Intelligente Automatisierung ermöglicht eine auftragsgesteuerte und nachhaltige Fertigung bei Wärtsilä

“Wir setzen unsere Ziele in die Tat um. Unser Ziel ist es, den maritimen und Energiesektor zu dekarbonisieren, und dabei machen wir unsere eigenen Prozesse so nachhaltig wie möglich. Wir produzieren ausschließlich auf Bestellung und haben unseren Einzelstückfluss so optimiert, dass er genauso effizient ist wie die Massenproduktion. Das bedeutet für uns hohe Maschinennutzung, erstklassige Qualität ab dem ersten Lauf und kürzeste Lieferzeiten für unsere Kunden.”
So beschreibt Juha Päivike, Director der Logistikkette bei Wärtsilä, die ambitionierten Ziele und die zukunftsweisende Strategie des Unternehmens im Wärtsilä Sustainable Technology Hub (STH) – dem neuesten und größten Produktionsstandort des Unternehmens, der 2021 in Vaasa, Finnland, eröffnet wurde. Mit einem klaren Fokus auf die globalen Klimaziele zur Reduzierung der Emissionen im Seeverkehr und der steigenden Nachfrage nach erneuerbaren Energien unterstützt Wärtsilä seine Kunden dabei, diesen Wandel bestmöglich zu nutzen.
„Jedes dritte hochseetaugliche Schiff ist mit Wärtsilä-Technologie ausgestattet – für eine nachhaltigere Zukunft auf den Weltmeeren.“
„Unsere Lösungen werden hauptsächlich zur Stromerzeugung in Schiffen und als Regelleistung in Kraftwerken eingesetzt. Die Lebensdauer eines Motors kann bis zu 40 Jahre betragen – um die Klimaziele in den nächsten 25 Jahren zu erreichen, müssen wir jetzt handeln“, sagt Päivike und fügt hinzu: „Letztes Jahr haben wir den ersten Methanolantrieb an einen Kunden geliefert, und heute besteht bereits 25 % unserer Auftragspipeline aus Motoren, die mit erneuerbaren Brennstoffen betrieben werden.“
Wärtsilä hat einen bemerkenswerten Geschäftswandel vollzogen, der das Unternehmen dazu brachte, ihre Fertigung zu überdenken, um Forschung und Entwicklung zu beschleunigen und Prozesse für den maximalen Kundennutzen zu optimieren. In über 30 Jahren Partnerschaft mit Fastems zeigt die Fertigungsanlage im STH eindrucksvoll, wie Prozessinnovation, flexible Automatisierung und ein hoher Integrationsgrad zu mehr Effizienz und Qualität in der Produktion führen. Wir haben Rami Hakala, Senior Development Manager bei Wärtsilä, gefragt, was die Fertigung im STH von den früheren Prozessen unterscheidet:
„Wir haben eine lange Geschichte mit Fastems flexiblen Fertigungssystemen, daher hatten wir bereits automatisierte Bearbeitungsprozesse sowie viele andere Prozesse wie Fertigung, Waschen und Messen. Diese hatten wir jedoch als separate Zellen automatisiert. Jetzt haben wir alle Prozesse in ein einziges System integriert, bei dem wir einfach Rohmaterial zuführen und fertige Komponenten erhalten. Und das nicht nur für einige wenige Teile – sondern für über 60 verschiedene Komponenten.“
Zwei nahtlos integrierte Systeme für die effiziente Fertigung von über 60 verschiedenen Komponenten
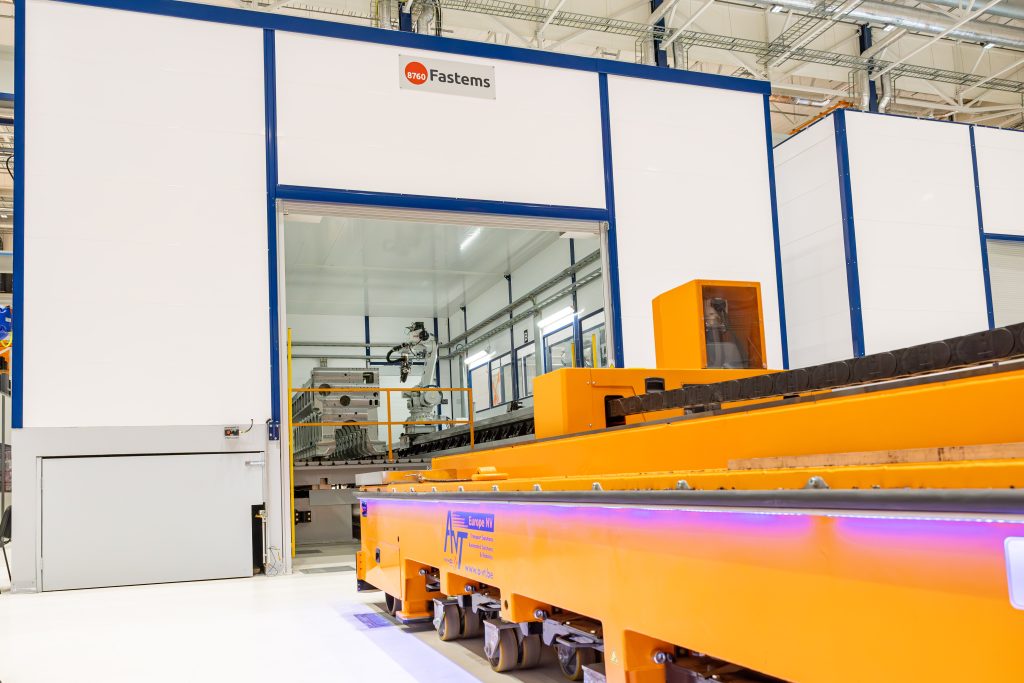
Im Wärtsilä STH werden Motoren und Komponenten für drei Schlüsselbereiche gefertigt: neue Bestellungen, Ersatzteile für im Einsatz befindliche Motoren und F&E-Anwendungen. Auf der 60.000 m² großen Produktionsfläche kommen zwei hochmoderne, flexible Fastems-Fertigungssysteme zum Einsatz: Das AGV-FMS für die Herstellung von Motorblöcken und das Multi-Level-System für die Fertigung von Komponenten, die an diese Blöcke montiert werden. Beide Systeme werden von der leistungsstarken Manufacturing Management Software (MMS) gesteuert, die speziell dafür entwickelt wurde, hochvariantenreiche Fertigung effizient zu planen und zu betreiben.
„MMS ruft automatisch Kundenaufträge aus unserem ERP ab und plant dann die Produktion beider Systeme, sodass jeder Motorblock und seine Komponenten just-in-time für die Montage bereit sind. Wir müssen keine Teile auf Lager produzieren, und unsere Fertigung bleibt flexibel, wenn die Nachfrage schwankt. Zudem haben wir den Qualitätssicherungsprozess in beiden Systemen integriert, um höchste Qualität und vollständige Rückverfolgbarkeit für jedes Bauteil zu gewährleisten“, erklärt Tero Kujamäki, Manufacturing Technology Development Manager bei Wärtsilä.
