Komplettlösung meistert alle Herausforderungen
Eine Automatisierungslösung, die sowohl eine durchgängige Qualitätsprüfung als auch die Produktkennzeichnung mit einbezieht, dies sind nur einige der Besonderheiten, die ein mittelständisches, finnisches Unternehmen auszeichnet. Allem voran steht eine hochproduktive und äußerst wirtschaftliche spanabhebende Fertigung. Einblicke in eine Produktionsstrategie, die auch deutschen Unternehmen interessante Impulse liefern könnte.
Der Grundstein für die Konepaja Sihvo Oy mit Sitz in Hyvinkää, rund 50 Kilometer nördlich von Helsinki, wurde bereits vor fast 60 Jahren gelegt. „Unter dem jetzigen Namen firmieren wir seit 1983 und ich führe das Unternehmen mit derzeit etwas mehr als 40 Mitarbeitern in der nunmehr dritten Generation“, berichtet Simo Sihvo.
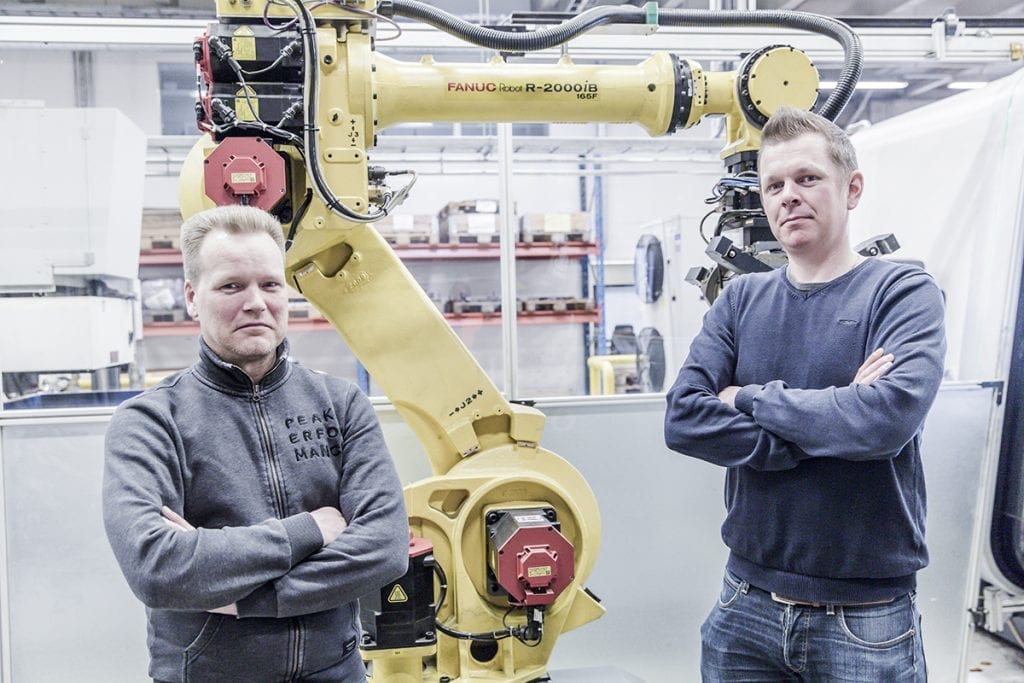
Tuuka Pasanen (links), Leiter der Qualitätssicherung, und Simo Sihvo, Geschäftsführer der Konepaja Sihvo Oy, haben gemeinsam mit Fastems in Finnland eine wohl einzigartige Automationslösung realisiert.
Hoher Qualitätsanspruch an die Fertigung
Beim konkreten Produktspektrum der Konepaja Sihvo möchte der Geschäftsführer nur ungern ins Detail gehen. Nur soweit: Ein Großteil der Fertigteile werden in Anwendungen eingesetzt, in denen hohe Sicherheitsanforderungen an die einzelnen Komponenten gestellt werden – entsprechend hoch ist der Qualitätsanspruch der Auftraggeber.
Darüber hinaus bietet das Unternehmen verschiedenste Dienstleistungen an, darunter 3D-Messungen nach Kundenspezifikationen sowie die Montage von Baugruppen, deren Komponenten in der Regel ebenfalls von der Konepaja Sihvo gefertigt werden.
„Die Dimensionen, der von uns ausschließlich für den finnischen Markt gefertigten Teile, bewegen sich mit Durchmessern von rund 100mm bis 1250mm gewissermaßen im Midsize-Bereich. Bearbeitet werden hierbei auf einer Produktionsfläche von zirka 3.000 Quadratmetern verschiedenste Metalle, darunter vor allem Gusseisen, wobei der Anteil an Drehteilen relativ hoch ist. Das zeigt sich u.a. auch beim Maschinenpark, der aktuell aus sechs Dreh-/Fräszentren, 20 Drehmaschinen und sieben Fräszentren besteht“, erklärt Tuuka Pasanen, Leiter der Qualitätssicherung von der Konepaja Sihvo.
