RAD Torque Systems sichert Arbeitsplätze mit neuem Automatisierungssystem
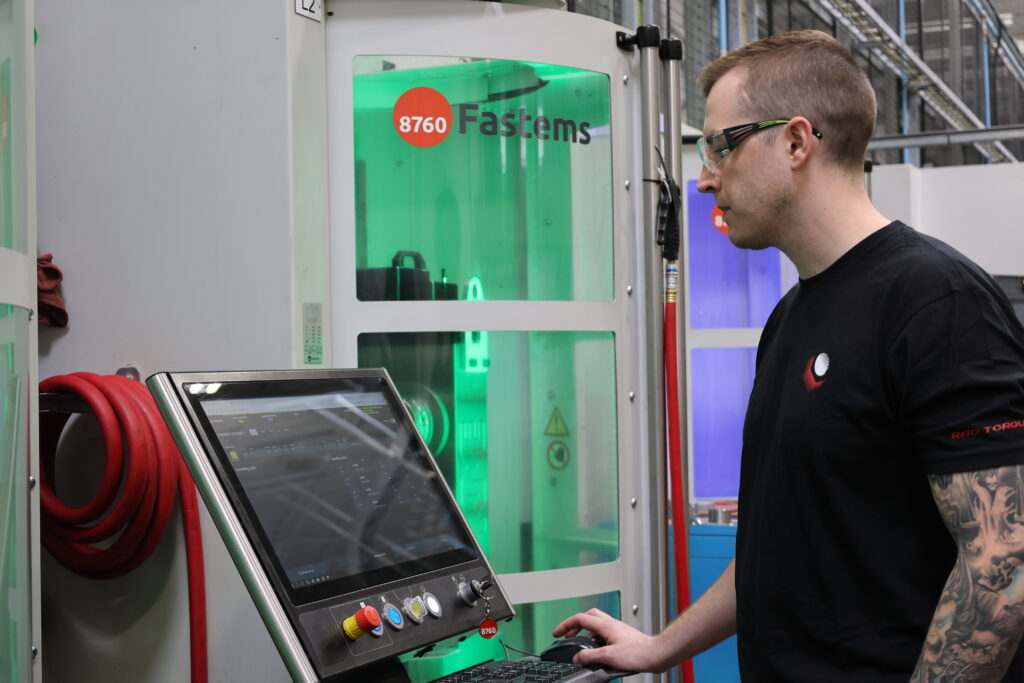
Situation
Dan Provost, Präsident und Gründer von RAD Torque Systems in Abbotsford, B.C., suchte Unterstützung für die Reshoring-Bemühungen seines Unternehmens und entschied sich für Fastems aus West Chester, Ohio, als Automatisierungspartner. Vor 30 Jahren begann Provost mit seiner Firma in einer Garage, heute ist RAD Torque Systems ein führender Hersteller von industriellen Drehmomentschlüsseln und Zubehör, der Branchen wie Energie, Luft- und Raumfahrt, Eisenbahn und Fertigung mit zuverlässigen Werkzeugen beliefert. Das Unternehmen produziert nicht nur die Drehmomentschlüssel, sondern auch die dazugehörige Software, Elektronik und sogar die Getriebelager – alles aus einer Hand.
Fastems, ein familiengeführtes Unternehmen mit über 5.000 weltweiten Installationen, liefert Paletten- und Roboter-Automatisierungssysteme, die stets mit der leistungsstarken Manufacturing Management Software (MMS) ausgestattet sind. Die Partnerschaft zwischen RAD Torque Systems und Fastems ist ein Paradebeispiel dafür, wie Automatisierung und Innovationsgeist lokale Arbeitsplätze sichern können.
