Wie ein Schweizer Uhrwerk
Mit Automation von Fastems zu anspruchsvollen Produkten
Eine Domäne der Knoepfel AG ist die hochautomatisierte Fertigung von großvolumigen Präzisionsbauteilen, mit der sich das Schweizer Familienunternehmen mit rund 50 Mitarbeitenden positioniert hat. Ein seit mehr als einem Jahrzehnt hochverfügbares Multi-Level-System (MLS) von Fastems in einem flexiblen Fertigungssystem (FFS) spielt in diesem Zusammenhang eine entscheidende Rolle.
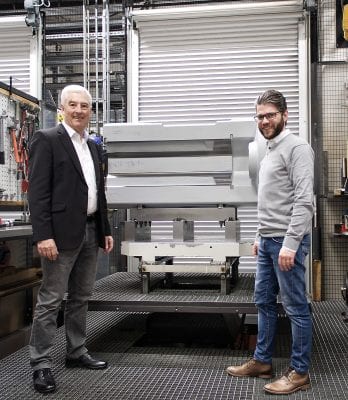
Urs Knoepfel, Mitglied in Verwaltungsrat der Knoepfel AG (links) und Roman Sgier, Verkaufsleiter des Unternehmens.
„Als wir 1991 unsere jetzige Produktionsstätte in Gaismoos bezogen, reagierten viele Außenstehende zumeist mit Erstaunen, wenn sie erfuhren, dass wir unsere Werkhallen mit einer Klimatisierung ausgestattet hatten“, erinnert sich Urs Knoepfel, Mitglied im Verwaltungsrat der Knoepfel AG mit Sitz in Walzenhausen am Bodensee.
Was ursprünglich zum Wohle der Mitarbeiter gedacht war, erwies sich im Nachhinein als sehr weitsichtige Investition.
„Ohne die noch vor kurzem modernisierte und mit einer modernen Wärmerückgewinnung ausgestatteten Klimaanlage, die uns eine konstante Raumtemperatur in der Produktion gewährleistet, könnten wir unsere Bauteile mit der hohen Präzision und Qualität nicht herstellen“, betont Verkaufsleiter Roman Sgier.
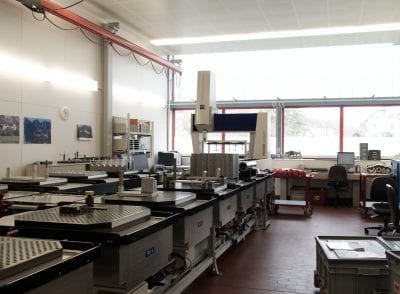
Das Mess- und Prüfzentrum erfüllt u.a. durch den Einsatz von 3D-Koordinatenmessmaschinen höchste Prüfanforderungen, wobei durch unbemanntes Messen auch große Prüfmengen bewältigt werden.
Vom Präzisionsbauteil bis zum Prüfzentrum
Die Knoepfel AG verfügt derzeit über drei Hauptgeschäftsfelder: eine Präzisionsteilefertigung, eine rotative Fertigung sowie ein Mess- und Prüfzentrum. Roman Sgier präzisiert: „Die rotative Fertigung besteht aus sechs Drehzentren, mit denen wir Teile in einem Durchmesserbereich von 30 bis 680mm, bis maximal 2.000 mm Länge und Werkstückgewichten bis 600 kg produzieren. Mit unseren CNC-Hochpräzisions-Hartdrehzellen fertigen wir bspw. Bauteile mit Toleranzen kleiner 5μm. Unser Mess- und Prüfzentrum in abgetrennten Räumen erfüllt durch Einsatz von 3D-Koordinatenmessmaschinen höchste Prüfanforderungen. Integriert ist eine Messmaschine mit Prüfgenauigkeit unter 1μm mit automatischer Zuführung von 13 Paletten für unbemanntes Messen – einzigartig in der Schweiz. Komplettiert wird das Leistungsspektrum schließlich mit einer automatisierten Präzisionsteilefertigung, die uns die unbemannte kubische CNC-Komplettbearbeitung von Werkstücken mit einem Gewicht bis 2.500 kg ermöglicht.“
Breitgefächertes Produktspektrum für Industrie, Mobility und Aerospace
Das Produktspektrum von Knoepfel ist entsprechend breit gefächert: von Bauteilen für Injektionswerkzeuge in der Kunststoffverarbeitung zur Herstellung von Pet-Rohlingen, über Schlüsselkomponenten für Helikopter und die Space-Industrie (z. B. Satelliten) bis hin zu hochpräzisen Lagergehäusen für Schiffsdieselmotoren, um nur einige Beispiele zu nennen. Gefertigt wird vor allem in kleinen und mittleren Serien mit Losgrößen von 20 bis 100 Stück pro Jahr, wobei die größeren Bauteile zumeist auf Kleinserien entfallen.
