Digitaler „Pilot“ steigert Blisk-Produktion – Intelligente Software sichert hohe Verfügbarkeit komplexer Automationslösung
Systemintegratoren sollten möglichst beide Disziplinen beherrschen, sowohl die Hard- als auch die Software. Vor allem die „softe“ Seite der Automatisierung hat nicht zuletzt aufgrund von Industrie 4.0 immens an Bedeutung gewonnen. Wie sehr, zeigt ein anspruchsvolles Projekt der MTU Aero Engines AG. Der Triebwerkhersteller suchte zur Realisierung einer hochautomatisierten Blisk-Fertigung einen Partner und entschied sich für Fastems, denn das Unternehmen mit langjähriger eigener Softwareentwicklung konnte vor allem die notwendige Intelligenz zur anvisierten Lösung beisteuern.
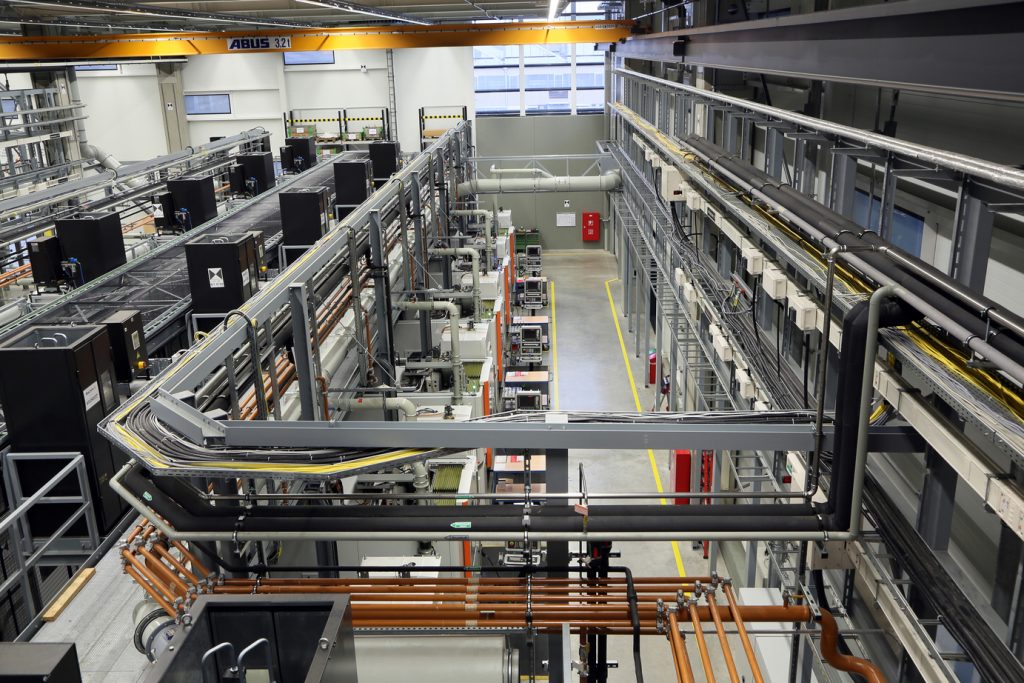
Die Verkettung der Fräs- und Drehfräsmaschinen erfolgt über 4 Flexible Fertigungssysteme, unterteilt in ein Hauptsystem und drei Subsysteme. In der Abbildung oben ist links eines der Subsysteme zu sehen. (© MTU Aero Engines)
„Dieses System ist einzigartig“, meint Walter Sürth. Und wer die Details zur Umsetzung des ambitionierten Projektes zur hochautomatisierten Fertigung von Titan-Blisks kennt, der wird dem Leiter der Blisk-Produktion von MTU Aero Engines nicht widersprechen. Doch der Reihe nach.
