Äußerst agil und kundenspezifisch –
Durchgängig automatisierte Fertigung von Kupplungskomponenten
Was ist der Unterschied zwischen Flexibilität und Agilität?
Eine Automatisierungslösung in Form einer agilen Fertigungszelle (AMC – Agile Manufacturing Cell), die Fastems gemeinsam mit dem Getriebespezialisten Flender entwickelte, vermittelt eine konkrete Vorstellung.
Das Kupplungswerk von Flender beschäftigt rund 420 Mitarbeiter, davon allein zirka 220 in der Produktion. Am Standort in Bocholt werden auf etwa 27.000 Quadratmetern nicht schaltbare Kupplungen gefertigt, darunter Zahn-, Bahn-, Strömungs- und Windkraftkupplungen sowie anwendungsspezifische Kupplungen. „Jährlich stellen wir mehrere Tausend Motorkupplungen her, bestehend aus zwei Kupplungshälften. Und jede Kupplung erhält je nach Bauteil eine spezifische Verzahnung“, erklärt Günter Thebingbuß, stellvertretender Fertigungsleiter im Kupplungswerk.
Deutliche Reduzierung an Sondermaschinen
Solche Verzahnungen wurden in der Vergangenheit auf Sondermaschinen gefertigt. „Aufgrund der verschiedenen, sehr aufwendigen Prozesse benötigten wir daher eine Vielzahl an Maschinen für die Herstellung der Mitnehmerringe und Kupplungsteile als Hauptkomponenten der Motorkupplungen“, so Günter Thebingbuß.
Mit Blick auf Kostensenkungen und damit der Reduzierung der Vielfalt an Maschinen sowie des hierfür notwendigen Personaleinsatzes wurde bereits vor mehreren Jahren über den Erwerb von Dreh-Fräszentren nachgedacht, die die Fertigung von unterschiedlichen Verzahnungen auf wenige neue Anlagen ermöglichten. Hierzu Günter Thebingbuß: „Im Zusammenhang mit der Fertigung von Motorkupplungen entschieden wir uns u.a. für zwei Dreh-Fräszentren vom Typ DMG CTX gamma 1250 TC, da sich mit ihnen u.a. auch das Wälzschälen als ein für uns entscheidender Prozessschritt in der Fertigung realisieren ließ. Zudem entschlossen wir uns, die Fertigung mit diesen Maschinen zu automatisieren.“
Komplexe Anforderung an die Automatisierung
Aus diesem Grunde wurde mit einer ganzen Reihe an potenziellen Anbietern gesprochen, die eine solche Automatisierung realisieren können. Als Partner blieb am Ende nur Fastems übrig, denn die Anforderungen an das Projekt waren, wie die zu fertigenden Kupplungskomponenten, durchaus komplex.
Marco Krane, hauptverantwortlicher Anlagenbediener der agilen Fertigungszelle, präzisiert: „Das Setup der Maschinen sollte komplett automatisiert sein. Das betraf nicht nur den Werkzeugwechsel, sondern auch das Rüsten mit den für die Werkstücke jeweils erforderlichen Spannmitteln. Vor jedem Auftrag musste zudem ein automatischer Ressourcencheck durchgeführt werden, und auch die NC-Programme sollten auftragsspezifisch an die Maschinen übertragen werden. Die Gesamtlösung musste letztendlich in der Lage sein, hochflexibel kleine bis mittlere Losgrößen mit hoher Teilvarianz zu produzieren.“

Erfolgreiche Zusammenarbeit: Stephan Limbach, Solution Sales Manager Fastems, Günter Thebingbuß, stellvertretender Fertigungsleiter, und Marco Krane, hauptverantwortlicher Anlagenbediener der Automatisierungslösung (von links).
Produktionsstraße mit zentraler Zellensteuerung
Die gemeinsam mit Fastems entwickelte Automatisierung besteht nach Aussagen von Stephan Limbach, Solution Sales Manager Fastems, im Wesentlichen aus zwei Zellen mit einem zentralen Turmspeicher:
„Zelle 1 dient der Materiallogistik für das Einschleusen von Rohmaterial und Ausschleusen der Fertigteile mit integrierter Wasch- und Konservierungsstation. Hieran schließen sich die Speicher für Rohmaterial, Halbfertig- und Fertigteile sowie für die Werkzeuge und Spannmittel an.
