Automatisierter Systemverbund überzeugt mit absoluter Präzision
Es war eine besondere Herausforderung: zunächst musste man die geeigneten Maschinen mit den entsprechenden Prozessen finden, um den Genauigkeitsvorgaben gerecht zu werden. Ursprünglich waren dafür unterschiedliche Maschinenkonzepte sowie für die Automation ein einfacher Palettenspeicher als Lösung geplant. Entwickelt hat sich das Projekt aber dann bei Siemens Ruhstorf zu einem Systemverbund mit drei Fräs-Drehzentren CP 2000 von HELLER und dem MLS (Multi-Level-System) von Fastems.
Bei der Fertigung der druckfesten, explosionsgeschützten Elektromotoren, sind umfassende Normen für den Schutz von Menschen, Maschinen und Umwelt zu erfüllen. Diese Normen sind bei Siemens Ruhstorf vor allem mit absoluter Präzision und höchsten Genauigkeiten verbunden. Genauigkeiten, die mit dem alten Maschinenpark allerdings nur noch mit einem erheblichen Zeit- und Kostenaufwand realisiert werden konnten. Darüber hinaus war für Rolf Gritl, Leiter Industrial Engineering bei Siemens deshalb auch eine wirtschaftliche Fertigung fester Bestandteil des Pflichtenheftes:
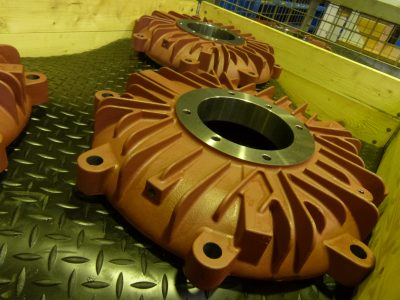
Höchste Normen sind mit absoluter Präzision verbunden. So bewegt man sich bei IT 6 und besser oder auch Durchmessertoleranzen von 9,0 µm. Das heißt, die Maschine muss 4,5 µm bringen.
Geplant waren dafür zunächst ein horizontales Dreh-Fräszentrum, sowie ein Fräs-Drehzentrum. Erste Versuche mit unterschiedlichen Anbietern machten allerdings schnell deutlich, dass die besten Ergebnisse mit den Fräs-Drehzentren CP 2000 von HELLER erzielt werden konnten.
So wurde zunächst in drei Maschinen dieser Baureihe plus einem MLS (Multi-Level-System) von Fastems investiert. Obwohl bei diesen Bauteilen das Drehen überwiegt, hat man sich in Ruhstorf für Fräs-Drehzentren entschieden. Frank Strothmann, Technologe bei Siemens sieht die Vorteile vor allem in der Automation: „Das Problem ist, dass man bei jeder Beladung für die Greifer- und Futterbeladung mindestens ein Spannmittel umrüsten muss. Bei unserer hohen Teilevarianz, den kurzen Laufzeiten aber auch relativ langen Werkzeugwechselzeiten gegenüber einem Bearbeitungszentrum sehe ich horizontale Dreh-Fräszentren nicht als wirtschaftliche Lösung.“
Auf Grund der großen Teilevielfalt, der geringen Losgrößen und dem Wunsch im Mixbetrieb Rüstzeiten zu reduzieren und just in time für die Montage fertigen zu können, wurde im weiteren Verlauf dieses Projekts dann allerdings die Automation immer mehr zum zentralen Thema.Und so wuchs aus der zunächst einfachen Palettenspeicher Lösung ein flexibles Fertigungssystem mit einem Multi-Level-System (MLS) von Fastems – genauer: ein MLS-LD (Low Duty) mit einer Tragkraft von 700 kg je Palette, das Platz für insgesamt 72 Maschinenpaletten bietet und zwei Hochgenauigkeits-Rüststationen integriert.