„Wir sind kein Auftragsfertiger“, betont Greg Doughty, Mechanical Production Manager bei RAD Torque Systems. „Wir stellen unsere Werkzeuge selbst her, entwickeln die Software, die Hardware und die Elektronik – alles entsteht hier vor Ort.“
Für Provost und sein Team war Offshoring nie eine Option. Er war entschlossen, die gesamte Fertigung in Kanada zu halten und sein Team mit lokalem Personal zu erweitern. Um die Produktion im eigenen Haus zu sichern und dabei gleichzeitig profitabel zu bleiben, setzt RAD Torque Systems auf Spitzentechnologie und fortschrittliche Automatisierungslösungen.
Die Lösung
RAD Torque Systems fand die ideale Lösung in einem Fastems ONE flexiblen Fertigungssystem (FMS) und einer ERP-Software, die die beiden Okuma MB-4000 Horizontal-Bearbeitungszentren im ursprünglichen Werk des Unternehmens optimal unterstützen. In der neuesten Produktionsstätte sorgt ein weiteres Fastems FMS dafür, dass vier zusätzliche Okuma MB-4000 Maschinen nahtlos und effizient betrieben werden.
Laut Greg Doughty war der Hauptgrund für die Einführung des Fastems-Systems die drastische Reduzierung der Rüstzeiten. „Die Automatisierung war eine bedeutende Investition, aber eine, die unverzichtbar war“, erklärt er.
„Ohne Automatisierung würden wir eine enorm größere Anzahl an Mitarbeitern und vertikalen Maschinen benötigen, um die gewünschten Produktionsmengen zu erreichen. Der Platzbedarf würde exponentiell steigen,“ fügt er hinzu.
Das Herzstück der Produktion von RAD Torque Systems bilden die vier Okuma MB-4000 Horizontal-Bearbeitungszentren. Ein dreistufiges Automatisierungssystem verbindet die Maschinen mit 84 Palettenplätzen und drei Beladestationen.
Das Ergebnis: Höchste Effizienz, minimale Stillstandszeiten und ein zukunftsfähiger Produktionsprozess.
Doughty erklärte, dass anfangs einiges an Vorbereitung erforderlich war. Fastems liefert das System erst aus, wenn bestimmte Voraussetzungen im Werk erfüllt sind – ein entscheidender Schritt, um eine reibungslose Integration sicherzustellen.
Als alles bereit war, reisten zertifizierte Fastems-Techniker zur Installation an. „Die Gründlichkeit war beeindruckend“, betont Doughty. „Bevor sie das System übergaben, prüften sie es bis ins kleinste Detail. Keine Abkürzungen, keine Unklarheiten – alles wurde perfekt umgesetzt.“
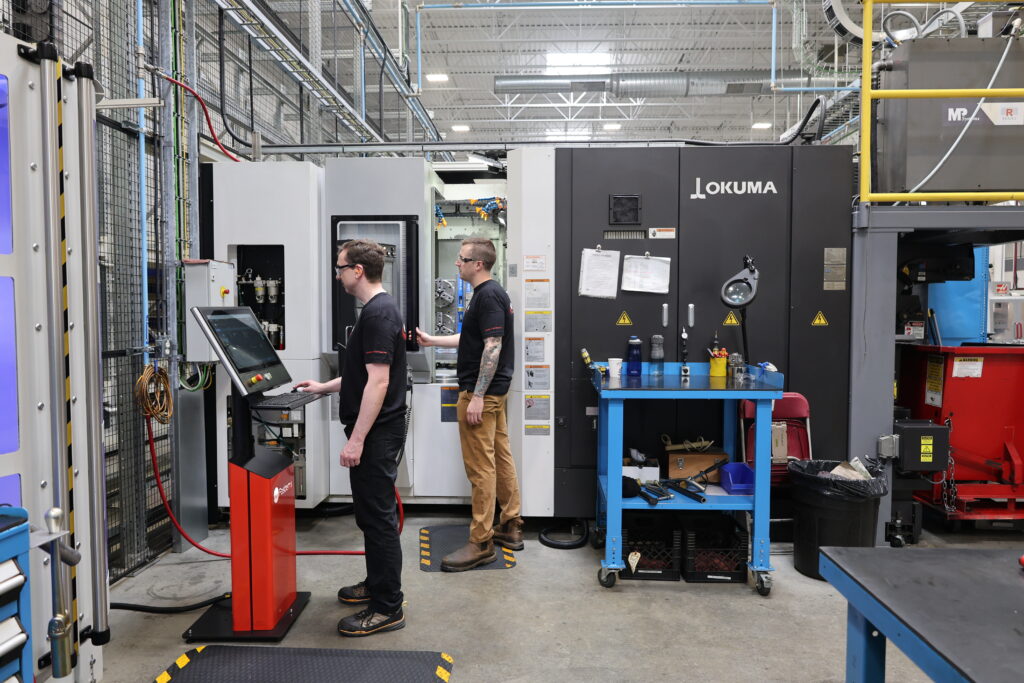
Ein Fastems-Techniker blieb zwei Wochen vor Ort, um das Team von RAD Torque Systems bei der Einführung des Systems zu unterstützen. Die Mitarbeiter wurden intensiv geschult und auf ihre Kenntnisse und Fähigkeiten geprüft. Als der Techniker abreiste, war sichergestellt, dass das Team das System eigenständig und sicher betreiben konnte.