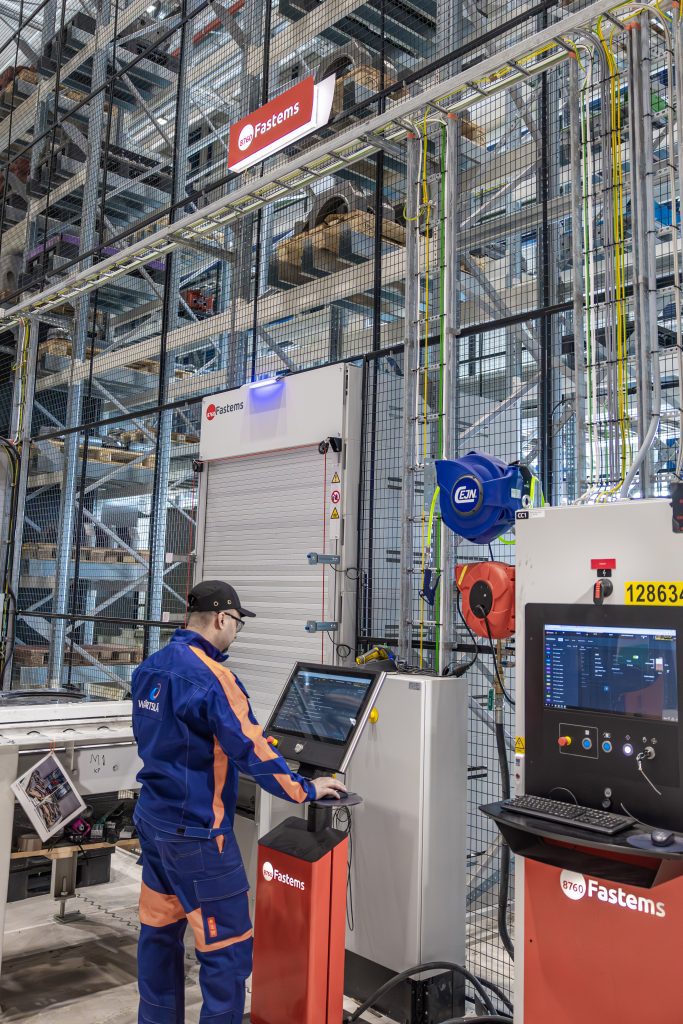
„Besonders stolz sind wir auf die neue ‚Fast Lane‘ für dringende Kundenaufträge. Unser Produktionssystem passt sich automatisch an Änderungen an, sodass wir einfach die Eilaufträge im ERP priorisieren und MMS den Produktionsplan so anpasst, dass wir unsere Lieferziele einhalten. Sollte ein Ziel nicht erreicht werden können, informiert uns MMS rechtzeitig, damit wir Alternativen prüfen können“, sagt Hakala.
“Jetzt haben wir alles in ein einziges System integriert, bei dem wir einfach nur das Rohmaterial einbringen und die fertigen Teile herausbekommen.”
Ein weiterer großer Automatisierungsschritt bei Wärtsilä im STH ist die Automatisierung der Werkzeugbereitstellung und -datenverwaltung mit dem Fastems Gantry Tool Storage (GTS). Das GTS-System speichert über 750 Schneidwerkzeuge zentral und plant den Einsatz der Werkzeuge basierend auf dem Produktionsplan. Just-in-time liefert es jedes Werkzeug an sechs verschiedene Bearbeitungszentren. Ist ein Werkzeug abgenutzt, wird es automatisch zur Nachbearbeitung in den Werkzeugraum zurückgebracht. Zudem übermittelt das GTS-System automatisch die Werkzeugversatzinformationen vom Voreinstellgerät an die Maschinen.
