Durchgängig digitalisiert –
Wie ein KMU seine komplette Produktion reorganisiert
Die Sistag AG hat die Potenziale von Bits und Bytes erkannt, denn das Schweizer KMU nahm im Zuge der Modernisierung eines flexiblen Fertigungssystems von Fastems seine Fertigung vor allem aus der Digitalisierungs-Perspektive unter die Lupe – mit durchweg interessanten Erfahrungen und ambitionierten Plänen.
Die weltweit agierende Sistag AG mit Sitz in Eschenbach (Kanton Luzern) stellt Armaturen für die Wasserversorgung und Industrie her. „Darüber hinaus sind wir auf Flachplattenschieber spezialisiert, die unter dem Markennamen Wey Valve bekannt sind und u.a. in der Petrochemie, Ölförderung und im Bergbau eingesetzt werden. Unsere mechanische Fertigung hier am Standort stellt mit rund 165 Mitarbeitern pro Jahr rund 20.000 Schieber her“, erklärt Manuel Schmidlin, Leiter Fabrikation bei Sistag.
Spezialist mit hoher Automatisierung
Wie viele andere Schweizer KMU hat auch Sistag mit hohen Kosten zu kämpfen. Manuel Schmidlin: „Grund und Boden sind teuer; die Personalkosten sind hoch. Wir finden überdies kaum Fachkräfte für die Produktion und bilden daher verstärkt selbst aus.“ Um die Produkte wirtschaftlich vertreiben zu können, müssen die Maschinen bei Sistag quasi non-stopp laufen. „Wir haben zudem den Vorteil, im Bereich der Sonderschieber besonders stark zu sein. Und aufgrund des relativ hohen Automatisierungsniveaus können wir uns auch preislich im Markt behaupten“, so Schmidlin.
Modernisierung mit Fokus auf Digitalisierung
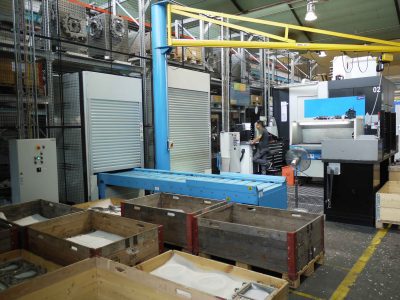
Das MLS-MD (Multi Level System-Medium Duty) wurde 2022 komplett mechanisch und auch softwareseitig auf den neuesten Stand gebracht.
Die Gehäuse als Kernkomponente für die Flachplattenschieber werden auf zwei horizontalen Bearbeitungszentren gefertigt. 2005 investierte das Unternehmen in ein flexibles Fertigungssystem von Fastems, genauer in ein Multi-Level-System (MLS), an dem zunächst eine OKK HM 630 angebunden wurde. 2010 wurde das System auf eine Gesamtlänge von 35m erweitert und eine zweite OKK gleichen Typs kam hinzu.
2022 entschloss sich Sistag, das MLS zu modernisieren. Hierzu Manuel Schmidlin: „Das Betriebssystem der Steuerungssoftware sowie die entsprechende Elektronik liefen noch auf 32 Bit und waren im Prinzip „End of Life“. Im Zuge der Umrüstung auf ein 64-Bit-System nahmen wir dann ein komplettes Retrofit sowohl steuerungsseitig als auch mechanisch vor.“ Da Sistag außerdem seit rund vier Jahren eine konsequente Digitalisierungsstrategie verfolgt, wurde nicht nur das FFS softwareseitig mit der Manufacturing Management Software (MMS) von Fastems auf den neuesten Stand gebracht, sondern das Augenmerk insbesondere auf die Digitalisierung der gesamten Produktion gerichtet.
Keinen Überblick über Kapazitäten und Auslastung
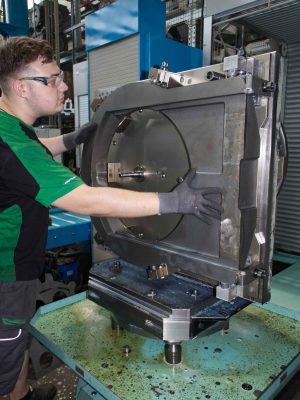
Aktuell verfügt das FFS über drei Be- und Entladestationen sowie zwei Materialstationen und bietet auf zwei Ebenen Platz für insgesamt über 74 Maschinenpaletten und 82 Materialpaletten.
Nach Aussagen von Manuel Schmidlin ist das Unternehmen in seiner 60-jährigen Geschichte vor allem historisch gewachsen.
Sätze wie „Das haben wir immer so gemacht.“ hat der Fertigungsleiter daher schon oft gehört.
„Unser Projektgeschäft hat jedoch deutlich zugenommen.
Wenn ein Kunde heute Schieber bestellt, dann sind das nicht drei oder vier, sondern gleich 400 oder 500. Mit unserer vorhandenen Infrastruktur konnten wir derart große Aufträge nicht von Anfang bis Ende sauber planen. So hatten wir u.a. große Mühe, unsere Maschinenkapazitäten im Griff zu halten, da wir noch mit Listen arbeiteten und im Grunde keinen Überblick darüber hatten, was zu welcher Zeit passierte und wo die Prioritäten lagen.
