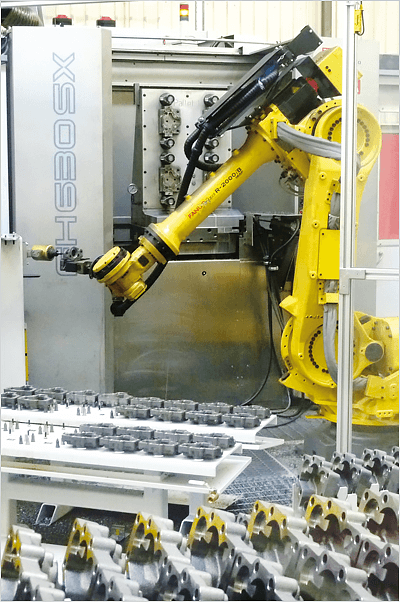
Nach der Bearbeitung entgraten die Roboter die Teile, bevor sie sie wieder zur Materialstation zurückbringen. Die neueste Roboterzelle ist der erste Teil der neuen Investitionsoffensive. Die Roboterzelle umfasst zwei Bearbeitungszentren: ein Quaser MK603S Vertikal-Bearbeitungszentrum und ein Toyoda FH630SX Horizontal-Bearbeitungszentrum. Die Maschinen wurden von Alfred van Meegen und Toyoda Europe in Krefeld, Deutschland, geliefert, während Fastems für die Automatisierung und die vollständige Lieferung des schlüsselfertigen Projekts verantwortlich war. Die Quaser- und Toyoda-Maschinen sind im rechten Winkel zueinander positioniert. Es gibt zwei Roboter, einen vor jeder Maschine. Zwischen den beiden Robotern befindet sich ein Puffertisch, auf dem sie die Produkte ablegen und von dem sie sie wieder aufnehmen. „Das ist wichtig für die Produktivität“, erklärt Henk Kremers von Valkworks. Valkworks ist der Fastems-Vertreter in den Benelux-Staaten. „Wir haben das Design auf dem Produkt des Kunden basierend entwickelt. Muss das Produkt auf beiden Seiten bearbeitet werden? Muss es horizontal oder vertikal bearbeitet werden? Wie lange dauert die Bearbeitung des Produkts und wie viel Zeit benötigt der Roboter für das Handling, einschließlich Entgraten? Nachdem wir all diese Aspekte betrachtet haben, entschieden wir, dass ein Roboter nicht ausreichen würde, da er mit den Bearbeitungszentren nicht Schritt halten könnte. Daher haben wir uns entschieden, zwei Roboter zu verwenden, mit einem Puffertisch zwischen ihnen.“
Hohe Geschwindigkeit
Selbst die beiden Fanuc-Roboter können kaum mit dem Quaser und dem Toyoda Schritt halten. Sie sind nahezu ständig in Bewegung. Der erste Roboter, vor dem Quaser, nimmt unbearbeitete Gusskomponenten von der Materialstation. Vier Teile werden gleichzeitig auf dem Spannsystem des Quasers eingespannt. Nach der Bearbeitung entgratet derselbe Roboter die Teile, während sie noch auf dem Spannsystem fixiert sind, und legt sie anschließend auf den Puffertisch. Der zweite Roboter nimmt dann die Teile vom Tisch und spannt sie auf dem Spannsystem des Toyoda ein. Zu diesem Zeitpunkt wurde nur eine Seite der Teile bearbeitet. Auch auf diesem Spannsystem werden vier Teile gleichzeitig eingespannt. Der Toyoda bearbeitet die andere Seite der Teile. Nach der Bearbeitung nimmt der zweite Roboter die Teile wieder einzeln auf und entgratet sie. Die fertigen Teile werden dann zurück auf den Puffertisch gelegt, von wo der erste Roboter sie aufnimmt und zurück zur Materialstation liefert. Dieser Arbeitszyklus wird kontinuierlich wiederholt. Eine Tür, die normalerweise offen bleibt, befindet sich zwischen den beiden Robotern. Der Puffertisch ist in zwei Hälften geteilt, und die Tür kann zwischen beiden Teilen hin und her gleiten. Kremers erklärt: „Die Tür ist Teil des Sicherheitssystems. Falls eine der beiden Maschinen für Messungen oder kleine Wartungsarbeiten ausfällt, kann die andere Roboterzelle dennoch 10 bis 12 Teile bearbeiten. Es ist wichtig, Maschinenstillstände auf ein absolutes Minimum zu reduzieren.“
Komplexität
Neben der Leistung der Roboterzelle bestand die größte Herausforderung dieses schlüsselfertigen Projekts in der Integration der Roboter-Software mit der Maschinensteuerung. Kremers fährt fort: „Die Roboterzelle wurde so konzipiert, dass sie etwa 30 Teile pro Stunde verarbeitet, von halbfertigen Gusskomponenten bis hin zu vollständig bearbeiteten und entgrateten Endprodukten. Das bedeutet, dass der Roboter die Maschine steuert. Der Roboter gibt der Maschine an, wann sie mit der Bearbeitung beginnen kann. Es ist auch wichtig, dass die Roboter niemals miteinander kollidieren.“ Fastems übernahm den gesamten Integrationsprozess, einschließlich der Software. Der Leitrechner ist mit einer Fernverbindung zum Fastems-Hauptsitz in Finnland ausgestattet, sodass bei Problemen diese sofort von dort aus gelöst werden können. Kremers schließt: „Als die Roboterzelle bei Doesburg Components geliefert wurde, funktionierte sie nahezu sofort einwandfrei. Es war einfach eine gründliche Vorbereitung und das Wissen darum, was der Kunde möchte.“
AUTOR: Paul Quaedvlieg
Über Doesburg Components
Doesburg Components aus Nieuw-Bergen ist hauptsächlich auf die Lieferung und zunehmend auf die Entwicklung und Konstruktion von installationsfertigen Komponenten (Guss- und bearbeiteten Gusskomponenten) für die internationale Lkw- und Landwirtschaftsindustrie spezialisiert. Die Komponenten werden an Kunden wie DAF, Deutz, Leyland Trucks, Daimler, MTU, Wabco, Lely und McCormick geliefert. Doesburg Components ist Teil der Gietburg-Gruppe, die auch Modelmakerij Hengelo, Gieterij Doesburg, Cirex in Almelo, Gietburg und das kürzlich übernommene Arbin Components aus Venlo umfasst.
Related products:
Das klingt
interessant?
Melden Sie sich einfach bei uns –
wir sind nur einen Anruf oder eine E-Mail entfernt!
„*“ zeigt erforderliche Felder an