Die Zelle 2 bildet schließlich den eigentlichen Fertigungsbereich.“
Als übergeordnete Intelligenz der AMC fungiert die Manufacturing Management Software (MMS) von Fastems, die die Produktion gemäß der Daten aus dem ERP-System automatisch plant, ausführt und überwacht.
Die MMS übernimmt zudem die Werkzeugverwaltung inkl. Standzeitenüberwachung, koordiniert u.a. das automatisierte Setup der Maschinen mit einem Roboter und kontrolliert vor jedem Auftrag, ob alle Ressourcen (z. B. Werkzeuge, NC-Programme, Rohmaterial) für die Fertigung bereitstehen.
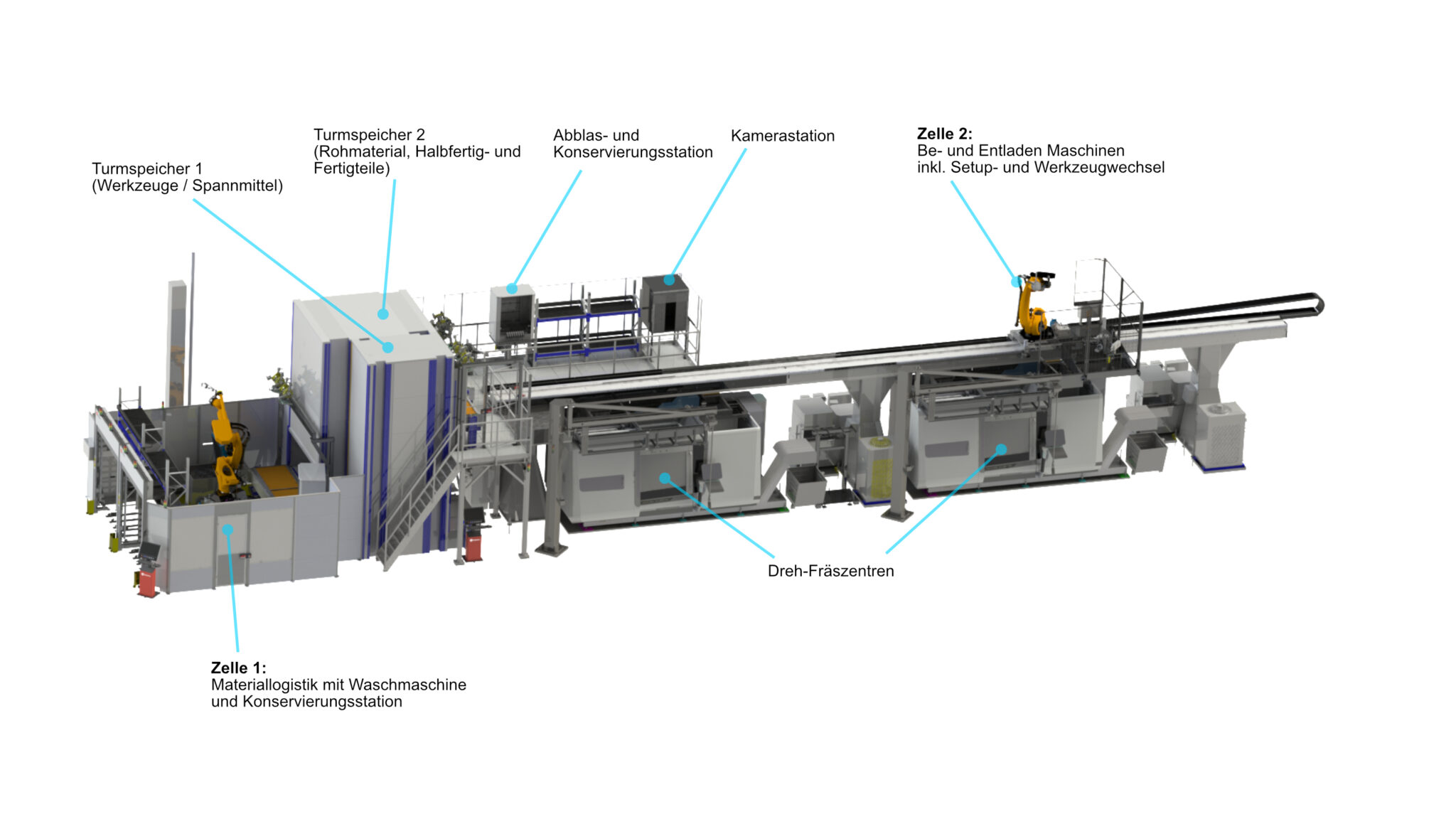
Gesamtübersicht der Agilen Fertigungszelle: Zelle 1 mit Roboter für die Materiallogistik inkl. Waschmaschine und Konservierungsstation (links), der Turmspeicher für Werkstücke, Werkzeuge und Spannmittel, der Turmspeicher 2 für Rohmaterial sowie Halbfertig- und Fertigteile sowie die Zelle 2 u.a. mit dem Portalroboter und den zwei Dreh-Fräszentren.