Unser Ziel ist es daher, mit der MMS als zentrales MES unsere gesamte Produktion zu steuern.“
„Terra Incognita“ der Fertigungsorganisation
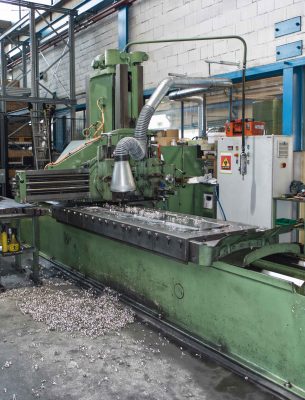
Fester Bestandteil der Digitalisierungsstrategie: Auch ältere, nicht netzwerkfähige Maschinen, wie dieser Metallhobel, werden dank WCO fester Bestandteil des MES und damit der Gesamtorganisation.
Die MMS von Fastems bietet hierzu sämtliche Voraussetzungen, denn sie zählt derzeit wohl zu den leistungsfähigsten Lösungen zur Planung, Ausführung und Überwachung einer automatisierten spanabhebenden Fertigung.
Die MMS plant u.a. mit Systemen wie das MLS automatisch die Produktion bis zu 96 Stunden im Voraus und berücksichtigt hierbei sämtliche erforderlichen Ressourcen, wie z. B. Rohmaterialen, NC-Programme und Werkzeuge inklusive deren Standzeiten.
Manuel Schmidlin weiß allerdings nur zu gut, dass für eine durchgängig planbare Fertigung auch Stand-Alone-Maschinen, manuelle Arbeits- und Prüfplätze etc. in die Digitalisierung einbezogen werden müssen.
Keine einfache Aufgabe, denn diese Bereiche sind bislang oftmals noch eine „Terra Incognita“ in der Fertigungsorganisation.
Digitale Planung der nicht-automatisierten Fertigung
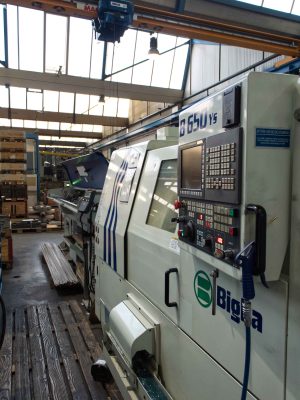
Dieses Dreh-/Fräszentrum gehört zu den Maschinen, die über eine Netzwerkschnittstelle in die MMS eingebunden werden können und somit eine lückenlose Planung, Ausführung und Überwachung der Produktion ermöglichen.
Das soll sich bei Sistag allerdings mit der Implementierung des MMS-Softwaremoduls WCO ändern.
„Wir wollen den gesamten Produktionsfluss in der MMS abbilden und hierbei jeden einzelnen Schritt, vom Zuschnitt auf einer Lasermaschine, über das Hobeln, Fräsen, Bohren und Schleifen, bis hin zur Qualitätsprüfung mit einbeziehen“, so Schmidlin. Und WCO spielt hierbei eine entscheidende Rolle.
WCO steht für „Work Cell Operations“ (Arbeitszellen-Operationen) und ist eine Lösung mit der sich auch nicht-automatisierte Maschinen und Arbeitsprozesse digitalisieren lassen. Das Modul ermöglicht es hierbei u.a., die Kapazitäten und Arbeitsreihenfolgen von Einzelmaschinen sowie Arbeitseinheiten (Zellen) zu organisieren und deren Auslastung zu erfassen. WCO integriert für Einzelmaschinen eine NC-Programm- und Werkzeugverwaltung, wobei sich die Software sowohl als eigenständige Lösung als auch in Kombination mit einer Paletten- oder Teileautomatisierung einsetzen lässt. In einem ersten Schritt plant Sistag die Implementierung von insgesamt acht WCOs. Weitere sollen folgen.
Vollständige Einbindung in die Gesamtorganisation
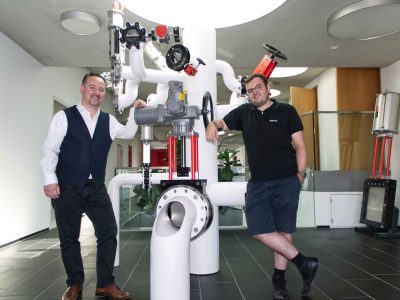
Gennaro Teta, Sales Manager von Fastems für die Schweiz (links), und Fertigungsleiter Manuel Schmidlin arbeiten im Digitalisierungsprojekt der Sistag AG eng zusammen.