RAD Torque Systems behandelte das neue System nicht als einfache Plug-and-Play-Lösung. Stattdessen investierte das Team Zeit und Aufwand, um sämtliche relevanten Daten zu Teilen, Maschinen, Zeitplänen und Versandprozessen präzise einzugeben. Dank der langjährigen Zusammenarbeit von Okuma und Fastems arbeiten ihre Produkte nahtlos zusammen und teilen Daten effizient. Heute laufen über 320 Programme auf dem System.
Die vier Okuma MB-4000 Horizontal-Bearbeitungszentren sind das Herzstück der Produktion. Schon allein liefern sie schnelle und präzise Ergebnisse, aber in Verbindung mit dem Fastems FMS ONE System erreichen sie ein völlig neues Leistungsniveau.
Robert Humphries, International Sales Manager bei Fastems für die Regionen West-USA und Kanada, betont die Bedeutung der drei Beladestationen: „Im mannlosen Betrieb werden alle Palettenpuffer vollständig gefüllt, was die Spindeln stark beansprucht. Diese Paletten müssen entladen und am nächsten Tag mit neuem Material bestückt werden“, erklärt Humphries. „Mit drei Beladestationen kann RAD Torque das System effizient ‚aufladen‘, sodass morgens direkt weitere Teile produziert werden können.“
Das System wird vollständig von der Fastems Manufacturing Management Software (MMS) gesteuert, die Produktion plant, priorisiert und Ressourcen effizient einsetzt. Die MMS organisiert Werkzeuge und Materialien projektbezogen und liefert umfassende KPI-Berichte, einschließlich Maschinenstatus, Alarmmeldungen, Produktionshistorie und einem Dashboard. Mit dem Modul Production Documents können Benutzer Palettendetails aufrufen und auf zugehörige PDFs, Zeichnungen oder wichtige Informationen zugreifen. So wird das gesamte Wissen zu einem Bauteil zentral verfügbar gemacht. Das Team kann auf einen Blick Spindelauslastung und Maschinenleistung überwachen.
Dank des automatisierten Systems sind nur noch wenige manuelle Eingriffe erforderlich. Die Produktion läuft nahezu eigenständig, effizient und zukunftssicher – eine perfekte Kombination aus Technologie und Innovation.