Durchgängige Lösung
mit besonderen Merkmalen
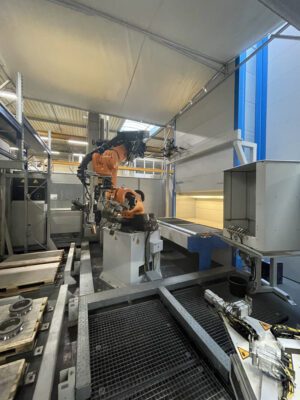
Zelle 1 dient der Materiallogistik mit einem Roboter. Darüber hinaus sind das Waschen und die Konservierung der Fertigteile als weitere Prozessschritte integriert. Rechts unten eine Verstelleinheit, mit der sich der Hub für den jeweils erforderlichen Greiferdurchmesser für die Werkstückhandhabung justieren lässt. In Zelle 2 befindet sich eine weitere Einheit.
Ein konkreter Blick auf die Automatisierung verdeutlicht die Funktionsweise des Systems. In Zelle 1 wird einem Roboter lageorientiert Rohmaterial auf einer Palette zugeführt.
Um das Rohmaterial dem jeweiligen Fertigungsauftrag zuordnen zu können, wird ein Barcode an jeder Palette eingescannt. Anschließend legt der Roboter die Rohteile im Werkstückspeicher ab.
Auf der gegenüberliegenden Seite des Speichers befindet sich die Zelle 2 mit den beiden Dreh-Fräszentren, die jeweils über eine Hauptspindel und ein Magazin für 36 variabel besetzbare Werkzeuge verfügen, um flexibel jedes Bauteil auf jeder Anlage fertigen zu können. Zusätzlich bietet der Turmspeicher Platz für weitere 400 Werkzeuge.
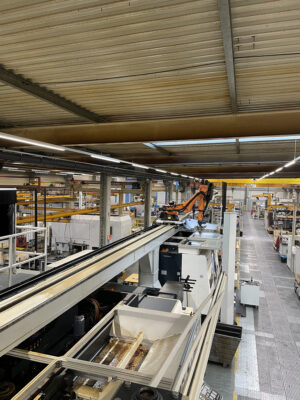
Der Portalroboter in Zelle 2 übernimmt nicht nur die Werkstückhandhabung, sondern auch das komplette Setup der Maschinen mit Werkzeugen und Spannmitteln.
In Zelle 2 übernimmt ein Portal-Roboter zusätzlich zur Werkstückhandhabung das Rüsten der Maschinen mit den jeweils für die Produktion benötigten Werkzeugen und Spannmitteln.
Pro Monat sind hierbei zirka 19 Setupwechsel für die Spannmittel an beiden Maschinen erforderlich. Hinzu kommen in jeder Stunde rund 30 Werkzeugwechsel pro Dreh-Fräszentrum.
Im Zusammenhang mit der Werkstückhandhabung weist die Zelle einige Besonderheiten auf. Hierzu gehört ein Greifermagazin für den automatisierten Greiferwechsel zur Handhabung von Werkstücken, Werkzeugen und Spannmitteln mit dem Roboter. An zwei integrierten Verstelleinheiten (eine in Zelle 1) lässt sich außerdem der Hub für den jeweils erforderlichen Greiferdurchmesser für das Werkstückhandling vollautomatisch justieren.
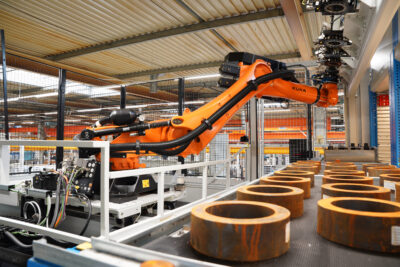
Der Roboter in Zelle 2 vor dem Turmspeicher. Darüber befindet sich das Greifermagazin für den automatisierten Greiferwechsel zur Handhabung von Werkstücken, Werkzeugen und Spannmitteln. (Bild: Flender GmbH)
Die Plattform, auf dem der Portal-Roboter verfährt, integriert eine Wendestation, um Werkstücke für die Zweiseitenbearbeitung handhaben zu können.