„Unsere Werkzeugbediener wissen immer im Voraus, welche Werkzeuge nachbearbeitet werden müssen, um die Spindeln am Laufen zu halten. Dieses System ermöglicht es uns, Werkzeuge zwischen den Maschinen zu teilen, anstatt jedes Bearbeitungszentrum mit einem vollständigen Werkzeugsatz auszustatten“, sagt Kujamäki. „Wir können auch die Werkzeugnutzung überwachen und bei Bedarf zusätzliche Werkzeuge für Engpässe bereitstellen.“
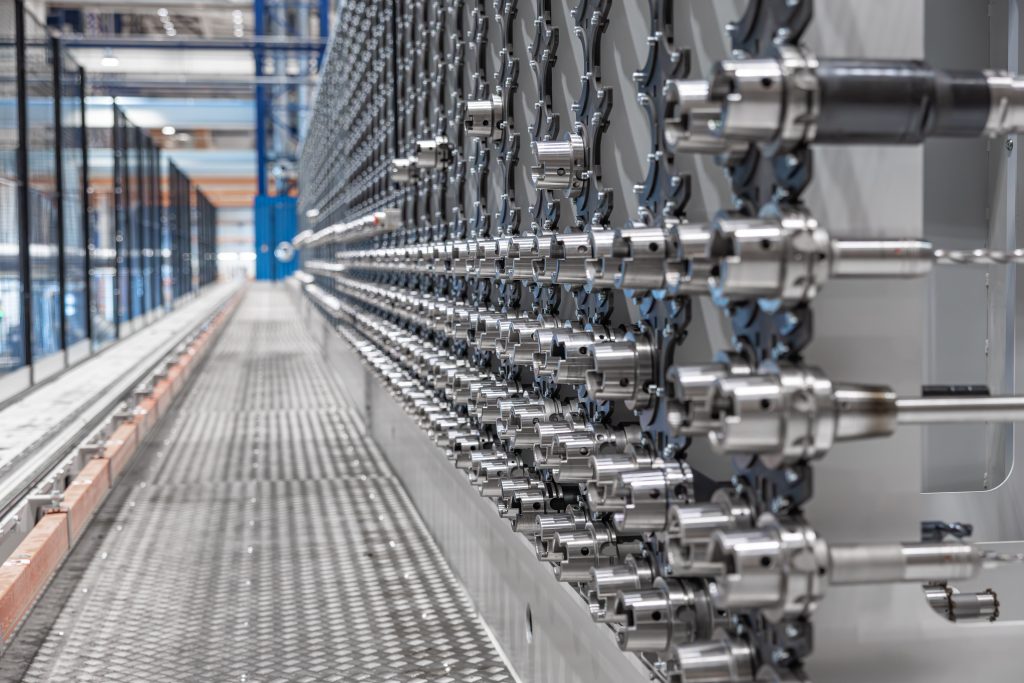
Wärtsilä ist rund um die Uhr für seine Kunden da – und das gilt ebenso für die Produktion. Die Tagschichten bereiten alles vor, während die Abend- und Nachtschichten mit nur wenigen Mitarbeitern eine Überwachungsrolle in der mannlosen Produktion übernehmen. „Wir setzen auf spezialisierte Rollen statt traditioneller Maschinenbediener, sodass sich unsere Mitarbeiter auf die Weiterentwicklung der Produktion konzentrieren können. Das ist ein entscheidender Faktor für unsere hohe Mitarbeiterbindung“, sagt Hakala, der seit über 20 Jahren bei Wärtsilä tätig ist. „Mit unserem großartigen Team und starken Partnern haben wir dieses System weiterentwickelt – und nun wollen wir sehen, wie viel mehr wir noch daraus herausholen können!“
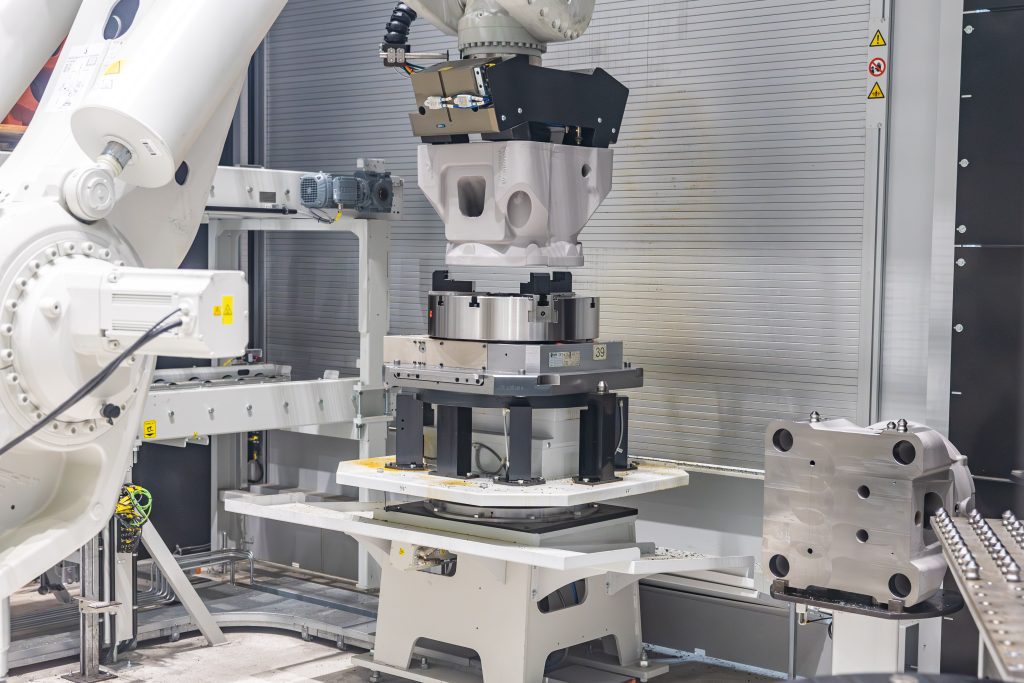