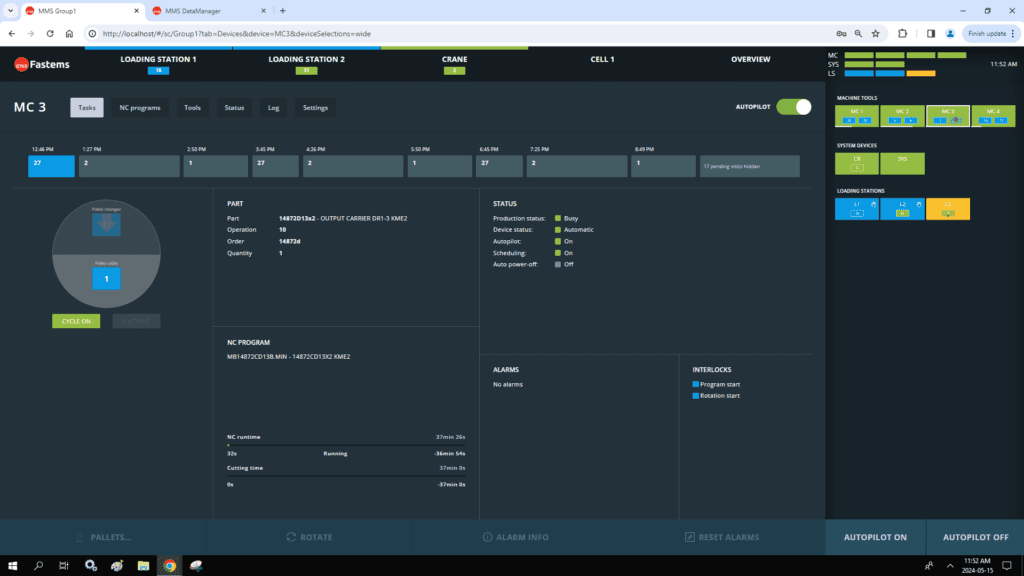
Automatisierung auf höchstem Niveau: RAD Torque Systems steigert Effizienz und Wachstum
Das automatisierte System von RAD Torque Systems sorgt für einen durchgängigen Produktionsfluss: Bediener laden Teile in die Stationen, woraufhin die Paletten im Lagerbereich auf ihren Einsatz warten. Sobald die Software sie aufruft, bringt ein rotierendes Palettensystem sie in eine freie Maschine. Nach der Bearbeitung wird die Palette zur Entladestation transportiert, während die nächste Palette mit einem neuen Teil bereitgestellt wird. Dieser Prozess, der sich mehrmals täglich wiederholt, hält alle vier horizontalen Bearbeitungszentren kontinuierlich in Betrieb.
Jedes Bearbeitungszentrum ist mit einer Werkzeugmatrix ausgestattet, die bis zu 220 Werkzeuge fasst. Mit durchschnittlich 218 Werkzeugen pro Maschine werden Wartezeiten praktisch eliminiert.
Jared Earnshaw, Werkstattleiter bei RAD Torque Systems, dokumentiert mit dem MMS die beeindruckenden Effizienzsteigerungen seit der Einführung der Fastems-Technologie. Die Spindelauslastung in den automatisierten Zellen liegt konstant bei 95 bis 98 Prozent, mit seltenen Ausreißern unter 90 Prozent. Vor der Automatisierung lag die Effizienz bei lediglich 45 Prozent. Zusätzlich nutzt Earnshaw das MMS, um Maschinenstillstände zu überwachen und Engpässe in der Produktion zu identifizieren.
Obwohl das System für mannlose Fertigung ausgelegt ist, sorgt derzeit eine 24-Stunden-Besetzung für die Prüfung von Toleranzen, insbesondere bei Bearbeitungszyklen von nur drei Minuten. Dies gewährleistet eine optimale Qualitätssicherung.
Die Drehmomentschlüssel von RAD Torque Systems, die sich durch ihre planetengetriebene Bauweise auszeichnen, bieten kontrolliertes Drehmoment mit kontinuierlicher Rotation. Sie sind ergonomisch und sicher, mit einem integrierten Motor im Griff. Das Unternehmen produziert täglich über 4.000 Teile in drei Schichten (teilweise auch an Wochenenden) und verzeichnet ein jährliches Wachstum von rund 15 Prozent – ein Erfolg, der vollständig in Westkanada verbleibt.
RAD Torque Systems, www.radtorque.com
Original article posted by Canadian Metalworking on September 11, 2024. Youtube video by Rad Torque.