Konsquente Investition in Automation
Angesichts hoher Lohnkosten und einem latenten Mangel am Fachpersonal, also ähnlichen Bedingungen, mit denen sich oftmals auch deutsche KMUs konfrontiert sehen, setzt die Konepaja Sihvo konsequent auf Automatisierung. Hierzu Simo Sihvo: „1987 haben wir in die erste Roboterzelle für das automatisierte Be- und Entladen einer Dreh-/Fräsmaschine investiert. Zuvor lohnten sich derartige Investitionen nicht, da unsere Kunden uns vor allem immer dann als Lohnfertiger benötigten, wenn ihre eigenen Produktionskapazitäten an Grenzen stießen. Anfang der 90-iger Jahre änderte sich das allerdings, als unsere Auftraggeber zunehmend mit einem Outsourcing ihrer Produktionen begannen. Mittlerweile bewegen sich unsere Losgrößen durchschnittlich zwischen 30 und 300 Stück. Ob wir kleinere Stückzahlen manuell oder automatisiert fertigen, hängt aber immer davon ab, ob es sich um Einzel- oder Wiederholaufträge handelt, denn im letzteren Fall kann eine automatisierte Produktion durchaus wirtschaftlich sein. Mittlerweile haben wir insgesamt sechs Roboterzellen im Einsatz.“
Großauftrag mit besonderen Anforderungen
Im Jahr 2012 erhielt Sihvo einen Großauftrag zur Fertigung spezifischer, rotationssymetrischer Teile aus Gusseisen mit einem Durchmesser von rund 700mm. „Aufgrund der zu erwartenden Losgrößen von rund 10.000 Stück pro Jahr stand für uns von vorneherein fest, für die Teilebearbeitung in eine weitere Roboterzelle zu investieren“, meint Tuuka Pasanen und betont: „Eine der besonderen Anforderungen seitens des Auftraggebers bestand jedoch darin, die Fertigteile zu 100 Prozent zu prüfen. Daher benötigten wir eine Komplettlösung, die nicht nur das automatische Be- und Entladen der Maschinen übernehmen sollte, sondern die auch eine durchgängige Qualitätsprüfung als integraler Bestandteil der Gesamtautomation ermöglichte.“
“Im letzten Jahr haben wir pro Maschine insgesamt 5.500 Spindelstunden erzielt und werden in diesem Jahr diese Marke wohl noch überschreiten. Noch produktiver und wirtschaftlicher geht es wohl kaum!”
– Tuukka Pasanen
Zuverlässiger Partner gesucht
Seinerzeit stand die Konepaja Sihvo aufgrund eines bereits realisierten Projektes in Zusammenhang mit einer Roboterzelle in Kontakt mit Fastems. In diesem Projekt hatte der Systemintegrator bewiesen, dass er in der Lage war, auch eine Werkstückprüfung in das Automationskonzept einer Roboterzelle zu integrieren. „Aus unserer Sicht kam daher im Grunde nur Fastems als Partner für das ambitionierte Neuprojekt in Frage und gaben daher 2012 die Automationslösung in Auftrag“, erklärt Simo Sihvo und Tuuka Pasanen ergänzt: „Wir wurden nicht enttäuscht, denn was Fastems zu dieser Zeit für uns entwickelte, war in Finnland wirklich einzigartig.“
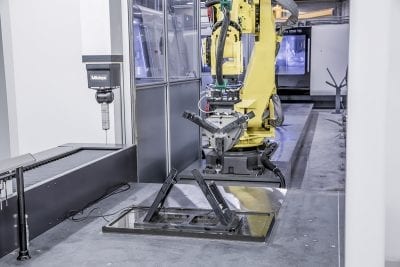
Ist ein Teil fertiggestellt, wird es vom Roboter zum Messplatz transportiert. Die Messergebnisse werden direkt an die Maschinensteuerung übertragen. So kann der Prozess optimiert werden.
Komplettlösung mit integrierter Qualitätssicherung
Selbst aus heutiger Sicht kann man dem Qualitätsmanager der Konepaja Sihvo nur beipflichten. Zu den Einzelheiten: Die Roboterzelle besteht aus zwei Fünf-Achs-Dreh-/Fräszentren, die von einem Shuttle-Roboter mit einer Traglast von 165 kg be- und entladen werden. Zentraler Bestandteil der Automationslösung ist eine Messmaschine, die sich in einem klimatisierten Raum innerhalb der Zelle befindet. Ist ein Teil fertiggestellt, wird es vom Roboter zum Messplatz transportiert, wobei sich hierzu ein Rolltor zum Messraum öffnet und während der Prüfung schließt.