Wichtiger Schritt in die Zukunft
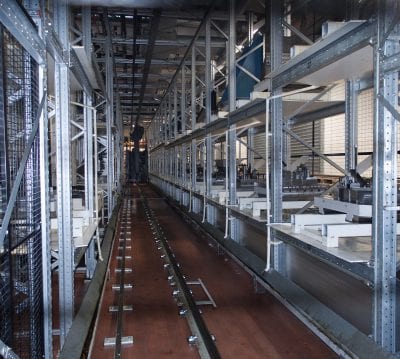
Das System von Fastems bietet Platz für insgesamt 40 Maschinenpaletten mit einer Tragkraft pro Palette von 2,5 Tonnen.
Höchste Präzision ist das Maß aller Dinge bei der Knoepfel AG, allerdings stets unter dem Aspekt der Wirtschaftlichkeit, wie Urs Knoepfel unterstreicht: „Die Schweiz ist ein Hochlohnland. Daher haben wir sehr früh in Automatisierung investiert, z. B. bereits 1997 in Maschinen mit Palettenpools. Um hinsichtlich Komplexität und Genauigkeit einen Vorsprung zu bekommen und somit Teile zu produzieren, die andere nicht fertigen können, mussten wir in diese Richtung weiterdenken. Daher haben wir uns 2008 dazu entschieden, in ein Multi-Level-System, ausgelegt für 3 Horizontal-BAZ, von Fastems zu investieren. Für uns ein entscheidender Schritt in die Zukunft, denn mit diesem System bekamen wir die Möglichkeit, hochautomatisiert und sehr flexibel Hochpräzisionsteile zu fertigen, die unsere Kunden von uns erwarten – und das just-in-time.“
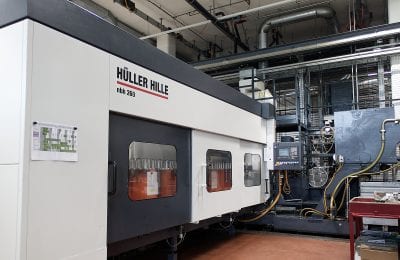
An dem MLS von Fastems sind insgesamt drei Bearbeitungszentren von Hüller Hille (eine NBH 290 und zwei NBH 260) gekoppelt.
Bedarfsorientiert mit bis zu drei BAZ erweitert
Das von Beginn an auf eine Erweiterung mit Bearbeitungszentren (BAZ) ausgelegte MLS-MD (Medium Duty) von Fastems mit einer Tragkraft von 2,5 Tonnen pro Palette bietet auf einer Länge von 40 Metern und mit knapp 6 Metern Höhe Platz für insgesamt 40 Maschinenpaletten. Für den Teiletransfer integriert das System zudem zwei Be- und Entladestationen.
Zunächst wurde ein horizontales Bearbeitungszentrum NBH 290 von Hüller Hille mit Hochgenauigkeitspaket an das System angebunden. „Mit dieser Lösung haben wir erste Erfahrungen gesammelt und nach rund zwei Jahren eine weitere Anlage von Hüller Hille vom Typ NBH 260 ergänzt“, so Urs Knoepfel. 2014 kam dann eine dritte Maschine gleichen Typs hinzu.
20 verschiedene Großbauteile permanent im System
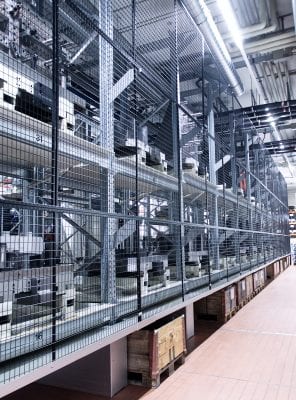
Das MLS-MD erstreckt sich über eine Länge von 40 Metern durch die automatisierte Präzisionsfertigung der Knoepfel AG.
„Mit diesem FFS produzieren wir in der Regel permanent zirka 20 verschiedene Bauteile, zumeist in zwei Aufspannungen, daher benötigen wir insgesamt 40 Paletten. Ausgelegt sind die Anlagen aber für die Fertigung von mehr als 100 Teile pro Jahr, wobei wir hier viele wiederkehrende Produkte haben“, erklärt Roman Sgier.