Mit der Produktion von Blisks (siehe unten) begann das Unternehmen mit Sitz in München Mitte der 1990-er Jahre. „Seinerzeit haben wir mit den Entwicklung der Triebwerkskomponenten für den Eurofighter angefangen und dann über mehr als zehn Jahre u. a. Bauteile für das TP400, einem Triebwerk für den Militärtransporter Airbus A400M, produziert“, erklärt Sürth. Durch die Entwicklung des Turbofantriebswerks PW6000 für den Airbus A318 gemeinsam mit Pratt & Whitney gelang MTU Aero Engines der Einstieg in die Blisk-Fertigung für den zivilen Bereich. Als „technologischen Quantensprung“ bezeichnet der Produktionsleiter dieses Triebwerk, da erstmals zwischen dem Fan mit seinen großen Schaufeln und der Verdichterstufe ein Getriebe geschaltet wurde, das beide Komponenten voneinander entkoppelte: „Die Ergebnisse sind eine geringere Geräuschentwicklung und vor allem erhebliche Einsparungen beim Kerosin-Verbrauch.“
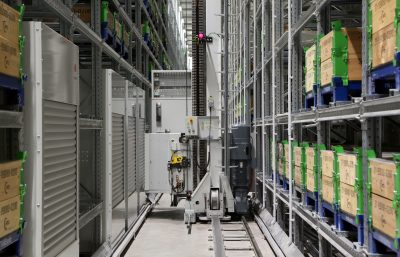
Das zentrale MLS verfügt über zwei Regalbediengeräte, die in einer Stunde rund 75 Transportbewegungen vornehmen (© MTU Aero Engines)
5-fache Produktionssteigerung auf knapper Fläche
Mit dem Einstieg in den zivilen Sektor stieg auch die Nachfrage nach Blisks für Getriebefans. „Wir waren zur damaligen Zeit auf eine Produktion von rund 600 Blisks pro Jahr für militärisch genutzte Triebwerke ausgelegt. Gemäß unserer Prognosen mussten wir die Fertigungskapazitäten jedoch auf rund 3.000 Titan-Blisks pro Jahr sowohl für den militärischen als auch zivilen Bereich erhöhen – und das hier am Standort“, berichtet Walter Sürth.
Die Möglichkeiten waren somit räumlich begrenzt. Auf dem Betriebsgelände wurde der Bau einer Halle mit einer Produktionsfläche von 5.000 Quadratmeter geplant, die u. a. den erforderlichen Platz für einen umfangreichen Maschinenpark zur Verfügung stellen sollte. Der Produktionsleiter vermittelt einen Eindruck von den Erwartungen: „Die Dreh-Fräszentren mussten rund 5.000 Spindelstunden und die Fräszentren mindestens 6.000 Spindelstunden jährlich für den prognostizierten Produktionsausstoß leisten. Hinzu kommt, dass wir die hochkomplexen Blisks, je nach Bauteil benötigen wir für die Bearbeitung eines Werkstücks 40 bis 100 Arbeitsschritte, in Losgröße 1 fertigen, da wir sonst zu lange Durchlaufzeiten hätten. Die Durchlaufzeit für einen Blisk beträgt derzeit durchschnittlich 60 Tage. Daher benötigen wir eine hocheffiziente Logistik, eingebunden in eine gleichsam intelligente wie leistungsfähige Automationslösung.“
Intelligentes MES gab den Ausschlag
Die Suche nach einem geeigneten Partner, mit dem sich ein solches Projekt, genauer die Verkettung von insgesamt 24 Fräs- und sieben Dreh-Fräszentren in einer einzigen hochautomatisierten Lösung, realisieren ließe, gestaltete sich nach Aussagen von Walter Sürth allerdings als nicht so einfach. Die meisten Anbieter winkten angesichts der Komplexität und Dimensionen des Projekts von vorneherein ab. Am Ende blieben nur noch zwei Unternehmen, die sich die hohen Anforderungen zutrauten. „Wir haben uns letztendlich für Fastems entschieden, da dieses Unternehmen zusätzlich zur Hardware auch eine im eigenen Hause entwickelte Software als intelligentes Manufacturing Execution System (MES) zur Steuerung der Gesamtlösung anbieten konnte. Das gab letztendlich den Ausschlag.“
Mit dem Bau der Halle wurde im Jahr 2012 begonnen. Parallel zur Bauplanung habe man sich bereits mit dem Automationssystem beschäftigt und die Halle quasi simultan mit den Multi-Level-Systemen (MLS) zur Verkettung der Maschinen errichtet. Bereits im April 2013 konnte die neue Titan-Blisk-Fertigung ihren Betrieb aufnehmen.