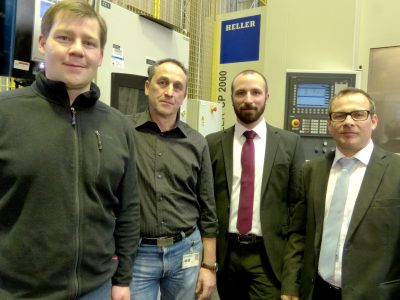
Frank Strothmann, Rolf Gritl, Sebastian Spanfelner und Holger Langer (v.l.n.r.): „Dieses Projekt war für uns alle eine Fülle an neuen Erkenntnissen. Aufgrund der geforderten Genauigkeiten und einer wirtschaftlichen Fertigung entwickelte sich ein völlig anderes, so nicht vorhersehbares Konzept.“
Integrierte Logistikabläufe für 20.000 Spindelstunden im Jahr
Das zentralisierte Paletten-Handling mit integrierten Be- und Entladestationen oder auch der Leitrechner von Fastems mit der Manufacturing Management Software MMS klingt zunächst nach Standard. Dem war nicht so, denn für Sebastian Spanfelner, Verkaufsleiter bei Fastems ist es schon allein wegen der Platzverhältnisse ein kundenspezifisches Fertigungssystem: „Für uns waren weder der gesamte Automationsprozess, die Reduzierung der Rüstzeiten noch die Schnittstellen zu HELLER ein Problem. Das MLS sorgt dafür, dass alle Logistikabläufe und der hierfür notwendige durchgängige Informationsfluss nahtlos in den Fertigungsprozess integriert werden. Um das System zu entladen oder mit Material zu versorgen, benötigt man aber vor den Rüststationen entsprechend Platz, den wir im Grunde nicht hatten. Es ist uns aber trotz des knappen Platzangebots, u. a. auch aufgrund einiger Säulen in der Halle, gelungen, die Fläche nahezu optimal zu nutzen.“
Nun ist es speziell beim zügigen Arbeiten an den Rüst- und Ladestationen für die Bediener aber wichtig zu wissen, was als nächstes zu tun ist. Die aktuellen Aufträge sind daher bereits vor Produktionsbeginn in der Software von Fastems (MMS) auf dem Leitrechner hinterlegt. MMS plant die Fertigung in diesem konkreten Fall über einen Zeitraum von drei Schichten im Voraus. Der Bediener erhält somit vor Schichtbeginn sämtliche relevanten Informationen über die gesamte Fertigungsplanung inklusive aller Rüstinformationen sowie die hierfür notwendigen Ressourcen. Siemens Ruhstorf verfügt somit über ein hochtransparentes Automationssystem u. a. mit Auftragsverwaltung, vorausschauender Fertigungsplanung und intelligenter NC-Programm- sowie Werkzeugverwaltung.
eit Ende 2014 ist man mit der Anlage nun produktiv und mittlerweile bereits bei einer Verfügbarkeit von 95 Prozent der Gesamtanlageangelangt. Holger Langer, Gebiets-Vertriebsleiter bei HELLER führt diese Ergebnisse einerseits auf die enge Zusammenarbeit mit Siemens, andererseits aber auch auf die intensive Entwicklungsarbeit zurück: „Dieses Projekt hat für uns zwei Jahre vor der Inbetriebnahme begonnen und war auch für uns bei diesen Genauigkeitsanforderungen eine echte Herausforderung. So haben wir beispielsweise festgestellt, dass die 1.000 min-1 beim Drehen sowie die hohen Drehzahlen beim Fräsen Verdunstungskälte erzeugen und deshalb eine Temperierung des Kühlmittels notwendig ist um die geforderte Prozessstabilität zu gewährleisten. Berücksichtigt man die Teilevarianz, die kleinen Losgrößen und den Systemverbund von drei Maschinen, ist diese Anlage sicher einzigartig. Wenn HELLER in kleinen Losgrößen und hoher Flexibilität gefragt ist, müssen wir dem Kunden aber auch über die Automatisierung einen Mehrwert bieten. Dazu verfügen wir über eine eigene Automationsabteilung, und im konkreten Fall war Fastems ein kompetenter und zuverlässiger Partner.“ Wie weit man mittlerweile die Rüstzeiten reduzieren und die Hauptzeiten bei Siemens erhöhen konnte, machen die inzwischen gemessenen 20.000 Spindelstunden im Jahr deutlich.