„Der Messraum verfügt zusätzlich über ein zweites Rolltor, das den Zugang von außerhalb der Roboterzelle erlaubt. So können wir neben den in der Zelle gefertigten Teilen bei Bedarf noch weitere Werkstücke prüfen“, so Tuuka Pasanen, der das Augenmerk auf die besonderen Anforderungen an die Automationslösung richtet.
Durchgängige Prüfung der Fertigteile
Bei jedem Werkstück ist die Einhaltung von vorgegebenen Toleranzen an bis zu fünf unterschiedlichen Messpunkten durchgängig zu überprüfen. Hierzu wird die Fertigungsqualität einer regelmäßigen Analyse unterzogen. Weicht der Fertigungsprozess von den zu erwartenden Ergebnissen ab, wird die Anzahl der Prüfungen pro Werkstück erhöht. Tuukka Pasanen: „Darüber hinaus führen wir nach einer gewissen Anzahl an gefertigten Teilen eine komplette 3D-Messung durch. Wird die Produktion außerdem nach der Fertigstellung einer Produktionscharge zum Rüsten der Roboterzelle für die nächste Charge gestoppt, überprüfen wir alle relevanten Parameter und können daher entsprechende Anpassungen vornehmen, um ggfs. den Fertigungsprozess weiter zu stabilisieren.“
Selbstoptimierende Prozesse
Die wichtigsten Faktoren für eine hohe Fertigungsqualität sind nach Aussagen des Qualitätsmanagers vor allem die Prüfergebnisse der Messmaschine und demzufolge auch die Temperaturen der Werkstücke während der Bearbeitung. „Wir haben die Dreh-/Fräszentren daher eigens mit einer Temperaturkompensation ausstatten lassen. Wichtig ist aber, dass wir neben den Temperaturmessungen auch die Ergebnisse der Messmaschine an die jeweiligen Maschinensteuerungen übertragen können. Das ist ein fortlaufender, automatisierter Prozess während der Produktion. Bewegen sich bspw. die Ergebnisse der Messungen an den Fertigteilen innerhalb der Toleranzen nach oben oder unten, erfolgt eine automatische Optimierung des Fertigungsprozesses, z. B. in dem die Werkzeuge in den Maschinen nachjustiert oder ausgetauscht werden. Jedes Bearbeitungszentrum verfügt daher über ein ausreichend dimensioniertes Werkzeugmagazin mit insgesamt 120 Werkzeugen.“ Dass sich die Messergebnisse an den Werkstücken einmal außerhalb der Toleranzen bewegen könnten, ist nach Meinung von Tuukka Pasanen eher ausgeschlossen, da das Gesamtsystem dieser Möglichkeit während der laufenden Produktion permanent und vor allem völlig autonom entgegenwirkt.
Vollumfängliche Dokumentation
Belegen kann der Qualitätsmanager dies außerdem durch eine lückenlose Dokumentation der Fertigungsqualität. „Unsere Ansprüche sind analog zu den Kundenerwartungen sehr hoch, daher werden alle Prozess- und Messergebnisse der Fertigung zusammen mit den Rohmaterialdaten in einer Datenbank gesammelt. Jedes einzelne Werkstück wird überdies im Zuge der Fertigung noch in der Roboterzelle gekennzeichnet und erhält somit alle relevanten Informationen, die für eine nahtlose Rückverfolgung der Produktionsqualität erforderlich sind.“
Rekordverdächtige Spindelstunden
Die Roboterzelle von Fastems ist nun seit rund fünf Jahren bei der Konepaja Sihvo in Betrieb. „In dieser Zeit haben wir viele wertvolle Erfahrungen gesammelt und überaus positive Ergebnisse erzielt“, resümiert der Geschäftsführer. Aus dem Munde von Simo Sihvo klingt diese Aussage vor dem Hintergrund, dass die Automationslösung rund um die Uhr in drei Schichten fertigt und gemessen an den Produktionsstunden eines Jahres zu rund 80 bis 90 Prozent permanent ausgelastet ist, schon fast wie Understatement. Doch Sihvo nennt auch konkrete Zahlen und wagt einen Blick in die Zukunft: „Im letzten Jahr haben wir pro Maschine insgesamt 5.500 Spindelstunden erzielt und werden in diesem Jahr diese Marke wohl noch überschreiten. Noch produktiver und wirtschaftlicher geht es wohl kaum!“
Veröffentlicht in der NC Fertigung: „Automatisiert – rund Um die Uhr“ (Ausgabe 07-08/2018)