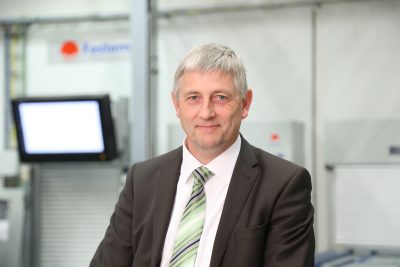
Walter Sürth, Leiter Blisk-Produktion bei MTU Aero Engines (© MTU Aero Engines)
Vier MLS, 31 Maschinen, ein System
„Einer der wesentlichen Merkmale unseres Automationskonzeptes ist die Materialfluss-Entkopplung. Wir fertigen nicht in einer Linie, sondern können jeden anstehenden Arbeitsvorgang auf jede Maschine verteilen. Daher sind wir auch in der Lage, die Werkzeugmaschinen auf engstem Raum unterzubringen“, erklärt Walter Sürth.
Die Verkettung der Fräs- als auch Dreh-Fräsmaschinen erfolgt über vier Flexible Fertigungssysteme, darunter ein Portallader und drei MLS von Fastems, unterteilt in ein Hauptsystem und drei Subsysteme, die gemeinsam eine Systemlösung bilden. Der Hauptstrang erstreckt sich über eine Länge von rund 90 Metern mit einer Höhe von acht Metern. Er ist doppeltseitig aufgebaut und bietet auf insgesamt 15 Ebenen (acht frontseitig und sieben in der hinteren Reihe) Platz für insgesamt 1.031 Paletten (Maschinen- und Materialpaletten). Hieran schließen sich zwei MLS-Stränge mit jeweils 12 Fräszentren vom Typ Mikron HPM800UHD an. Jeder Strang verkettet somit je sechs gegenüberliegende Werkzeugmaschinen. Am Portallader befinden sich sieben Dreh-Fräszentren vom Typ Monforts UniCen 1000.
75 Transportbewegungen pro Stunde
Hierzu Manfred Sürth: „Das Hauptsystem verfügt über zwei Regalbediengeräte (RGB). Immerhin haben wir in einer Stunde zirka 75 Transportbewegungen im System, was mit einem RGB kaum zu schaffen wäre. Darüber hinaus dient das zweite Bediengerät als Backup. Sollte also ein RGB ausfallen, bedeutet das nicht gleichzeitig einen Produktionsstillstand.“
Jeweils ein Regalbediengerät in den beiden Subsystemen für die BAZ von Mikron be- und entladen die Maschinen von deren Rückseite, um den Mitarbeitern frontseitig einen ungehinderten Zugang zum Maschinenraum zu ermöglichen. Diese Prämisse gilt ebenfalls für die Dreh-Fräszentren, deren Beschickung in diesem Fall über einen Portallader erfolgt.