Siemens, der Standort Ruhstorf In Ruhstorf
In Ruhstorf produziert Siemens mit 1.200 Mitarbeitern explosionsgeschützte Motoren für industrielle Umgebungen wie Chemie, Petrochemie und Öl & Gas, Sondermotoren, Niederspannungsumrichter für spezifische Branchen (z. B. Marine, erneuerbare Energien) und Windgeneratoren. Die druckfesten Motoren SIMOTICS XP übertreffen so beispielsweise die grundlegenden Sicherheitsanforderungen. Die druckfeste Ausführung Ex d wurde speziell widerstandsfähig gegen Explosionsdruck entwickelt und verhindert, dass mögliche Zündungen innerhalb des Motors zur umgebenden Atmosphäre gelangen.
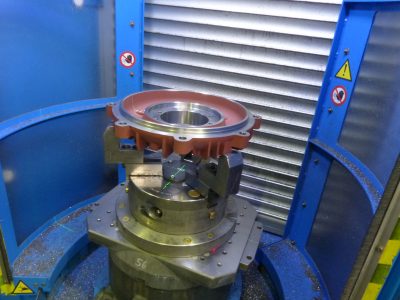
Eine der zwei Rüststationen. Die Bauteile lassen sich innerhalb eines Rundlaufs von 20 µm sicher ein- und ausschleusen.
Mannlose Schichten waren bei Siemens nie das Ziel. Vielmehr ging es darum, Rüstzeiten gegen null zu reduzieren.
Den Verantwortlichen war klar, dass dies mit klassischen Maschinen nicht zu erreichen ist. Heute arbeitet man mit fest auf Paletten montierten Spannvorrichtungen und je nach Bedarf wird das Bauteil auf die so vorgerüstete Palette gespannt. Untersuchungen bei Siemens haben ergeben, dass es aufgrund der durch die Bearbeitungsprozesse erzeugten Verdunstungskälte bei einer Raumtemperatur von 23° C und einer Temperatur des Kühlmittels von 20° C innerhalb weniger Minuten zu einer Abkühlung des Bauteils auf 18° C kommt.
Nebenbei bemerkt
Hinsichtlich der Prozesssicherheit ging es u. a. darum, wie man unter Berücksichtigung des teilautomatisierten Prozesses Mehrfach- oder Umschlagsmessungen trotz der vorhandenen Späne sicherstellt. Neben der nachhaltigen Entlastung und zusätzlichen Unterstützung des Bedieners bei wiederkehrenden Aufträgen ermöglicht die Software von Fastems die Steuerung und Überwachung von Produktionsprozessen nicht nur in Flexiblen Fertigungssystemen (FMS). MMS ist in der Lage, anhand der aktuellen Auftrags- und Fertigungssituation sowie aller hierfür zur Verfügung stehenden Ressourcen (darunter Rohmaterialien, NC-Programme, Werkzeuge sowie deren Standzeiten, etc.) eine vorausschauende Produktionsplanung vorzunehmen.
Contact
Siemens AG Industry Sector Mr. Rolf Gritl D-94099 Ruhstorf Tel.: + 49 8531/39-550 www.siemens.com |
Gebr. Heller Maschinenfabrik GmbH Mr. Marcus Kurringer D-72622 Nürtingen Tel.: +49 7022 77-5683 www.heller.biz |
Fastems Systems GmbH Gewerbering 5 D-47661 Issum Mr. Sebastian Spanfelner (Sales Manager Bavaria/Austria) Tel.: +49 162 4080051 www.fastems.com |
Was können wir für Sie tun?
Rufen Sie uns an oder senden Sie uns einfach eine kurze Nachricht.
„*“ zeigt erforderliche Felder an