„Hinzu kommt eine Kamerastation, die die robotergestützte Ausrichtung spezifischer und ebenfalls in zwei Aufspannungen zu fertigenden Teile ermöglicht.
Diese Teile erhalten in OP10 eine Bohrung und müssen daher für OP20 vom Roboter exakt im Spannfutter der Maschine positioniert werden“, erklärt Marco Krane.
Wir konnten unsere Produktivität signifikant steigern und darüber hinaus aufgrund der durchgängigen Automatisierung unsere schon hohe Fertigungsqualität verbessern.
Hohe Produktivität durch hauptzeitparallelen Werkzeugwechsel
Für die eigentliche Produktion rüstet der Portal-Roboter zunächst eine der beiden Maschinen mit den jeweils erforderlichen Spannmitteln. „Ab hier entscheidet im Grunde die MMS, ob zuerst das Werkstück eingespannt oder die für die Bearbeitung notwendigen Werkzeuge zur Maschine transportiert werden“, so Günter Thebingbuß. Während die Maschine läuft, übernimmt der Roboter weitere Tätigkeiten für die noch anstehenden Fertigungsaufträge. Hierbei wechselt er u.a. hauptzeitparallel die Werkzeuge in den Magazinen, wobei die MMS die Bereitstellung von Werkzeugen im Voraus planen kann. Ist ein Bauteil bearbeitet, wird es vom Roboter in den Speicher gelegt. „Bei Halbfertigteilen kann es durchaus sein, dass ein Werkstück nach OP10 zunächst zum Speicher und erst zu einem späteren Zeitpunkt für OP20 wieder zu einer Maschine transportiert wird. Auch hier arbeitet die Zelle völlig flexibel“, meint Günter Thebingbuß.
Alle im Speicher befindlichen Fertigteile gelangen mithilfe des Roboters in Zelle 1 zunächst zur Wasch- und Konservierungsstation, bevor sie auf einer Palette abgelegt werden.
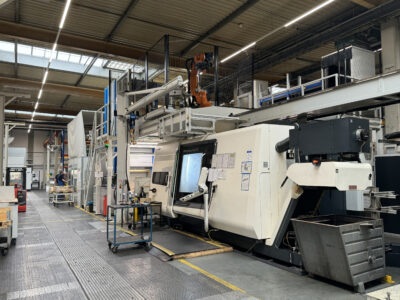
Mit der AMC wurde der komplette Materialfluss vom Roh- bis hin zum komplexen Fertigteil in einer Automatisierungslösung mit zentraler Zellensteuerung realisiert.
Agile Zerspanung auch
kleiner Lose mit hoher Teilevarianz
Mit der AMC konnte das Kupplungswerk von Flender den kompletten Materialfluss vom Roh- bis hin zum Fertigteil in einer Automatisierungslösung mit zentraler Zellensteuerung realisieren, die im Sinne hauptzeitparalleler Abläufe wesentlich zur Entkopplung einzelner Prozesse in der Zerspanung beiträgt.
Das gesamte Werkstückhandling sowie das komplette Setup der Maschinen inkl. Spannmittel- und Werkzeugwechsel erfolgen vollautomatisch.
„Momentan produzieren wir aufgrund der hohen Auslastung vor allem die Mitnehmerringe für die Kupplungen. Das sind zirka 20 bis 60 Stück pro Auftrag mit Bearbeitungszeiten von 30 bis 70 Minuten pro Teil, wobei es sich hier um rund 25 verschiedene Materialnummern handelt. Darüber hinaus sind wir bei vorhandenen Stammdaten in der Lage, kurzfristig auch kleinere Lose von bspw. 3 Bauteilen zu fertigen. Produziert wird in drei Schichten inklusive einer komplett mannlosen Schicht. Hierdurch konnten wir unsere Produktivität signifikant steigern und darüber hinaus aufgrund der durchgängigen Automatisierung unsere schon hohe Fertigungsqualität verbessern“, so das Fazit von Günter Thebingbuß zur erfolgreichen Zusammenarbeit mit Fastems.