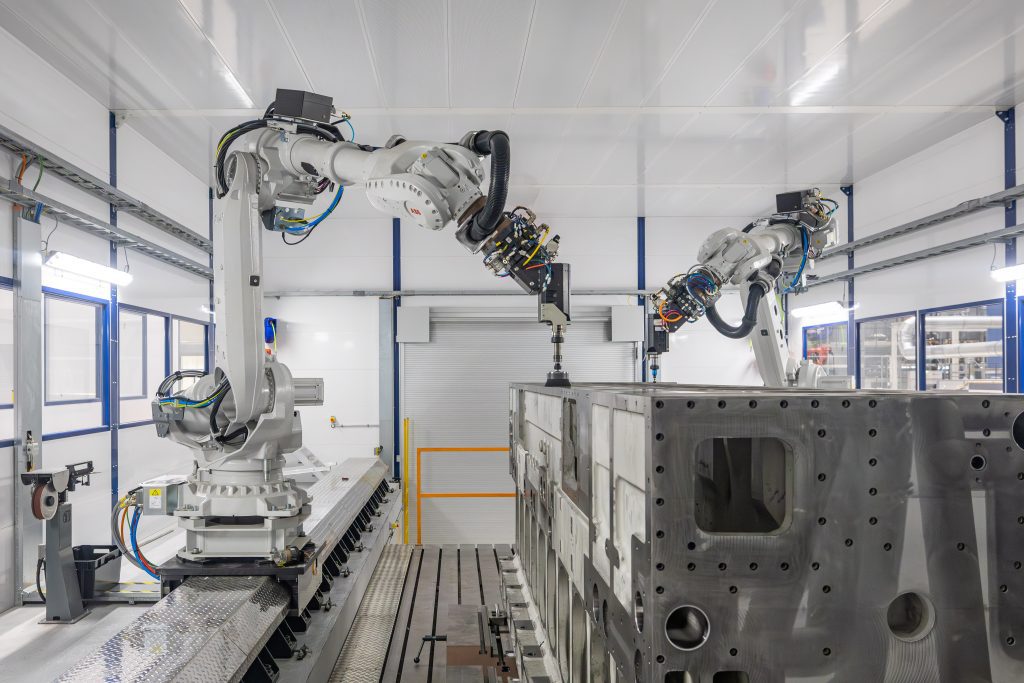
Fastems‘ Systeme bei Wärtsilä STH
Multi-Level System | MLS
Mit diesem flexiblen Fertigungssystem produziert Wärtsilä über 60 Typen von Pleueln und Zylinderköpfen für ihre Motoren.
Die Bearbeitungszyklen reichen von 10 Minuten bis zu 8 Stunden.
Das System umfasst:
- Fünf HELLER-Horizontal-Bearbeitungszentren
- Regalbediengerät für den Palettenwechsel
- 60 Maschinen- und 124 Materialpaletten
- Werkzeugbereitstellung (auch für eine große Portalmaschine im AGV-FFS)
- Roboter-gestütztes Einspannen von Teilen in Paletten (ALD)
- Automatisiertes Waschen, Entgraten und Markieren
- Automatisierte Qualitätskontrolle (CMM)
- Automatisierte Vormontage
AGV-FFS

Die großen Motorblöcke mit einem Gewicht von bis zu 60.000 kg werden in diesem FFS gefertigt, das anstelle eines traditionellen Krans ein großes AGV als Transfervorrichtung nutzt.
Das System umfasst:
- WaldrichSiegen-Portalmaschine
- Ein AGV zum Palettentransport
- Drei Beladestationen zum Einspannen der Motorblöcke in die Maschinenpaletten
- Lagerplätze für vier Paletten
- Roboter-gestütztes Finishing
- Roboter-gestützte Montage
- Optische Messung (nicht von Fastems)
- Waschanlage (nicht von Fastems)