Manuel Schmidlin vermittelt einen konkreten Eindruck von den Potenzialen des MMS-Moduls: „Jedes WCO steht für eine Stand-Alone-Maschine oder einen Arbeitsplatz, wobei sich auch mehrere Maschinen in einem WCO gruppieren lassen. So haben wir bspw. die Drehmaschinen einer Abteilung in einem WCO zusammengefasst. Innerhalb der WCO-Gruppierungen können wir dennoch die Aufgaben an jeder Maschine verteilen und koordinieren. Alle weiteren netzwerkfähigen Stand-Alone-Maschinen werden ebenfalls direkt mit der MMS verbunden. Darüber hinaus haben wir aber auch ältere Maschinen, wie z. B. Metallhobel, die sich als vergleichsweise einfache Fertigungslösungen ebenfalls für die Einbindung in die Gesamtorganisation mit den WCOs anbieten. Weil die Maschinen nicht netzwerkfähig sind, erhalten die Mitarbeiter ein Tablet, um die erforderlichen Produktionsdaten und Infos an die MMS zu übertragen.“
„Das kann ein ERP-System nicht liefern“
Die MMS plant mit den WCOs auf Basis der Auftragsdaten aus dem ERP-System, ähnlich wie für das FFS, automatisch die Produktion in den einzelnen Abteilungen und vergibt anhand der Endtermine Prioritäten. Die Mitarbeiter an den Maschinen erhalten dann digitale Listen, die sie gemäß den Prioritäten abarbeiten können. Die entsprechenden Rückmeldungen an die MMS, z. B. wann eine Maschine gerüstet wird oder ein Fertigungsauftrag startet, erfolgen entweder direkt von einer netzwerkfähigen Maschine oder in anderen Fällen über die Tablets.
„Wir bleiben hierbei stets flexibel“, betont Schmidlin, „denn ich kann einzelne Aufträge umschichten und neue Prioritäten vergeben, falls erforderlich. Das war früher so nicht möglich. Ich sehe hierbei jederzeit die gesamte Produktionsplanung und die Fortschritte, die Auslastung der Maschinen und welche Aufträge als nächstes kommen, also sämtliche organisatorisch relevanten Informationen und Daten, die ein ERP-System in dieser Form nicht liefern kann.“
Hohe Transparenz über die gesamte Produktion
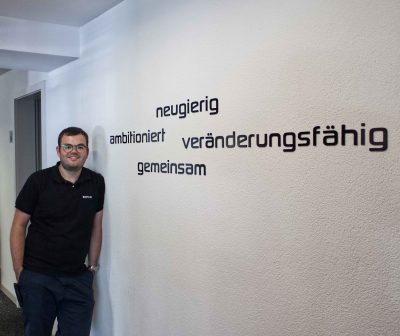
Manuel Schmidlin, Leiter Fabrikation der Sistag AG: „Wir wollen die gesamte Produktion über MMS als zentrales MES abbilden. Schon heute sind wir mit weniger Maschinen und Mitarbeitern deutlich produktiver. Und die wachsende Transparenz versetzt uns in die Lage, unsere Fertigung sehr gezielt zu optimieren.“
Damit die Digitalisierungs-Strategie mit der MMS und den WCOs wirklich greift, muss aus Sicht des Fertigungsleiters jedoch wesentlich früher angesetzt und zunächst im ERP-System „aufgeräumt“ werden, um alle erforderlichen Informationen in korrekter Form an die MMS zu übertragen.
„Das hat schon eine Weile gedauert. Aber die Mühe lohnt, denn wir erhalten ein immens hohes Maß an Transparenz mit detaillierten Daten, selbst über nicht-automatisierte Maschinen und Prozesse. Ein besonderer Vorteil ist in diesem Zusammenhang zudem, dass wir vom MMS zum ERP nur eine einzige Schnittstelle benötigen, wobei die MMS dann als MES fungiert. Mit Blick auf das weiterhin wachsende Projektgeschäft ist das ein riesiger Fortschritt, weil wir über eine sehr hohe Informationsdichte mit validen Betriebsdaten verfügen, die es uns wiederum ermöglichen, genauer zu kalkulieren, sodass wir ggfs. die Stammdaten im ERP anpassen können, wenn diese nicht übereinstimmen.“
Weitere Investitionen in Automatisierung
Flankiert wird die Digitalisierungsstrategie durch den weiteren Ausbau der Automatisierung, z. B. im Dezember 2023 durch einen FPC-3000 (FPC: Flexible Pallet Container) von Fastems. Parallel hierzu investiert Sistag in eine weitere OKK, denn Maschinen ohne Automatisierung soll es in der Fertigung zukünftig nicht mehr geben.
„Vielfach haben Unternehmen mit einer Automatisierung von Fastems und der MMS schon eine Lösung, die hinsichtlich der Fertigungstransparenz keine Wünsche offenlässt. Sie vergessen hierbei aber zumeist sämtliche Fertigungskapazitäten im Umfeld der Automatisierung. Wir haben das erkannt. Schon heute sind wir mit weniger Maschinen und Mitarbeitern deutlich produktiver. Und die stetig wachsende Transparenz versetzt uns in die Lage, die vollständige Fertigung sehr gezielt zu optimieren“, so das Fazit von Manuel Schmidlin.