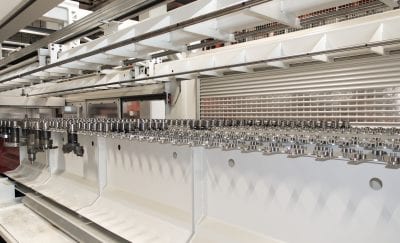
400 zusätzliche Werkzeuge werden über die von Knoepfel selbst entwickelte Erweiterung der NBH 290 zur Verfügung gestellt, so dass die Anlage auf insgesamt 800 Tools zugreifen kann.
Entsprechend ausgestattet sind die Werkzeugmagazine der beiden NBH 260 mit jeweils 400 Tools. Eine Besonderheit ist allerdings die Kapazität der NBH 290 mit insgesamt 800 HSK-100 Werkzeugen. Hierzu Urs Knoepfel: Wir haben eigens hierfür im Rahmen einer Diplomarbeit eine Erweiterung entwickelt, die den Einsatz von 400 zusätzlichen Werkzeugen ermöglicht. Die hohe Anzahl der Werkzeugplätze für alle Maschinen ist erforderlich, damit wir die gleichsam hochkomplexe wie hochgenaue Bearbeitung der Werkstücke auch unbemannt, z. B. während der Nacht, sicherstellen können.“
Bis zu 40 Stunden unbemannt produzieren
Bemannt produziert wird hingegen ausschließlich im Einschichtbetrieb. Jeweils ein Mitarbeiter ist dann für eine Maschine zuständig. Hinzu kommen zwei weitere Mitarbeiter für die Be- und Entladestationen. „Unser Ziel ist stets, alle Maschinen bis zum Schichtbeginn am nächsten Morgen mannlos weiterproduzieren zu lassen. Das ist natürlich immer auch von der Konstellation der jeweiligen Aufträge und der zu fertigenden Bauteile sowie deren Bearbeitungszeiten abhängig“, meint Roman Sgier.
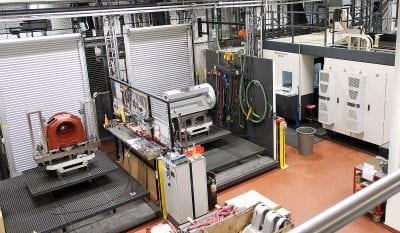
Das MLS-MD verfügt über zwei Be- und Entladestationen für den Teiletransfer.
Bearbeitet werden zu rund 50 Prozent Eisen- und Aluminiumgussteile sowie verschiedenste Stahl- und Aluminiumqualitäten. Die Bearbeitungszeiten sind daher sehr unterschiedlich und bewegen sich durchschnittlich pro Maschinenpalette zwischen einer und 10 Stunden. „Haben wir einen optimalen Arbeitsvorrat im MLS, erreichen wir über das Wochenende mitunter auch bis zu 40 unbemannte Stunden am Stück, wobei die NBH 290 im Grunde immer durchläuft “, so Sgier. Pro Jahr lassen sich auf diese Weise mit der Systemlösung von Fastems bis zu 5.000 Spindelstunden je Maschine erzielen.
Erfolgreiche Partnerschaft wird fortgesetzt
„Das FFS ist ein zentraler Bestandteil unserer automatisierten Fertigung und überzeugt durch eine extrem hohe Verfügbarkeit. Da wir außerdem mindestens zwei Mal im Jahr eine präventive Instandhaltung vornehmen, hat uns das System noch nie im Stich gelassen“,
so das Fazit von Urs Knoepfel, der aufgrund seiner durchweg positiven Erfahrungen keinen Zweifel an einer weiteren erfolgreichen Zusammenarbeit mit Fastems lässt.
So plant die Knoepfel AG u.a. den Ausbau der Produktion mit zusätzlichen Maschinen, wobei zur Automatisierung der Neuinvestitionen eine Roboterzelle für die Handhabung schwerer Werkstücke und ein Flexibler Paletten Container (FPC) als kompaktes, flexibles Fertigungssystem von Fastems vorgesehen sind. Urs Knoepfel: „Außerdem ist geplant, unser derzeitiges Leistungsspektrum durch eine Baugruppenmontage ergänzen. Mit einem Neubau, der zurzeit als zukünftiges Lager auf unserem Firmengrundstück entsteht, schaffen wir hierfür den notwendigen Platz in unserer Produktion.“