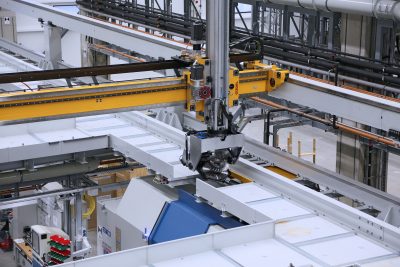
Die sieben Drehfräszentren von Monforts werden über einen Portallader bedient (© MTU Aero Engines)
Echte Effizienzsteigerung
Die Monforts können nach Aussagen des Produktionsleiters schon alleine wegen der Be- und Entladung nicht so autark laufen, wie die Fräszentren mit Langläufern und Bearbeitungszeiten zwischen 20 und 40 Stunden. „Die Automation mit dem Portallader verschafft uns allerdings die entscheidende Effizienzsteigerung. Trotz sehr kurzer Bearbeitungszeiten von 20 Minuten bis maximal zwei Stunden konnten wir hierdurch den Durchsatz an diesen Maschinen um den Faktor 4 bis 5 erhöhen“, betont Walter Sürth und hebt im Zusammenhang mit dem Anspruch an eine hohe Produktivität auch die Fertigungsqualität hervor: „Vom technologischen Anspruch ist die Produktion von Blisks das Optimum, was man einer Werkzeugmaschine in Punkto Präzision und damit Wiederholgenauigkeit abverlangen kann. Wenn wir allerdings schon beim Rüsten der Werkstücke Toleranzen verschenken, dann nützen auch keine hochgenauen Maschinen.“ Aus diesem Grunde verfügt das Haupt-MLS über drei Hochgenauigkeitsrüstplätze von Fastems, mit denen die Vorrichtungen auf Null-Punkt-Spannsystemen sowohl für die Dreh- als auch Dreh-Fräszentren bestückt werden. „Die Genauigkeit der Rüststationen ist vergleichbar mit den Werkzeugmaschinen. Potenzielle Fehler werden somit vermieden und können ergo erst gar nicht in die Fertigung gelangen“, so Sürth.
Individuelle Steuerung als Nervensystem
Gewissermaßen als Nervensystem der gesamten Automationslösung fungiert die Manufacturing Management System (MMS) von Fastems, die eigens an die extrem hohen und auch sehr spezifischen Anforderungen der Blisk-Fertigung angepasst wurde. Die Steuerung plant die gesamte Produktion für 96 Stunden im voraus und muss somit in der Lage sein, permanent bis zu 1.500 Aufträge zu verwalten. Analog hierzu können das zirka 150.000 Fertigungsoperationen sein. Gibt es eine Terminverschiebung, so plant die MMS5 in Echtzeit die gesamte Fertigung neu, wiederum für vier Tage im voraus.
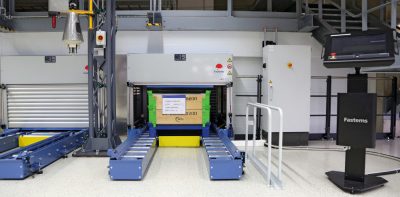
Das Haupt-MLS ist mit einer Schleuse zum Prüfbereich ausgestattet. Auf Anforderung durch einen Mitarbeiter koordiniert die MMS5 den Transport eines Halbfertig- oder Fertigteils zur Qualitätsprüfung (© MTU Aero Engines)
Auch alle manuellen Prozesse im Blick
Die u. a. an das ERP-System angebundene Steuerung führt aber nicht nur völlig autonom die Feinplanung sowie Organisation der automatisierten Fertigung gemäß Terminierung respektive Priorisierung der Aufträge durch, sondern hat auch alle manuellen Prozesse innerhalb der Produktion im Blick, wie Walter Sürth weiß: „Wird ein Werkstück für eine manuelle Tätigkeit entnommen und später wieder dem System zugeführt, behält die Software die Übersicht, in dem sie diese Aktivitäten in der Bestandsführung berücksichtigt.“ Ein gutes Beispiel hierfür ist die Qualitätsprüfung von Halbfertig- bzw. Fertigteilen. Die MMS5 koordiniert in diesem Zusammenhang nach Anforderung durch einen Werker sogar den Transport des Prüflings in einen Messraum, der hierzu mittels einer Übergabestation an das Haupt-MLS oberhalb der Fertigung angedockt ist.
„Zur Produktionsplanung übernimmt die Software außerdem die komplette Verfügbarkeitsprüfung aller Betriebsmittel. Hierbei kontrolliert sie z. B., ob sich die Werkstücke zur Bearbeitung im System befinden, verwaltet zudem sämtliche Werkzeuge inklusive deren Standzeiten sowie die NC-Programme, die von der MMS5 je nach Produktionsverlauf an die betreffenden Maschinen übertragen werden“, beschreibt der Produktionsleiter einige weitere Merkmale.
Intelligente „chaotische“ Fertigung
Grundsätzlich plane die Steuerung die Produktion im Hinblick auf die Fertigstellung eines Auftrags unter der Vorgabe maximaler Spindelauslastung. In der nichtlinearen Produktion bei MTU Aero Engines sei dies etwas anders. „Spezifische Werkstücke werden bei uns nur auf bestimmten Maschinen gefertigt. Die Steuerung hat auch diese Informationen, sodass sie im Sinne einer hocheffizienten chaotischen Fertigung solche Bauteile anhand der beschriebenen Ressourcen diesen Maschinen direkt zuordnen kann. Die gesamte Logistik dieser und auch aller anderen Werkstücke ist dabei vollautomatisiert“, unterstreicht Sürth.
Produktion fast rund um die Uhr
Gabelstapler oder ähnliche Transportfahrzeuge sucht man daher in der Blisk-Fertigung vergeblich. Der Wareneingang besteht aus einer Schleuse in einer Hallenaußenwand, über die das Rohmaterial in mit RFID-Chips ausgestatteten Behältern direkt an ein Transportband in der Halle übergeben wird. „Da die mit einem Lesegerät automatisch ausgelesene ID des Chips stets eine Sachstandkopplung zu einem SAP-Auftrag hat, weiß das System, wann das Material für einen konkreten Auftrag in unserer Produktion eingetroffen ist. Ab diesem Moment beginnt auch die Bestandsführung und Planung der MMS5“, erklärt Walter Sürth, der ein positives Resümee zur Gesamtlösung ziehen kann und dabei bereits in die Zukunft schaut: „Gefertigt wird dreischichtig an sechs Tagen die Woche. An Sonn- und Feiertagen kommen dann noch auf den Mikron drei komplette Geisterschichten hinzu. Dennoch sind wir nicht am Ende unserer Auslastung angelangt. Die Prognosen sind mittlerweile auf rund 7.000 Blisks für den militärischen und zivilen Sektor gestiegen. Wir werden daher in Zukunft die militärische Blisk-Fertigung aus unserer jetzigen Produktion ausgliedern und mit unserem Automationssystem ausschließlich Bauteile für den zivilen Bereich fertigen. Die Kapazität der Anlage beläuft sich dann auf die Produktion von zirka 4.000 Blisks pro Jahr.“
Blade Integrated Disk-Blisk
Eine Blisk (Blade Integrated Disk) ist eine aus einem Stück gefertigte Rotorstufe für Verdichter von Triebwerken. Man unterscheidet zwischen Nickel-Blisks, die mit einem elektrochemischen Verfahren hergestellt werden, und Titan-Blisks, die ausnahmslos zerspanend gefertigt werden. Vereinfacht dargestellt bestehen moderne Turbofan-Triebwerke im Wesentlichen aus einem Nieder- und Hochdruckverdichter und einer Brennkammer. Zusätzlich befindet sich vor den Verdichterstufen ein Fan mit großen Schaufeln. Dieser wird über eine Welle vom Niederdruckverdichter angetrieben und beschleunigt die von vorne einströmende Luft, von der etwa 1/10 in das Kerntriebwerk gelangt. Die restlichen 9/10 sorgen für den Schub. Bei einem Getriebefan-Triebwerk ist die Verdichter-Stufe vom Fan über ein Getriebe entkoppelt. Hierdurch kann der Fan langsamer laufen, als die Niederdruckturbine, was zu geringeren Geräuschemissionen und höheren Treibstoffeinsparungen führt.
(Erschienen in „WB Werkstatt + Betrieb“, Ausgabe 05/2017)
Was können wir für Sie tun?
Rufen Sie uns an oder senden Sie uns einfach eine kurze Nachricht.
„*“ zeigt erforderliche Felder an